
Waveform control is the ability of a welding power source to affect heat input, droplet shape and size, penetration, bead shape and toe wetting by the use of microprocessor controls which manage the welding output. Advances in waveform control technology over the past two decades have provided the ability to weld tough materials successfully. One of the benefits of a power source that can control the welding output via waveforms is that the welder skill necessary to make certain welds may not need to be as high. This claim has been supported over and over again and this is why companies like Lincoln Electric, Miller Electric, OTC, Fronius, ESAB and many more spend millions of dollars in research & development to continue to improve their waveform technology.
The most commonly known waveform is pulse. In pulse, a welding power source will switch between a high and a low current (amperage) at frequencies between 20 to 200 times per second. The switch is so fast that we don’t see any changes in the arc; however, we can certainly hear a difference as compared to straight constant voltage (CV) output. The primary effect of pulse is a reduction of heat input. However, there is minimal or in some cases no loss of depth of penetration. This is a huge advantage when welding with the GMAW process out of position. The lower heat input allows for the puddle to freeze faster and allows for higher deposition rates and better bead appearance out of position than with traditional short circuit transfer. For more on pulse, its benefits and limitations read Can Pulse Really Solve All Your Welding Problems.
Pulse waveforms are not created equal. Their details and the quality of the weld they produce vary by brand of equipment. Even within the same brand there can be multiple waveforms to accommodate different applications. For instance, there are pulse waveforms to weld root on pipe, pulse waveforms to weld very thin stainless base metal, pulse waveforms to weld thin materials at really high travel speeds (achieving good wetting at high speeds with a low heat input process can be extremely challenging). There are also pulse waveforms that affect bead appearance such as that commonly known as pulse-on-pulse or double-pulse. This waveform is typically used in aluminum to achieve a bead appearance that resembles a GTAW (tig) weld.
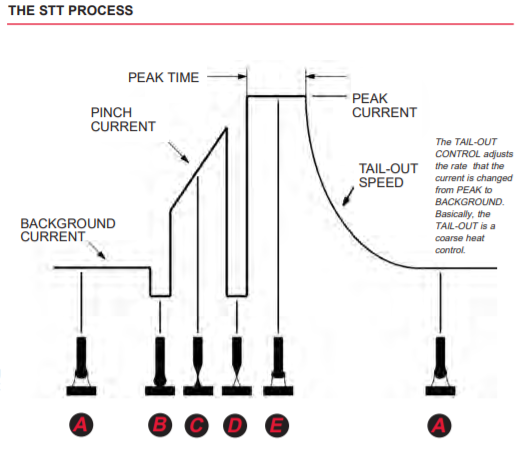
STT is a patented waveform that was specifically developed to weld root on pipe. It also excels in thin materials and spatter reduction. The graph above shows how the current level is controlled by the power source in order to minimize the spatter associated with the short circuit mode of metal transfer.
The vast majority of waveforms do not produce a pulse output. Instead, they are finely tuned outputs that are dependent on the following four variables:
- Base metal and filler metal alloy
- Diameter of filler metal (wire diameter)
- Shielding gas being used
- Desired metal transfer (CV, pulse, short circuit)
The user/welder will select a waveform based on these variables. The power source will then access the right waveform from its library and provide a welding output that is optimized for the four variables mentioned above. The benefits include:
- smoother arc
- higher operating range for the electrode
- reduction in spatter
- better arc starts
- lower heat input (some waveforms)
- deeper or shallower penetration depending on what’s desired
- improved toe wetting
- faster travel speeds while still maintaining desired bead shape and penetration depth
- higher deposition rates out of position
Waveform control technology will continue to evolve. This will continue to improve quality and reduce rework. It will never be able to fully compensate for the lack of skill from a welder, but can certainly help. Even with these advancements the need for highly skilled welders will continue to increase. Waveforms can only help so much.
Please note: I reserve the right to delete comments that are offensive or off-topic.