
Today we continue our series which discusses some of the major considerations when developing a welding procedure. Last week we covered selecting the right welding process. Today we’ll look at selecting the right filler metal. The following is an excerpt from our guide: Welding Procedure Development for Non-Welding Engineers.
Selecting the filler metal should not be a trivial matter. The easy way out is to select a filler metal that has matching strength, meaning that the minimum specified tensile strength of the filler metal matches that of the base metal. However, this is not always the best option. In some cases it may be beneficial to use undermatching filler metals. There are many factors to consider when selecting the right filler metal. Understanding requirements in the areas of strength, ductility, wear resistance, corrosion resistance, in-service demands, cost and productivity is essential.
Below are aspects that must be taken into consideration when selecting a filler metal for the welding procedure being developed.
Matching Strength
The American Welding Society does not formally define the term “matching strength.” However, what is accepted in the industry is that matching strength simply means that the filler metal’s minimum specified tensile strength will be equal to or greater than that of the base metal. Determining whether or not matching strength is required depends on the type of joint being welded and the loading conditions experienced in service. Typically, matching strength is required in complete joint penetration (CJP) groove welds in tension applications. However, it is not always the most conservative or economical choice.
Codes will sometimes provide matching filler metals. For example, in AWS D1.1 Structural Welding Code – Steel, you will find in the Prequalification clause (Clause 5 in the latest edition – 2020) matching filler metals. If the code recommends a particular filler metal you must not immediately assume it is the best choice. Understanding the requirements of the weld is important as using an undermatching filler metal may be advantageous.
Undermatching Strength
Rather than focusing on when to use matching filler metals our focus should be on when to use undermatching filler metals. This may sound like a bad idea to some. Why would we want to use a filler metal that is weaker (in terms of tensile strength) than the base metal? The answer is: when the welded connection can benefit from it. As tensile strength of base metals and filler metals goes up, ductility goes down. This means that in highly restrained joints the probability of cracking goes up. If we use an undermatching filler metal the weld will have higher ductility and will be better able to handle residual stresses without cracking. Whenever you are welding high strength steel, consider the use of undermatching filler metal on fillet welds and partial joint penetration (PJP) welds.
In many of these cases, especially fillet welds, we can use undermatching filler metals without having to increase the weld size. Other times, when the weld is transferring all of the stress we can still use undermatching filler metals and simply increase the size of the weld. This would require more filler metal and more welding time than if we used a matching strength filler metal, but by using an undermatching filler metal we eliminate or reduce cracking susceptibility which in the long run will save us a lot of money.
The same can be said of PJP welds. The weld can be made bigger to compensate for the strength required but still have higher ductility than if a matching filler metal was used.
Welding engineers must understand the design concerns of using matching and undermatching filler metal. For most structural steels using matching filler metal is a safe option. However, once you start getting into high strength steels consider the use of undermatching filler metals.
Expected Service Conditions
Understanding the in-service conditions and requirements of the weld, such as service temperature, exposure to corrosive elements, exposure to wear and impact, and other factors is very important in selecting the right filler metal.
An example of this is the use of weathering steels. Weathering steels are alloyed with copper, nickel and chromium. These elements provide the necessary atmospheric corrosion resistance by facilitating the formation of a protective layer of rust which does not penetrate the surface of the steel.
A matching filler metal for ASTM A588 (a weathering steel) would be one with a minimum specified tensile strength of 70ksi. However, this particular application requires a filler metal that will also provide the same atmospheric resistance. In this case, the use of a wire containing at least 1% nickel is required. In the case of GMAW an ER80S-Ni1 would be a good option. When multiple passes are required, a filler metal that closely matches the base metal may be necessary.
Low temperature service conditions may also require special filler metals. When specific charpy v-notch (notch toughness, or resistance to crack propagation) values are required, the filler metal to be used may not necessarily be a matching filler metal. Manufacturers of filler metal will provide this information in their certificates of conformance. This will let you know if the filler metal being considered will meet the required notch toughness values.
Figure 6.1 – Excerpt from a certificate of conformance for Lincoln Electric’s Super Arc L-56 GMAW filler metal (ER70S-6) and additional graphs for further explanation. The green oval shows the location of the toughness values. In this case the test was done at -20F [-29C]. If in-service conditions will be at much lower temperature a different filler metal may be needed.
A typical requirement may be “50 ft-lb at -40F.” In this case, Super Arc L-56 would not be an option. It may very well be able to achieve 50 ft-lb at -40F, but the certificate of conformance does not provide values for toughness at that temperature. At this point you would have two options: (1) perform a welding procedure qualification tests and test toughness at -40F, or (2) find a filler metal that has already been tested at -40F and provides a minimum of 50 ft-lb at that temperature.
