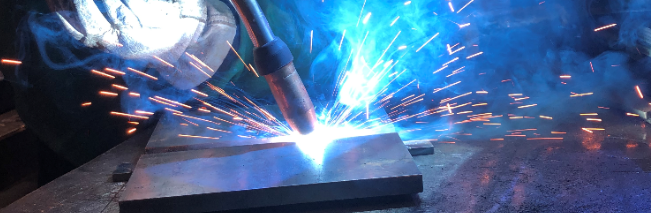
Whenever you hear that a welding procedure needs to be qualified it simply means that its suitability for use in a welded structure needs to be proven by testing. This means that the welding procedure must be capable of producing sound welds. But what are sound welds? Sound welds are welds that will perform in accordance with design criteria. A weld may simply need to provide an air-tight, or liquid-tight seal between two components (as in an oil drain pan). Or it may need to provide sufficient strength and ductility to bear heavy and varying loads under cyclic service while also providing adequate corrosion resistance (as in ocean oil rigs).
To determine if a welding procedure is fit for use in production of welded structures and components, a fabricator must run a weld test and then use both nondestructive and destructive testing to ensure it meets the acceptance criteria. Most often, this acceptance criteria is dictated by a welding code, standards or specification. The code, specification or standard to use primarily depends on the material being welded and its application. Some of the most common welding codes are:
- AWS D1.1 Structural Welding Code – Steel
- AWS D1.2 Structural Welding Code – Aluminum
- AWS D1.6 Structural Welding Code – Stainless Steel
- ASME Section IX – Boiler and Pressure Vessel Code
- API 1104 Welding of Pipelines and Related Facilities
Tests that are commonly used to test suitability for use include: visual inspection, tensile strength testing, hardness testing, impact toughness testing, corrosion resistance and more.
So, to qualify welding procedures follow these four steps:
- Determine the acceptance criteria – this may be as simple as identifying the applicable structural code or standard. Many times this is provided by the owner of the project and specified in contract documents. Other times, you simply need to look at the work you’ll be doing and pick the standard yourself.
- Develop a welding procedure for testing – many times a welding procedure already exists, but needs to be qualified. In this case simply run that procedure on your test plate. If the procedure does not meet the acceptance criteria after being tested you’ll need to develop a welding procedure and retest.
- Perform the weld test – this is often referred to as running PQR plates or tests. PQR stands for procedure qualification record. If you run the weld test and the welded plates (or pipe sections) meet the acceptance criteria of the applicable code then the exact parameters used for welding are documented in a PQR form. In addition to simply stating amps and volts, the PQR must also record other essential variables such as shielding gas composition and flow rate (if using a gas process), travel speed, heat input, welding position, base metal thickness, joint type, etc.
- Write the Welding Procedure Specification (WPS) – the qualified welding procedure is written using the PQR as a base. The code or standard uses will provide allowed ranges for the many essential variables. For example, if you are following AWS D1.1 (Steel) to qualify a GMAW WPS and your PQR shows that the weld test was done with the following parameters:
- 300 amps
- 28.5 volts
- 15 in/min travel speed
Your WPS ranges would be as follows based on what’s allowed by the code (see Table 6.5 of AWS D1.1 excerpt below)
- 270 – 330 amps (300 +/- 10%)
- 26.7 – 30.5 volts (28.5 +/- 7%)
- 11.3 – 18.8 in/min travel speed (15 +/- 25%)
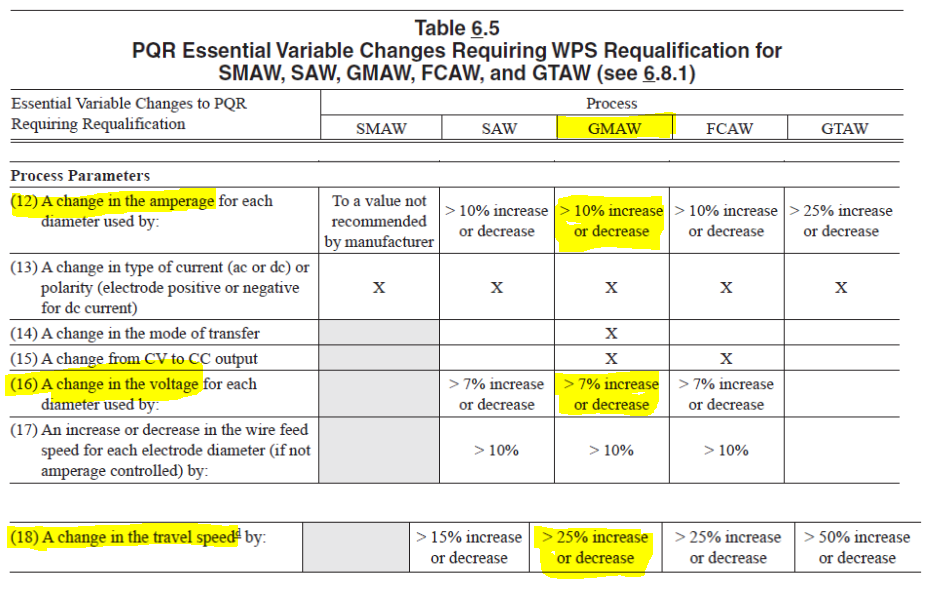
Portion of Table 6.5 PQR Essential Variables Requiring Requalification of WPS from the American Welding Society D1.1/D1.1M:2020 Structural Welding Code (Steel)
If you pull out your copy of AWS D1.1 and go to Table 6.5 you’ll see that there are allowable ranges for 37 different essential variables. Not all apply to all processes as can be seen above. Any boxes filled in with gray shade do not apply to the process.
As you can imagine, all the testing required to qualify a procedure takes time and money. Some codes allow the use of Prequalified Welding Procedures. A prequalified welding procedure is exempt from testing but it must follow all the rules of prequalification imposed by the code. To learn more about prequalified WPSs you can read What is a Prequalified Welding Procedure.
If you need AWS D1.1 qualified welding procedures you have the following options:
- Use prequalified welding procedures if your specific application allows by following the Prequalification clause of AWS D1.1.
- You can do this yourself, or
- You can purchase them
- Develop and qualify your welding procedure in accordance with the Qualification clause of AWS D1.1
Most of the work with do with our consulting customers is with structural steel so we have develop and written the following resources which are available for purchase:
2. Qualification of Welding Procedures, Welders and Welding Operators per AWS D1.1 Structural Welding Code (Steel)
3. Welding Procedure Development for Non-Welding Engineers – Complete guide on how to develop a welding procedure (how to select all of the essential variables such as amps, WFS, volts, travel speed, torch angles, CTTWD, preheat, shielding gas composition, shielding gas flow rate, PWHT, etc.)
Please note: I reserve the right to delete comments that are offensive or off-topic.