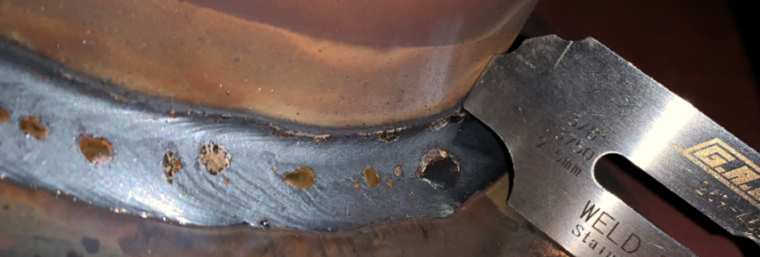
When bidding jobs several fabricators end up calculating their costs associated with welding and then double that number to be safe. In some cases, that isn’t even enough. It is important to have a clear understating of how to translate the amount of welding to be done to actual manufacturing costs. One of the biggest challenges is that rework and overwelding is hard to estimate. This is because many fabricators have no way to control or measure their welding operations.
The list provided below can be extremely helpful for companies that are new to quoting jobs, but it should not be disregarded by those with plenty of experience. It is by no means a comprehensive list. It is also very specific to welding and does not go into other processes.
When a potential customer provides a print with all the welds called out you should be able to determine exactly how much weld metal is needed. You then should be able to estimate the amount of labor associated with making those welds.
Below are some of the most common oversights by fabricators when estimating welding costs.
- Overwelding – If you are to make 100 feet of 3/16-inch fillet welds that would require 6 pounds of weld metal. If the weld size is not controlled and typical welds made in the shop are ¼-inch that would mean an increase of about 78% in filler metal required. So instead of 6 pounds you will need 10.65 pounds of weld metal. Even if your welders maintain a 3/16” fillet weld size there is usually 10 -15% more metal required due to the convexity of the weld (crown) whether it is intentional or not. It is possible to get a flat weld face, but should not be assumed. For more on this read: The Outrageous Cost of Overwelding.
- Failure to consider process efficiency – Different welding processes have different electrode efficiencies. GMAW (mig) can be as high as 98% efficient. This means that for every 100 pounds of electrode to you consume, 98 pounds will become weld metal. This 2% difference can add up, but it is not necessarily significant. However, if you fail to consider this with a process like FCAW (flux-cored are welding) you may be in trouble. Typical efficiency for FCAW electrodes ranges from 83 – 88% depending on the diameter of the wire. If you forget to account for this, your filler metal usage can be off by as much as 17%.If you were using SMAW (stick) your efficiency is around 65%.So for every 100 pounds of filler metal purchased you can only deposit 65 pounds of weld metal. Always keep electrode efficiency in mind. For additional information read: Which Arc Welding Process is the Most Efficient.
- Failure to consider part fit up – Gaps add a lot of volume to the amount of filler metal required. you are to make a ¼-inch fillet weld but have a 1/8-inch gap, you are required to increase the size of the leg by the size of the gap if you are to maintain the same amount of weld strength (dictated by the throat of the weld).So you would go from a ¼-inch fillet weld to a 3/8-inch fillet weld. This results in an increase of 125% in filler metal required. That is more than double what your projections would have been if you failed to considered gaps (provided you have fit up issues). To look further into this cost driver read: The Outrageous Cost of Poor Fit Up in Welding Operations.
- Failure to consider rework – Do you know what your welding rework rate is? Is it less than 1%? Is it more like 5% to 10%?Rework represents a huge cost. If you don’t have a way to measure this you will be going blind into estimating costs. We should always strive for zero rework, but that is hardly ever the case.
- Failure to consider documentation requirements – Many contract documents specify the need to comply with a specific code or standard. This typically means you will need to develop and qualify your welding procedure specifications according to the tests set forth in the applicable code or standard. Even when this allows for the use of prequalified welding procedures there can be significant costs involved. Additionally, your welders will probably also need to be qualified.
Many other factors go into estimating the cost of a welding job, some of which are unpredictable and for which allowances must be made. Do not oversee the five factors above as these should be relatively easy to control and/or estimate.
References:
Qualification of Welding Procedures, Welders and Welding Operators per AWS D1.1 (2017)
“Qualifying Welding Procedures, Welders and Welding Operators” is a guide developed to help you perform your own qualifications in full compliance to AWS D1.1 Structural Welding Code.
Welding Procedure Development for Non-Welding Engineers
Not being a welding engineer is not an excuse for avoiding due diligence. The principles needed to properly develop a welding procedure are clearly explained in this publication. The intent is to provide the knowledge necessary to make the right selection of the many welding variables. It has been written in order for anyone, regardless of level of education, to read and apply it. Welding Procedure Development for Non-Welding Engineers can also be used a troubleshooting guide, as it clearly explains the effects of all welding variables.