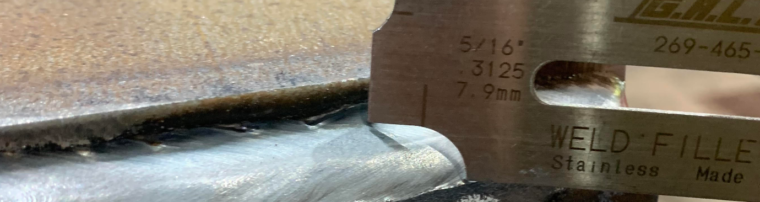
If you are a CWI, welding engineer or serve in a capacity that requires you to use and interpret welding codes, you probably have run into instances where the code is not very clear. Many of the questions we receive from our readers deal with interpreting codes and standards. Many times it is not about interpreting the code, but wondering what to do when the code does not address that situation.
Over the next few weeks we will discuss some of these situations. We’ll provide very specific examples of what to do when the code does not provide the information necessary to make a decision. For example, the Design Clause of AWS D1.1 states that for lap joints where the metal thickness is ¼-inch or greater there is a maximum fillet weld size equal to t – 1/16-inch, where t is the thickness of the base metal, as shown below.
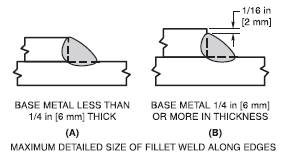
Figure 4.7 of AWS D1.1/D1.1M:2020 Structural Welding Code – Steel (Maximum Fillet Weld Size Along Edges on Lap Joints).
If a production weld does not adhere to these requirements what is our responsibility as an inspector? What is our responsibility as the fabricator? Do you have to remove the weld and reweld? Is that really necessary? What is the purpose of this requirement?
The primary reason for this requirement is to be able to verify the weld size, more specifically to ensure that the throat dimension is sufficient. More detail will be provided next week.
For now let’s look at the general guidelines regarding what to do if the code isn’t clear or does not provide enough information to make a decision.
When the code isn’t clear do the following (these are not in any particular order)
- Ask others for assistance – more experienced welding professionals may have already dealt with the issue at hand and can provide guidance. If you happen to know a few of these professionals call them directly.
- Read the Commentary – it continues to amaze us how many CWIs and Welding Engineers don’t know there is a commentary section in most of the welding codes. This section is there to provide some color on certain sections of the code. It allows the AWS committees to explain the reason behind certain requirements.
- Consult the Engineer in charge – the engineer in charge as defined by the American Welding Society is the “duly designated individual who acts for and on behalf of the owner on all matters within the scope of the code.” This person can make judgment calls when there is ambiguity.
- Use sound engineering judgment – If you are the engineer in charge and still have doubts as to what to do then go back to basics. Use sound engineering judgment. The code exists to ensure the safety of those using and those around welded structures. Always err on the side of caution. This may not always be the lowest cost alternative, but don’t take changes when safety is at stake.
- Consult the committee in charge of writing the code – Did you know that you have the option to send your inquiries to the committee in charge of specific codes and standards? If you’ll do this make sure you follow the guidelines detailed in the code you are using. For example, if you are using AWS D1.1 then turn to Annex T (in the 2020 edition) which provides the guidelines for the preparation of technical inquiries for the Structural Welding Committee.
Another option which we don’t list above is to consult online forums. This can be dangerous as there are more people providing incorrect information than there are providing correct information. If you will consult forums make sure that it is one that is hosted and monitored by a credible resource. Always inquire further, never trust those comments 100%.
If you have any other things we can do when the code isn’t clear please let us know! We’ll be happy to share in later articles.
We fabricating structural steel ( angles, channels, I beams, girders of SAF 2205 material and we experience tremendous distortion because AWS D1,6 state the fillet weld size must be the same size of the thinned thickness of the component to be welded. Example I making an I beam with a web thickness of 8mm and the flanges of 10/ 12mm thickness, welding process if FCAW qualified procedure, position 1F. The distortion on the flange created by the 8mm fillet weld is out of the accepted criteria! We improve by pitting square stiffeners inside and strong back on the outside and back stepping techniques! ALL THIS RESUTS IN: A LOT OF STOP/STARTS, EXCESSIVE GRINDING ON REMOVING THE STIFFENER AND A LOT OF REWORK HOURS. Can someone explain the necessity for this rule on the welding size required.???? Thank you
Happy to help you look into this. Can you please let us know exactly where in AWS D1.6 this requirement is specified? The requirements for minimum fillet weld sizes is more important for AWS D1.1 (Steel) since low heat input can cause embrittlement. In some stainless, primarily austenitic stainless steels a fast cooling rate is preferable so a low heat input (small weld) is desirable.