The modes of metal transfer refer to the different ways in which the filler metal (electrode) is transferred through the welding arc and into the weld puddle. We can write a book on this topic but we’ll keep it simple to provide an understanding of the different modes of transfer, what they require and what their advantages and limitations are.
The variables that determine the mode of metal transfer include: wire diameter, amperage, voltage and shielding gas composition.
The basic modes of metal transfer are:
There are variations which create sub-categories within these four, but no need to complicate things over a mostly theoretical differentiation.
This article will focus on short circuit transfer and we’ll cover the other three modes in later posts.
Short Circuit Transfer
Short circuit, commonly called “short arc” and formally called GMAW-S, is a mode of metal transfer with low heat input where the transfer of metal from the electrode to weld puddle occurs by a series of electrical shorts. As the welding wire is fed it makes physical contact with the base material and creates a short. As the short occurs the voltage immediately drops to zero. However, mig welding machines are constant voltage power sources and their main job is to keep the voltage constant. In order to do so in the presence of short, which wants to drive the voltage to zero, the power source will increase the amperage to break the short.
The short is essentially blasted away by the spike in amperage causing an explosion of sorts. This explosion generates spatter and the crackling noise we hear. Some people liken the sound of short circuit transfer to that of frying bacon. Every time the wire shorts to the base metal the welding arc is extinguished. The welding machine will react instantaneously with the spike in amperage to eliminate the short and reignite the arc. This happens many times per second (up to 200 times per second!) which is why we never see the arc go out.
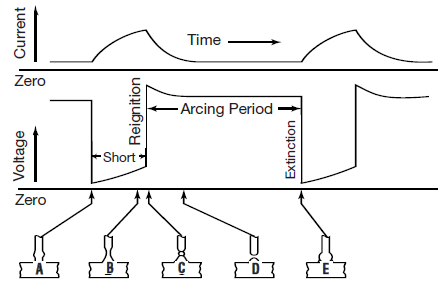
This plot of amperage and voltage in relation to time show how the short brings the voltage to zero and at the same time the power sources increases amperage to break the short.
Short circuit transfer generates low heat input due to the low amperage and low voltage used. Because of this, it is limited to thin materials. The American Welding Society prohibits the use of short circuit transfer in prequalified welding procedures because of the high probability of lack of fusion.
Typical shielding gases for short circuit transfer include 100% carbon dioxide and mixes containing up to 75% argon with the balance being carbon dioxide.
Advantages of Short Circuit Transfer
- Good for thinner materials (1/8” and under) – low heat input prevents blowing through the base material and as long as the travel speed is adequate can also prevent distortion.
- All-position welding – due to the low heat input the puddle solidifies quickly which allows for welding in all positions.
- Great for gaps and bad fit up – short circuit transfer is good for bad fit-up, including gaps. Short circuit is widely used to run the root pass on pipe because of this reason.
- Low cost – The low amperage requirement of short circuit transfer means that basic, low-end power sources can be used. Carbon dioxide is also relatively inexpensive compared to mixes with high argon content.
Limitation of Short Circuit Transfer
- Limited to sheet metal – as mentioned above, the low heat input produces lack of fusion on thicker sections.
- Spatter – the shorting of the arc and subsequent blasting of the arc by the spike in amperage generates spatter which increases clean up time and reduces the electrode efficiency.
- Not allowed for use in prequalified welding procedures (due to susceptibility to lack of fusion).
The biggest problem with short circuit transfer is that we can make a very nice looking weld that gives the illusion of quality. Single and multi-pass short circuit transfer welds are made every day on trailer frames, steel buildings and other load-bearing structures. This is why having qualified welding procedures is crucial. Following codes such as AWS D1.1 Structural Welding Code (Steel) should not be seen as a nuisance but rather as an opportunity to increase quality by following proven guidelines.
To illustrate what using short circuit transfer in structural members can mean take a look at the images below. The first weld (left) was made using short circuit transfer. The weld on the right was made with spray transfer.
