Short-arc vs Globular Transfer in GMAW
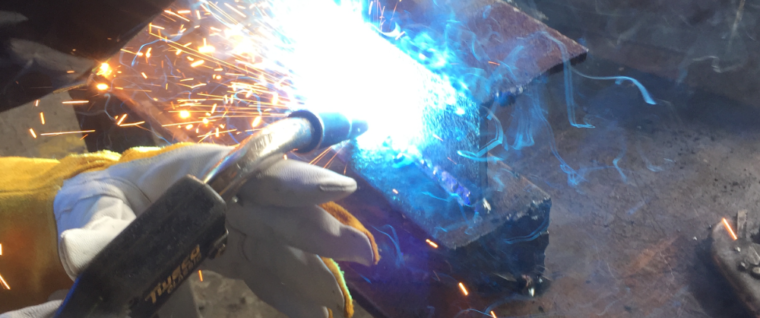
What is the difference between globular and short-circuit transfer? Short-circuit is a mode of metal transfer in GMAW in which metal is transferred from the electrode to the weld pool via a series of electrical shorts. When the electrode (wire) touches the base material a short occurs and the arc goes out. At this point […]