Stress Relieving Applications
Stress relieving is a type of post weld heat treatment which is used to reduce residual stresses that are present after welding. This is done by carefully controlling the heating of the part to a specific temperature, holding it for a specific amount of time and then controlling the cooling rate.
Stress relieving is also used to reduce distortion and to control dimensional stability and tolerances.
It is important to know that stress relieving typically reduces weld strength by 10 to 15%. Therefore, if an electrode classified in the “as-welded” condition is stress relieved, the final tensile strength could fall below the minimum classification tensile strength.
Hardfacing Applications
If the in-service application demands resistance to abrasion, impact or other type of wear, then a filler metal with resistance to these conditions must be selected.
If the weld will experience wear, abrasion or impact, then a filler metal that produces a specified hardness level must be selected. This hardness level is typically specified based on the expected type of wear, impact or abrasion.
At times you may be welding abrasion resistant (AR) plates as is typically done with bulldozer and backhoe buckets. In this case, the weld is just attaching the plate to the bucket and does not need to have the same abrasion resistance as the AR plate. In situations like this, the use of undermatching filler metals is recommended.
The above are some of the main considerations when selecting the right filler metal. As you can see, this is not a trivial matter. Next week will be evaluating another key component of welding procedure development: Selecing your welidng parameters (wire feed speed, amps, volts, travel speed, etc.).
Reference: Welding Procedure Development for Non-Welding Engineers
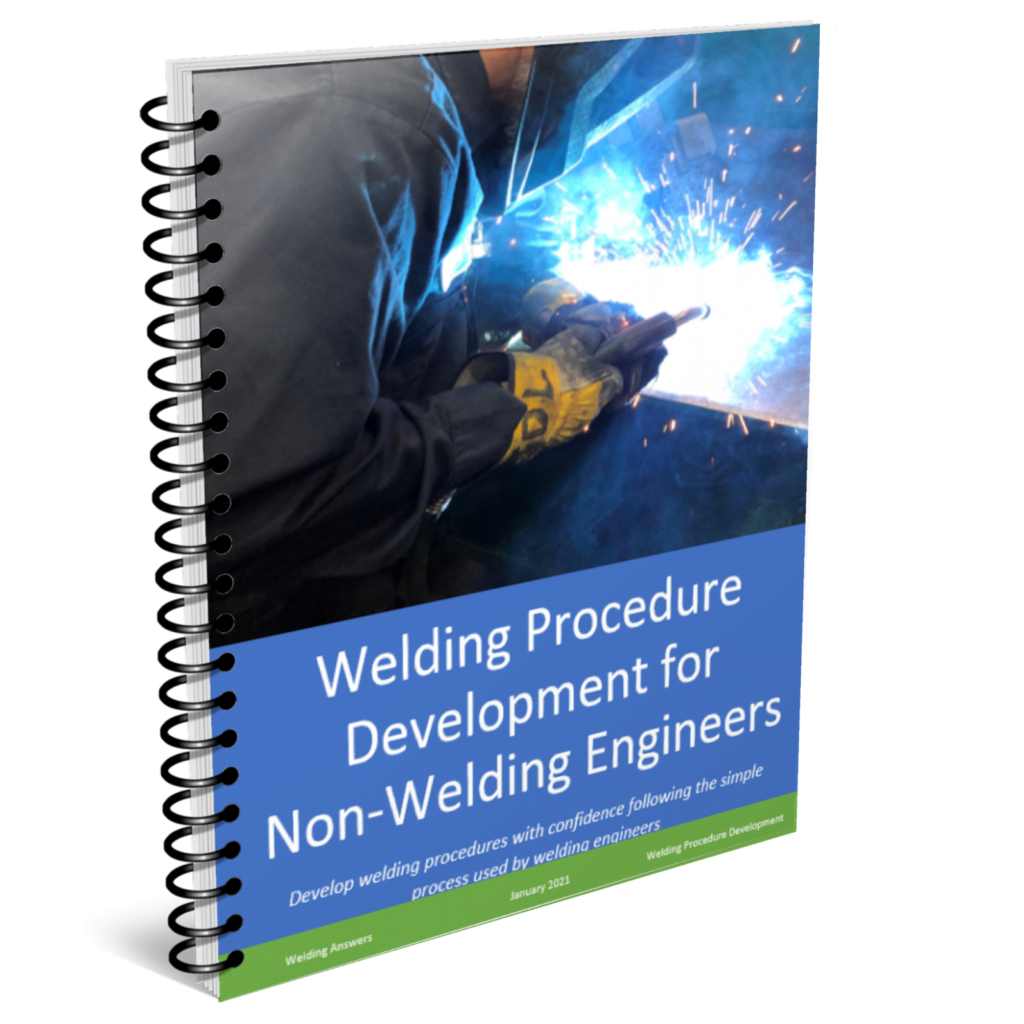