This question can be answered very quickly. Gas Metal Arc Welding (GMAW) and Submerged Arc Welding (SAW) can have 98-99% deposition efficiency. However, the question is a bit more complicated since when we talk about efficiency we don’t just care about deposition efficiency (how much of the electrode becomes weld metal). What we care about is how quickly we can apply the weld metal.
Because of this, the answer to this question is “it depends.” It depends on the application and its requirements.
First, let’s look strictly at deposition efficiency of different types of electrodes:
SMAW (stick) – 60 – 65%
FCAW-G (flux-cored gas shielded) – 82 – 88%
FCAW-SS (flux-cored self-shielded) – 75 – 85%
GMAW (mig) – 92 – 99%
SAW (submerged arc) – 99% (does not include flux)
MCAW (metal-core) – 94-98%
GTAW (tig) – 94-97%
At first glance you may assume that SMAW is the worst in terms of efficiency. This is true of its depositions efficiency. For every pound of stick electrode that you buy only about two thirds of it become weld metal,. The rest is stub loss and slag. On top of that SMAW is a true manual process, meaning there is no automatic feeding of the electrode. This makes SMAW a very inefficient process. However, there are cases where the ability to change electrode types and diameters quickly can increase efficiency. SMAW is typically most efficient in maintenance and in some outdoor applications where it becomes difficult to haul around cylinders of gas and/or portable wire feeders.
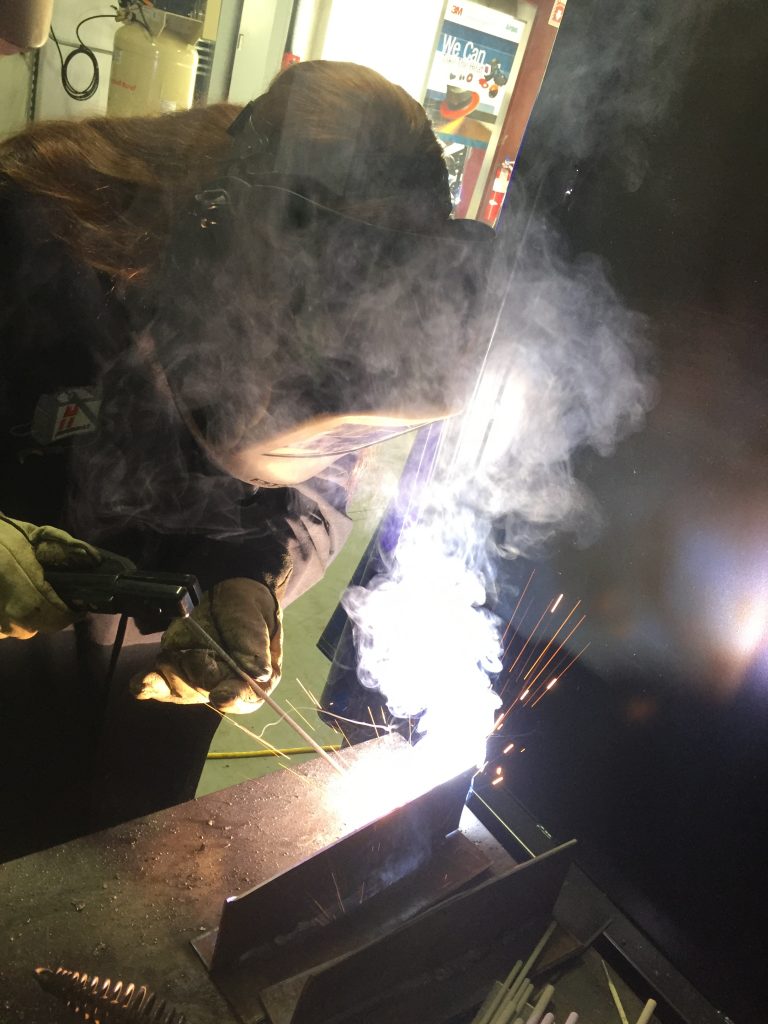
Shielding metal arc welding has very low electrode efficiency but it is a very versatile process which comes in handy when flexibility is required.
GMAW and MCAW appear to be the best and they are as long as we are welding in the flat or horizontal positions for fillet welds or flat positions for grooves. With deposition rates exceeding 15 pounds per hour with 1/16” diameter wire this process is extremely efficient. However, if you take it out of position and weld vertical up or overhead you are forced to reduce that deposition rate to something closer to 5 pounds per hour.
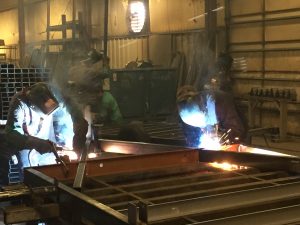
Gas metal arc welding is the most popular arc welding process in manufacturing facilities. It’s high electrode efficiency and ability to deposit metal at a high rate make it a very attractive process for high productivity environments.
FCAW can help out of position. If you then switch to FCAW when your work requires you to go vertical up or overhead you can get close to 10 pounds per hour deposition rate with the right electrode. There are FCAW wires that are specifically designed to run out of position. Although the efficiency of the this type of electrode can be as as low as 75% for self-shielded FCAW it can be the most efficient when welding out of position. Cleaning the slag, especially when we doing multiple passes can be very time consuming. However, the process can double deposition rate of GMAW out of position, it is easier to run for the welder and may reduce expensive rework.
SAW has the highest electrode efficiency and in long, flat, straight joints it will be the most efficient. It is also extremely beneficial in circumferential groove welds as those done in pressure vessels. SAW is also the prefered process for hardfacing of mill rolls and other type of continuous welding when applying hardfacing. However, with SAW you are limited to flat and horizontal positions.
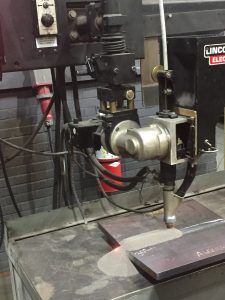
Submerged arc welding is capable of depositing welding metal at over 20 pounds per hours with a single electrode. However, it is limited to the flat and horizontal positions only.
GTAW is very efficient but as you probably already know it can be excruciatingly slow.
Always keep in mind that the most economical process is that which has the lowest cost per foot of welded joint. So the efficiency of the electrode is only one component. Other factors that affect the cost per foot of weld are:
- Cost of electrode
- Cost of labor/time to weld including slag removal (if any)
- Rework (some processes are more susceptible to weld discontinuities and defects)
- Joint preparation required (i.e. GTAW requires perfectly clean joints where SMAW does not)
- Welder skill
What process do you use the most? Do you believe it is the most efficient for your particular application?
Reference: The Procedure Handbook of Arc Welding – 14th Edition