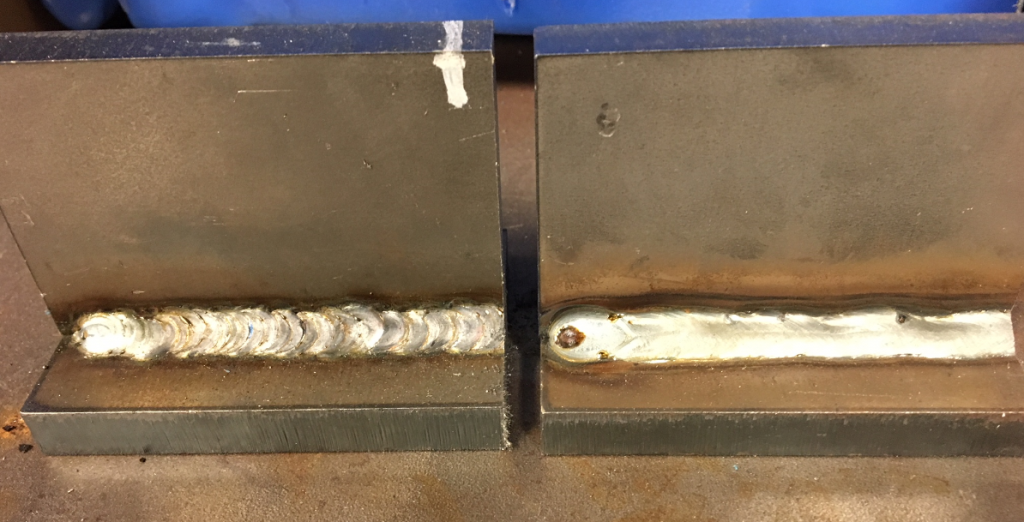
The weld on the left was made using short circuit and by manipulating the electrode motion distinct ripples are formed. The weld on the right was a stringer (no manipulation) made with spray transfer. Both welds were made on 3/8-in plate.
Looking at the exterior of these welds we can assume that both are good welds. Some people prefer the weld on the left because they like the look of the ripples. But what is underneath these welds? Let’s take a look.

The etched cross section of the short circuit weld (left) shows clear of lack of fusion. The image on the right show the deep penetration associated with spray transfer.
Although both welds are the same size, the weld on the right (spray transfer) has almost twice the load bearing capacity due to its deep root penetration. The short circuit transfer weld on the left shows significant lack of fusion. These welds were made on 3/8-in material to show that short-circuit transfer should not be used on thick sections. For more on this topic read How To Determine the Shear Strength of a Fillet Weld.
Is it time for you to consider the quality of your welds?
Reference: The Procedure Handbook for Arc Welding, 14th Edition
Great article (as always). Glad to see you guys back.
I have a lingering doubt: How do you know what kind of mode you’re using? I mean, is there a range in parameters that you can change in the machine to make sure you´re in globular mode or any other mode? Is it a switch on the machine? Are machines restricted to a certain mode type (eg.: “this machine only welds in short circuit”)?
Other question: What is the best transfering mode to weld in a vertical position?
Thanks!
Great questions.
The mode of transfer depends on the current and the shielding gas. If you have at least 78-80% argon you can spray transfer once you get above the transition current. If you are welding with less than 78% argon you’ll never achieve spray transfer. So you would be in short circuit and then move onto globular once the current is high enough. The best mode for vertical up welding is short circuit as globular produces way to much spatter and an erratic arc and spray transfer is to fluid to weld out of position. If you are able to do pulse then you have the best of both worlds. Higher depositions rates and less than spatter than short circuit and still able to weld out of positions.
I have been tiring to qualify a short circuit procedure but have failed twice. I am using 20.5 volts, 75 – 25 gas, backing plate on 3/8 thick SA36 V 45 degrees groove coupon flat, 0.35 ER70S-6 wire. the root bends look excellent but face bends crack. Its short circuit all the way to the cap. Can I use short circuit for the root and finish with spray and qualify for both short and spray?
Hi Victor, absolutely. It is highly recommended that you use spray transfer for fill and cap passes if you are welding in position. And, if you are using a backing plate then use spray for the root as well. However, keep in mind that if you qualify a welding procedure with spray you are NOT qualified to weld short arc.
This is a great article– especially the last photo. Can you list the following for the two different welds:
Shielding gas composition
WFS
Voltage
This would be helpful for readers to see what needs to be done to avoid LOF defects.
Thanks!
Both welds were made with .035” ER70S-6 wire and 90% argon / 10% carbon dioxide gas. Weld (Short Circuit) was made at 300 in/min using a weave technique while weld (Spray) was made at 550 in/min using a stringer technique (no manipulation).
Good Stuff
Thank you
Thanks for your comment Dennis. I’m glad you found this helpful.