How To Qualify A Welding Procedure
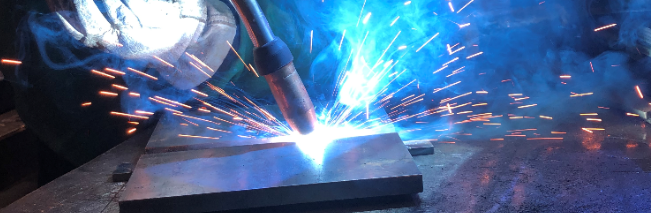
Whenever you hear that a welding procedure needs to be qualified it simply means that its suitability for use in a welded structure needs to be proven by testing. This means that the welding procedure must be capable of producing sound welds. But what are sound welds? Sound welds are welds that will perform in […]