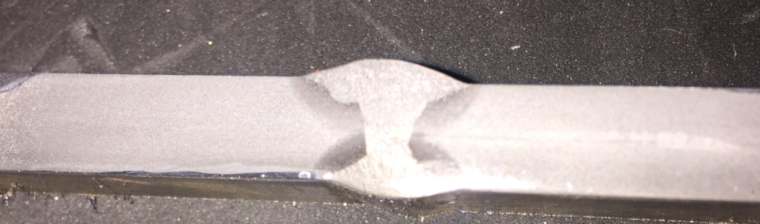
A qualified welding procedure is a welding procedure that has been proven to produce sound welds after undergoing extensive testing. When using structural welding codes, these tests include both destructive and nondestructive tests. Some of these tests are:
- Visual examination
- Macroetch
- Break test
- Bend test
- Ultrasonic inspection
- Radiographic inspection
- Hardness test
- Tensile test
The reason for conducting these tests is to verify that the welding procedure can produce the necessary mechanical characteristics in the deposited weld metal and adjacent heat affected zone to be fit for service.
Each of the tests above provide assurance that the welding procedure will in fact have the ability to produce sound welds. Of course, in manual and semi-automatic applications the skill of the welder comes into play. This is why a good quality control system will also have welder performance qualification tests.
Here is, in plain English, what each of the above tests looks for and how it provides us the assurance that the welding procedure is adequate.
- Visual Examination – if you have been following us for a while you should know that just because a weld looks good on the outside it does not mean the weld is good. However, visual inspection can definitely tell us if there are issues with the weld. Visual inspection looks for welding discontinuities in the weld surface such as: undercut, overlap, cracks, porosity and others. Some of these discontinuities constitute an immediate failure of the procedure, others have an allowance based on structural codes. For example, cracks are not allowed regardless of dimension, while some discontinuities like undercut are allowed up to certain measurements (depth and length).
- Macroetch – typically only done on fillet weld tests, a macroetch provides us with assurance that the welding procedure can achieve fusion to the root of the joint and to the side walls. Fusion to the root is important because if this is not achieved the weld would not have the strength or load carrying capacity required.
- Break test – a macroetch can only provide information on a single point of the weld. The break test is done to ensure fusion to the root over a certain length, typically 4 to 6 inches. Its only purpose is to ensure that fusion to the root of the weld has been achieved.
- Bend Test – this type of test is making sure that the weld does not have any internal discontinuities such as cracks and lack of fusion that could create failures. It also ensures that the deposited weld metal and the heat affected zone have enough ductility. A weld that is too hard and not very ductile is sometimes desired. However, this is hardly the case.
- Ultrasonic Inspection – this is a type of volumetric test, meaning it examines the entire volume of the weld. It can detect lack fusion, slag inclusions, lack of penetration and other discontinuities that can create failures.
- Radiographic Inspection – Similar to ultrasonic, radiographic inspection is volumetric. It can detect lack of fusion, porosity, some cracks among other discontinuities.
- Hardness Test – in some cases we want high hardness, such as when we are depositing hardfacing material, other times, excessive hardness can facilitate cracking and other types of failure. Depending on the intended service of the weld, hardness needs to be above or below certain values. Hardness and ductility are inversely related. For more on this you can read Weld Toughness vs Weld Strength.
- Tensile Test – Tensile tests are for determining the load carrying capacity of a weld. The higher the tensile strength the more load it can carry or sustain before failure
Welding codes like AWS D1.1 allow the use of prequalified welding procedures. These are welding procedures that do not require testing in order to be considered qualified. That is because they need to follow a long list of requirements and limitations that assure they are adequate. This can sometimes save a lot of time and money; however, most prequalified welding procedures are for use with “standard” steels. Once you get into really high strength steels there is no prequalification. You must qualify by testing.
Reference: Qualification of Welding Procedures, Welders and Welding Operators
Please note: I reserve the right to delete comments that are offensive or off-topic.