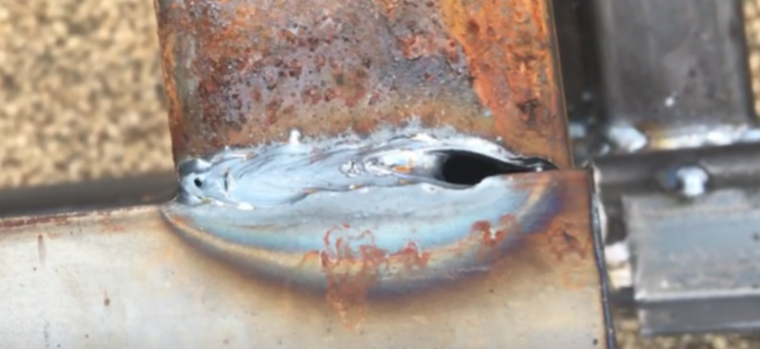
Burn-through is a common defect in welding of light gauge materials. It is typically results in costly scrapping of parts since it can be difficult to fix. Or, if left in place when there are not structural integrity concerns it looks awful and portrays extremely poor quality.
The following is an excerpt from our guide: Weld Troubleshooting for Non-Welding Engineers.
Burn-through is a condition created by excessive penetration that leads to the weld metal being expelled on the backside of the joint. The result is an opening in the joint rather than a weld. This problem is common in welding thin gage materials as well as in open root joints such as those seen in pipe welding.
Burn-through must not be confused with melt-through. Melt-through is the term used for a condition where some weld metal protrudes on the back side of the joint; however, the weld itself is acceptable (there are no holes on the weld or joint). Melt-through is called for in welding symbols and the purpose is to assure that there is adequate penetration. The melt-through confirms the penetration.
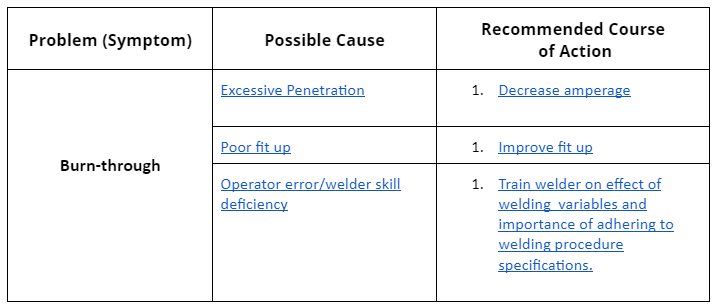
Burn-through possible causes and solutions
Cause: Excessive penetration
Although penetration is usually a good thing, it is not if it is excessive and creates burn-through. Amperage is the essential variable that controls penetration. Thin materials are especially susceptible to burn-through so the welding procedure must control the amperage based on the material thickness.
Solution 1: Decrease amperage
Amperage drives penetration. The higher the amperage the deeper you can penetrate and vice versa. In order to decrease susceptibility to burn-through, reduce the amperage.
Keep in mind that changes to one variable may require adjustments to others. If you decrease amperage you may need to decrease your voltage to maintain the same arc characteristics.
Also, decreasing amperage results in decreased melt-off rate (how quickly the electrode is consumed) and thus a lower deposition rate (the rate at which we deposit weld metal). This means that as you decrease the amperage your weld will get smaller if nothing else changes. This may be acceptable if you are getting burn-through. However, if you are needing to meet a specific weld size you may need to slow down the travel speed.
Cause: Poor fit up
Poor fit up can easily lead to burn-through even on thicker sections. Controlling fit up allows the welder to more easily control the amount of penetration. Having gaps can be a problem. An even bigger problem is when the gap is not consistent. For example, if a gap on 16 gage material varies from 1/32-inch to 1/8–inch, it will make it really hard for the welder to deposit a weld without burn-through. To reduce susceptibility to burn-through improve fit up. This may require an investment in upstream operations, such as bending or cutting operations to make sure that parts fit properly.
Figure 3.9-1 – Inconsistent fit up can lead to burn-through, especially when gaps get too big for the weld parameters being run by the welder.
Solution 1: Improve fit up
Improving fit up is critical, not just to prevent burn through, but to control costs and quality. To improve fit up parts need to be formed, bent and cut well. This sometimes means slowing down upstream operations to assure quality. Other times it means obtaining better cutting equipment or simply training the operator. At times, improving fit up may increase costs, but overall costs tend to be decreased due to reduced rework and more efficient welding operations.
If cutting, forming or bending operations are outsourced, it may be necessary to speak to your supplier and be more strict with your acceptance criteria. If parts are not delivered to you meeting specifications you may need to find a different supplier.
Cause: Operator error/welder skill deficiency
In manual and semi-automatic operations we can control every single variable, except for welder skill. That is specific to each welder. Even the best welding procedure can produce discontinuities such as incomplete penetration if the welder makes a mistake. Some mistakes, such as traveling too fast or too slow, excessive CTTWD and failure to properly prepare (clean) the weld joint have already been explained above. Other issues such as excessive weaving and incorrect angles can also come into play.
