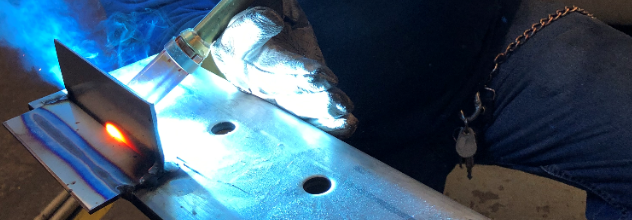
If you own or work at a job shop you may have noticed an increase in the number of customers that require the use of qualified welding procedures to build their products. Some fabricators are even getting this request from long time customers who never required them in the past. So why is this?
The purpose of having a welding procedure specification (WPS) is to give the welder detailed instructions on how to make a weld. These instructions consist of parameters that need to be used such as amperage, voltage, travel speed, transverse and travel angles, gas flow rate, etc. The WPS also provides joint details such as allowable gaps, groove angles, material thickness and root dimensions. Other instructions provided by the WPS include required preheat and interpass temperatures, interpass cleaning instructions and whether or not post weld heat treatment is required. As you can see, a properly developed WPS should produce sound welds, so long as it is followed.
Over the past 10 – 15 years we have seen a steady decline in the number of skilled workers. This is especially true in welding. Today, in the US alone there are over 350,000 vacancies for skilled welders. With reduced skill comes increased costs. These costs come from rework, warranty repairs, and in many cases the need to overbuild products to prevent failures.
Although the costs associated with poorly built products rest on the fabricator, the end user suffers from these failures as well. For example, a few years ago a manufacturer of concrete mixer trucks had a weld failure in a shaft. This shaf allows the barrell to spin which keeps the concrete from solidifying. When the shaft failed the barrell stopped spinning and the load of concrete hardened. The end user who purchased the concrete mixer was not able to pour a pad of concrete. Their customer was not able to install a large piece of equipment. So not just one but two end users were affected by this failure. The manufacturer of the concrete mixer incurred significant costs and had a very upset customer.
The lack of skill is forcing end users to demand the use of WPSs in order to assure quality. They may not understand welding, they may not understand how welding procedure qualification and welder qualification works, but they know that having qualifications is better than not having them. Similar to needing a house wired, would you want any electrician doing the work or would you feel more comfortable with a licensed electrician?
Unfortunately, if a WPS is not developed properly it doesn’t do much good. Many fabricators that are required to have WPSs see it merely as a paperwork requirement. The WPSs may have been done properly, but after being submitted for an audit they are stored away and not supplied to the welders.
In other cases, fabricators recognize this as an opportunity to increase quality, increase productivity and reduce costs. However, the lack of understanding of how the many welding variables affect quality and productivity prevent this from happening. This is one of the reasons why we wrote Welding Procedure Development for Non-Welding Engineers. The principles outlined in this ebook are the exact same ones used by welding engineers to develop welding procedures that achieve the needed quality and maximize productivity. You don’t’ need a welding engineering degree and you do not need to be CWI to develop welding procedures. If you have a basic understanding of welding processes and the effects of welding variables and if you can follow structural welding codes you can perform your own qualifications. Even if you end up hiring this out, having this knowledge is a must for any manufacturing facility in which welding is the primary industrial process.

From the exterior both welds look acceptable. Both welds were made with .035” ER70S-6 wire and 90% argon / 10% carbon dioxide gas. Weld (A) was made at 350 in/min using a weave technique while weld (B) was made at 550 in/min using a stringer technique (no manipulation). The improved welding procedure (B) increased quality and increased welding speed by 57%.
Being asked to have qualified welding procedures and qualified welders should not be seen as costly requirements. Take it as an opportunity to improve your processes. Remember, a properly developed welding procedure will assure quality and maximize productivity. If you pay a third party to do this for you, make sure that they are not just meeting the quality requirements imposed by the governing welding code, but also maximizing productivity.
References:
Welding Procedure Development for Non-Welding Engineers
Qualification of Welding Procedures, Welders and Welding Operators
Welding procedures are also required on our robot welders. If an outside service person works on our robots, they are required to make sure the robot is following the procedure.
With our resistance welders (butt welders), the welding parameters are not set in stone but the parts must pass a strength test where not the weld but the parent material must break.
We are ISO 9001 registered
You are correct. Often times it is assumed that robots don’t need welding procedures. As you stated, an inspector has to be able to compare what is being done by the robot with what was qualified. A WPS is required regardless of the level of automation. Additionally, the operator must also be qualified.