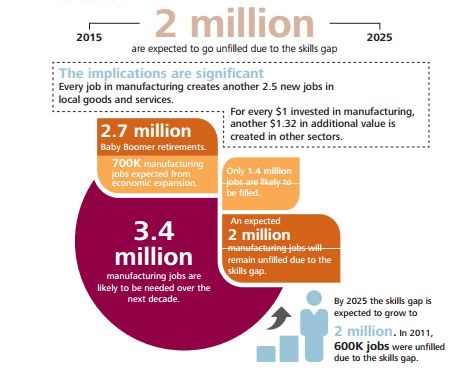
If you work in the manufacturing industry you have heard of the Skills Gap. This refers to the current and growing shortage of skilled workers in the manufacturing sector. This problem is not isolated to the United States, this is a worldwide problem. There are several numbers thrown around, these are all estimates, but they are scary. We are looking at having a shortage of about 500,000 skilled workers by the year 2020. Some studies suggest a shortage of 2 million skilled workers as early as 2025. This shortage is certainly a challenge for employers and the manufacturing industry in general; however, it also provides great opportunity for many.
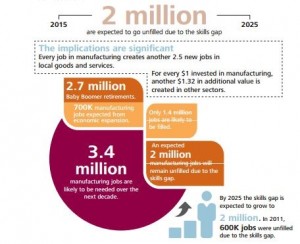
Over the next 10 years nearly 3.5 million manufacturing jobs will likely be needed and 2 million are expected to go unfilled to the skills gap.
Source: Deloitte Issue 16
The skills gap refers to the shortage of job applicants for manufacturing jobs with proficiency in Science, Technology, Engineering and Math (STEM). The lack of these skills hits many jobs, some of the most affected are: Engineers, researchers, machinists, and welders.
Several factors are creating this shortage, the main ones are:
1. Average age of skilled workers – the baby boomers are retiring and are taking with them a wealth of knowledge. Many more workers are retiring that those entering the workforce with comparable skills.
2. Perception of manufacturing as a “dirty” industry – when most kids and young adults think about manufacturing they associate it with getting dirty and requiring a great deal of physical activity. They favor desk jobs which utilize software and technology over shop floor positions regardless of pay. There is plenty of technology in manufacturing, we just need to do a better job of changing the perception of our industry for the young generations.
3. Poor on-the-job training – Only a few companies have excellent training programs for their employees. This is a must to stay on top of the latest technology and stay competitive. Investing in employees also builds up employee morale and reduces turnover.
4. Poor education of youth – Out of the over 3 million yearly high school graduates a significant amount express interest in STEM careers; however, only 16% meet the required level of proficiency.
All this seems like bad news. And it is; however, there are plenty of programs in place and many more coming to address this skills gap issue. As with almost all challenges this one presents many opportunities to both employers and skilled workers.
If employers can set up excellent in-house training programs they can increase skills and retain qualified skilled workers. This translates into less turnover and lower costs. It will also help keep current with technology and be more cost competitive in the market.
For individuals seeking a career in manufacturing this is also an opportunity. There will be plenty of jobs. However, it is important to keep in mind that simply because there are vacancies does not mean that employers are lowering standards. As a matter of fact most employees are making their standards higher. Those who excel in their trade will command higher salaries and increase job security.
Is your company already hurting due to the skills gap? What are you doing about it?
Great article! I am a pressure vessel welder building production equipment used downstream of compression. The company I work for is going under due to falling oil prices. They preached the importance of cross training but never put it in effect for the sake of reaching deadline numbers. A select few would be spoon fed, burped and diaper changed while others who hungered to learn more were told to pick up the pace so numbers looked good. I am a team player who wanted to learn in order to be more versatile in the shop and for self enrichment. For other companies that claim to cross train and don’t follow through —- shame on you! I hope your doors close like the place I work will next month. The time wasted on trying to hire someone to fill a position far exceeded what it would have taken to train from within. People are loving lower gas prices but over 250,000 people like me have to transition to something else. Anyhow GREAT ARTICLE people need to read.
Stan, sorry about your company. And you are right, it is unfortunate that deadlines trump everything else. We see it every day where in attempts to meet deadlines even safety violations are overlooked. Being a pressure vessel welder we are sure you’ll land another job soon. And hopefully with an employer that is more interested in long terms success rather that short term results. Good luck!
Is useful