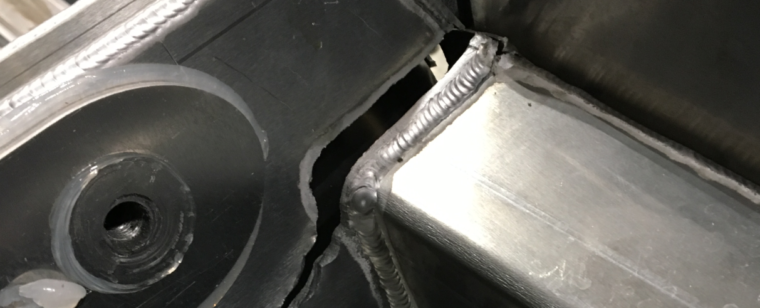
Welding aluminum should not be complicated. That is, if you are welding 6061-T6 (very common) with ER5356 or ER4043 filler metal. Although this alloy is still susceptible to cracking, other aluminum alloys are much more prone to cracking. Below are 6 factors that affect cracking susceptibility when welding aluminum alloys.
- Thermal stresses: Aluminum has a relatively high coefficient of thermal expansion, meaning it expands and contracts more than other metals when heated and cooled. When we weld, the rapid heating and subsequent cooling can create thermal stresses, leading to cracking.
- High thermal conductivity: Aluminum has excellent thermal conductivity, which results in fast heat dissipation. When welding aluminum, the heat can quickly transfer away from the weld zone, potentially causing lack of fusion. Although lack of fusion is not a crack, it can lead to cracking by reducing the effective throat of the weld, thus reducing it’s load carrying capacity.
- Alloy selection: Different aluminum alloys have varying compositions and properties. Some alloys are more prone to cracking than others. For example, certain high-strength aluminum alloys, such as those used in aerospace applications, are particularly susceptible to cracking during welding. It is crucial that you select the right filler metal. If you are unsure, consult your welding engineer or seek sound advice.
- Joint design and fit-up: The design and fit-up of the joint can influence cracking. If the fit-up is poor or the joint design is inadequate, it can create stress concentrations that promote cracking.
- Improper welding technique: Welding aluminum requires specific techniques and parameters to achieve a sound weld. In the gas metal arc welding (GMAW) cracking can occur when welders try to achieve the “stacked dimes” look (ripples) by manipulating the arc. This typically will result in intermittent lack of fusion. This in turn reduces the effective throat and the strength of the weld.
- Contamination: Aluminum is sensitive to contamination from oils, grease, dirt, or other foreign materials. If the welding surface is not properly cleaned and prepared, contaminants can be trapped in the weld, leading to cracking. Ensuring the filler metal is clean, dry and free of all contaminants is crucial.
To minimize the risk of cracking when welding aluminum, it is essential to use appropriate welding techniques, select the correct alloy and filler material, ensure proper joint fit-up, and clean the surfaces thoroughly.
Please note: I reserve the right to delete comments that are offensive or off-topic.