3 Effective Ways to Reduce Welding Rework
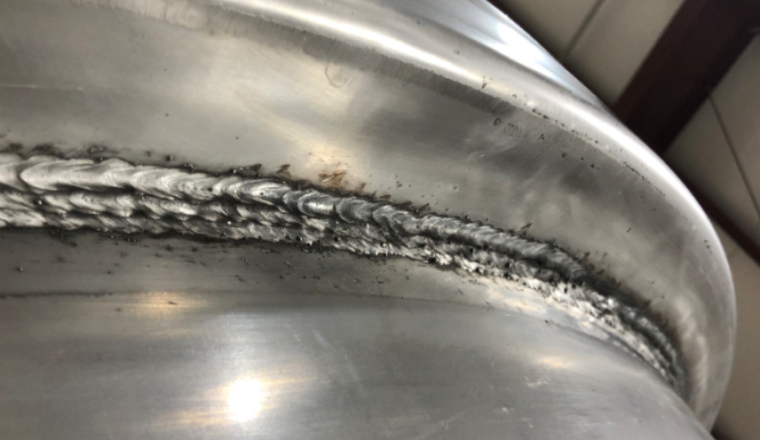
Rework is extremely costly, especially in welding. If you consider what happens when a weld is rejected it is essentially triples the amount of work. You weld, you remove the weld, you reweld. On top of this it may require additional inspection. So, reducing rework can save considerable amounts of time and money.