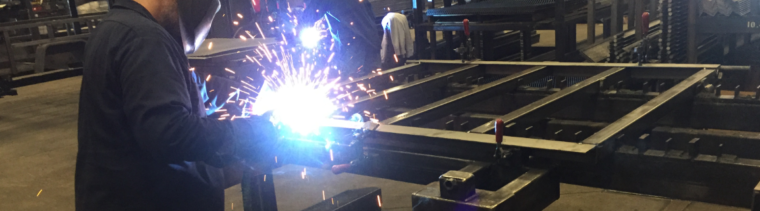
It is not a secret that increasing our deposition rates, measured in pounds per hour (kg per hour in metric units), can result in increased productivity. Deposition rate is the rate at which we are depositing weld metal. It is different from the melt-off rate. Melt-off rate is the rate at which we consume our electrode. The deposition rate is simply the melt-off rate multiplied by the efficiency of the electrodes.
For instance, if we are running a mig wire at a wire feed speed that produces a melt-off rate of 7 lb/hr and the electrode efficiency for spray transfer is 97%, the deposition rate is
Deposition Rate = Melt-off Rate x Electrode Efficiency
Deposition Rate = 7 lb/hr x 0.97 = 6.79 lb/hr
Why would we want to increase our deposition rates?
Simply, higher deposition rates result in faster travel speed and thus higher productivity. This reduces our welding time. Increasing deposition rates is typically accomplished by increasing wire feed speed in arc welding processes such as SAW, GMAW and FCAW (this results in an increase in amperage) or simply by increasing amperage in processes like SMAW.
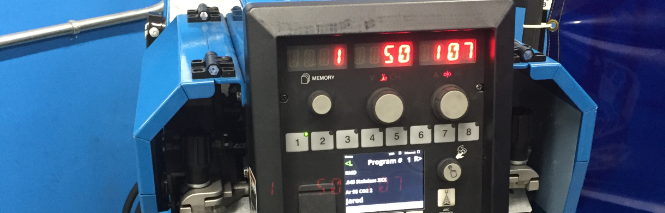
Another way to achieve higher deposition rates is to increase the electrode diameter. Typically, once a welder is running an electrode at its top end (at or near the point of current saturation) it becomes necessary to switch to a larger wire diameter and increase the amperage. It’s important to note that if you increase electrode diameter it can result in a lower deposition rate if your amperage is not increased accordingly.
Higher deposition rates allow us to weld faster. For example, if a weld takes 1 minute to make using a welding procedure that produces a deposition rate of 4 lb/hr, the same weld can be made in 30 seconds, half the time, if we increase the deposition rate to 8 lb/hr. Increasing travel speed is the key. If you increase deposition rate from 4 to 8 lb/hr, but the travel speed does not change you are simply making a larger weld and increasing your costs. The exact opposite of what you set out to do.
Challenges when increasing deposition rates
There are several challenges associated with increasing deposition rates. All of these challenges can be addressed when there is a welding quality standard in place, welding procedures available to the welder and proper training. However, many fabricating shops lack one, two or all three of these very important items.
Here are some of the most common challenges faced by fabricators when trying to gain productivity by increasing deposition rates.
- Higher deposition rates result in bigger weld puddles requiring faster travel speeds and many welders don’t have the skill necessary to go faster and be able to deposit sound welds.
- Higher deposition rates may create quality problems. This is related to point 1 above. If a welder is unable to keep an acceptable travel speed it may result in lack of fusion – this can occur when the puddle rolls over ahead of the arc or to the side when welding in horizontal position.
- Higher deposition rates change essential variables and may require additional testing associated with qualifying a new welding procedure. Although the cost of qualifying a new welding procedure can be minimal, the lack of understanding of the economic impact of increasing travel speeds makes many fabricators believe it is not worth it. So they do nothing.
- Increasing deposition rates is not possible because the available welding equipment is limited on amperage, thus being unable to run larger electrode diameters or even increase the amperage on the existing electrode diameter.
- Increasing deposition rates may result in increased costs, as already explained above. . If travel speeds are not adjusted accordingly the result will be bigger welds without time savings. This increases material costs due bigger welds. Bigger welds can also introduce other problems, such as welding discontinuities like lack of fusion, overlap and distortion. To learn more about these issues read Bigger (Welds) are not always better.
- Higher deposition rates may not be good for welding out of position. Increases in deposition rates which result in bigger puddles are not always feasible for out-of-position welding. In many shops, rather than having different parameters for different weld joints and positions, welders will choose a happy medium. This often results in a welding procedure that is OK for out-of-position welds, but significantly slow for in-position welds.
As previously stated, these challenges can be addressed when there is a quality standard in place, welding procedures available to the welders and proper welder training.
Have you tried increasing deposition rates to increase welding productivity? Were the changes sustained? What types of gains did you experience?
____________________________________________________________________
Are you looking to qualify welding procedure and/or welders? Are you using AWS D1.1 Structural Welding Code -Steel as your quality standard?
“Qualifying Welding Procedures, Welders and Welding Operators” is a guide developed to help you perform your own qualifications in full compliance to AWS D1.1 Structural Welding Code. It provides step-by-step instructions on how to qualify welders and welding procedures. It also provide step-by-step instruction on the proper use of prequalified welding procedures.
__________________________________________________________________
Are you in need of AWS D1.1 prequalified welding procedures? This collection provides welding procedures for several arc welding processes. These procedure cover 14 of the most common welding joints, all positions and the most common wire diameters for each process.
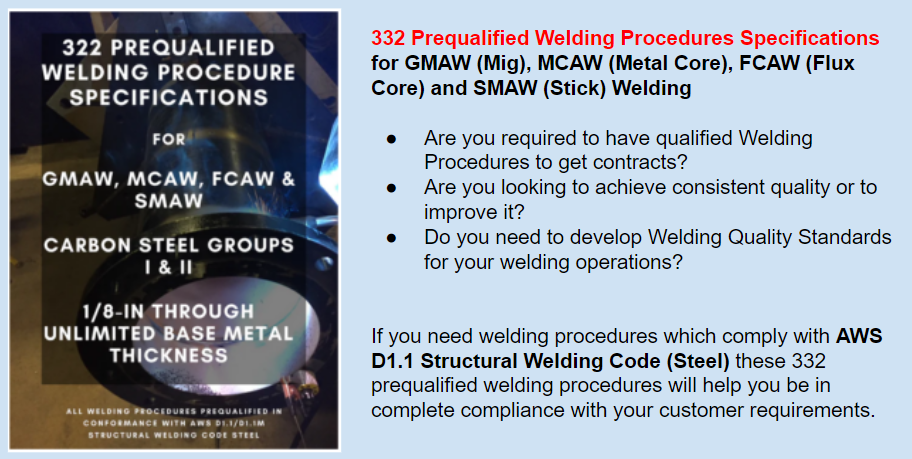