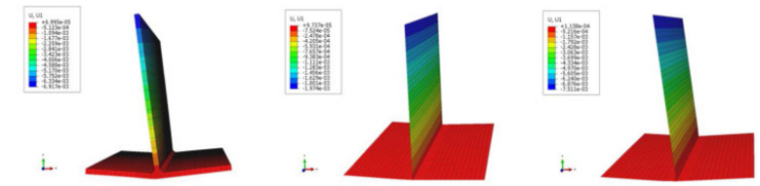
Bigger is not always better, at least not in welding. Making welds bigger than they need to be is not only wasteful and costly, but can cause other problems such as distortion and premature failure.
Below are 3 reasons why you may need to pay close attention to your weld sizes.
1. Bigger welds cost more – any time we make a weld bigger than it needs to be we are increasing our costs. This can get out of hand at times, especially with fillet welds. If a print calls for a 3/16” fillet weld and you make a 5/16” fillet weld you are almost tripling your filler metal consumption. The filler metal is the least of your concerns, because you are almost tripling the amount of filler metal this means you are welding almost three times slower than you could be. For more on this read The Outrageous Cost of Overwelding.
2. Bigger welds cause distortion – the biggest contributing factor causing distortion is the size of the weld. The bigger the weld, the stronger the shrinkage forces. Formulas that estimate the amount of distortion make this quite clear. For more on this topic read 7 Ways to Control Distortion.
3. Bigger welds may negatively affect mechanical properties – bigger welds usually mean higher heat input. A high heat input is not always bad. It may actually be beneficial to reduce susceptibility to hydrogen induced cracking in carbon steels. However, it can also be detrimental. Higher heat input produced by larger welds may increase ductility but reduce strength in carbon steel weldments. In austenitic stainless steels, like 304L, bigger welds that produce high heat inputs can make the heat affected zone susceptible to sensitization. For more you can read The Relationship Between Heat Input and Weld Size.
Overwelding is a big problem, yet many fabricators associate large welds with higher quality and do not realize this is not always true. Nor do they understand the significant increase in cost. There are more drawbacks to ovewelding. Can you name at least one more?
References:
Welding Procedure Development for Non-Welding Engineers
Prequalified Welding Procedures for Steel Fabricators
Do you need AWS D1.1 welding procedures that have been qualified or prequalified in accordance with the code? If so, this publication has you covered.
322 Prequalified Welding Procedure Specification for Steel Fabricators
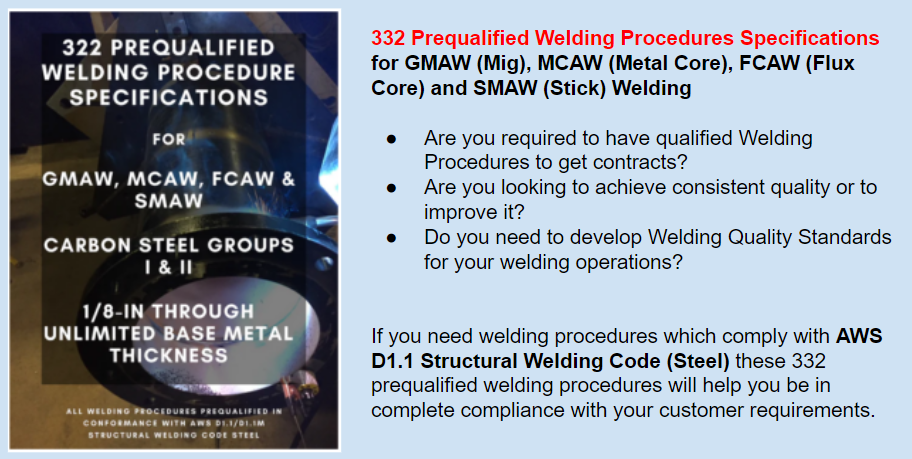
Please note: I reserve the right to delete comments that are offensive or off-topic.