Solution: Train the welder
An effective welder training program is essential to help welders understand welding theory, more specifically, they should understand the effects of essential welding variables and the importance of adhering to a welding procedure specification (WPS).
Below is a list of some common mistakes and work practices that may lead to burn-through:
- Incorrect technique adjustment – unfortunately, gap inconsistencies introduce many problems to the welding process. The welder must compensate for these inconsistencies with workarounds. An example of these workarounds is increasing the contact-tip-to-work-distance (CTTWD) when the gap opens up. This action reduces the amperage without having to stop and reset the welding power source. A similar action is done in SMAW (stick welding). By increasing the standoff distance, commonly referred to as “pulling a long arc,” the welder reduces the amperage to some extent. If a welder does not do this, burn-through might occur. Increasing the CTTWD in GMAW, MCAW and FCAW can introduce other problems such as porosity, so the welder has to be careful not to excessively increase contact-tip-to-work-distance.
- Too slow welding travel speed – on thinner materials, traveling too slow will increase the changes on burning through. Welding faster decreases heat input and provides a better chance to attain a weld without discontinuities in thinner materials.
There may be other cause for burnthrough, it isimportant to follow a sound troubleshooting process in order to adequately determine the root cause. Is burn-through something you see in your welding operations? What have been the challenges in avoiding this welding problem?
Source: Weld Troubleshooting for Non-Welding Engineers
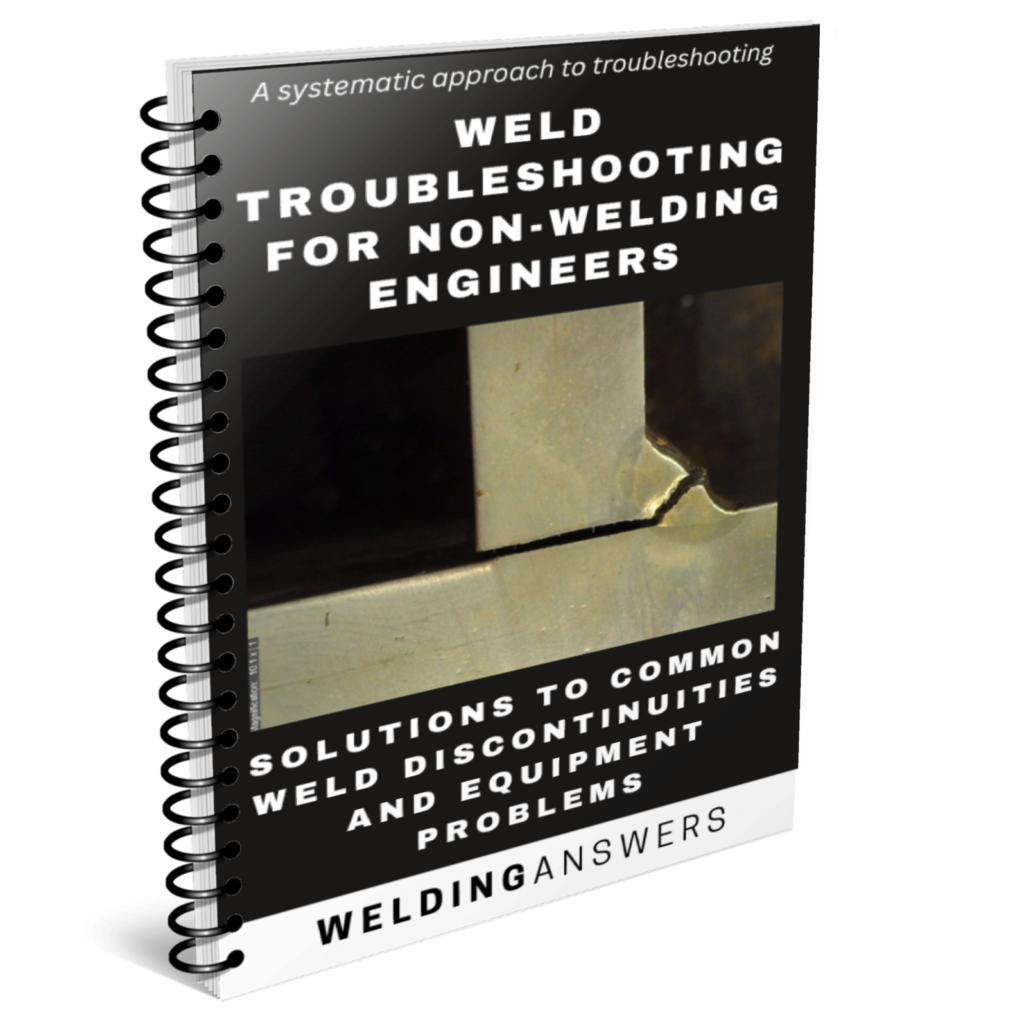