Submerged arc welding is typically done automatically, meaning it is not done by hand, but rather set up as hard automation. The operator simply controls the welding machine and torch position to obtain the desired results. Typically,the system is run by an operator, not a welder. So when problems come up, the operator may not have the experience necessary to troubleshoot the weld and make the necessary procedural adjustments. Porosity is a common problem which may be hard to troubleshoot. Many times we think nothing has changed in the fabricating process, but if we take a close look at all the variables we can identify the reasons behind porosity.
Below is a list of the most common causes of porosity in submerged arc welds. By going through this list you’ll notice that most of these issues can change without your knowledge. Whenever porosity becomes a problem go through the list below to correct the issue.
Poor grade of steel – The chemistry of steel typically has no effect on susceptibility for porosity, but here is one element that can really give you problems: sulfur. This is especially a problem when welding free machining steels. Increasing sulfur content increases the machinability of steel, but can create problems when welding. Even when sulfur content is within the allowed ranges it can be an issue due to segregation. This means that sulfur is not evenly distributed throughout the steel, but can accumulate in certain areas. If you are facing this problem you have the following options: minimize admixture by using lower currents to penetrate less (not always an option) or travel slower to allow more time for the sulfur to degas.
Joint cleanliness – Even with the high heat input provided by the SAW process, joint cleanliness is very important. Rust, oil, paint and other contaminants can cause porosity in submerged arc welds. Clean the joint properly to remove any contaminants.
Flux contamination – If flux is not properly stored it can pick up moisture and be contaminated and this may cause porosity. When a flux recovery system is used, it is very important to make sure that no slag is being picked up. It is highly recommended to use a magnetic separator to prevent metallic particles from contaminating the flux. Lastly, it is important to add new flux to the recovered flux, a 50/50 mix is ideal.
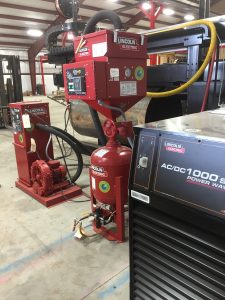
Flux recovery systems should include filtering screens, magnetic separators and a way to add virgin flux to maintain an adequate mix of recovered and new flux.
Electrode contaminations – Like flux, wire that is improperly stored can pick up moisture. Moisture pick up on solid wires will cause rusting. Rust will increase the probability of porosity so it is vital that proper storage procedures be followed. Don’t forget about the coils of wire sitting on the equipment. When a coil of wire remains on the wire feeder over a weekend it can pick up enough moisture to rust.
Insufficient flux coverage – Flux provides atmospheric shielding similar to what shielding gas does for GMAW. If there is not enough flux to shield the arc porosity can occur. However, it is important not to use too much flux as it can affect bead shape. The amount of flux used is directly proportional to the distance between the nozzle and the work piece. Insufficient flux coverage typically occurs on roundabout welds. The smaller the diameter of the part the harder it is to prevent flux spillage. It is not recommended to use SAW in outer diameters of less than 6 inches.
Tack welds – If tacking is done with SMAW electrodes or FCAW wires, it is necessary to completely remove the slag. Slag left in tack welds can create porosity when welding over them with SAW. Don’t small amounts of slag will be removed by the welding arc.
Arc blow – Arc blow is caused by magnetic fields induced by the welding arc. These magnetic fields may cause the wire to wander, moving in and out of the joint. This creates an erratic arc. To reduce or eliminate arc blow, weld away from the work connection (ground clamp) or switch to AC polarity if feasible.
Travel speed – Higher travel speeds are more susceptible to porosity due to faster weld solidification times. The longer the weld puddle remains molten, the longer the gases generated by the welding process have to escape..
There are other causes for porosity, but the above eight usually account for about 90% of the causes.
References: The Procedure Handbook of Arc Welding, 14th Edition
Lincoln Electric Submerged Arc Welding Guide
Hello,
I am SAW operator/welder in a pipe fabrication company and from time to time I get pores which happen on a segment of a pipe when doing longitudinal welds. Now it happened 3 or 4 times in circular welds out of 100+ pipes but more on linear/longitudinal welds. These are counted as butt welds although they are rolled and fitted with slight gap on the outer side and almost zero in inner part. Pore itself not very big but it is deep down to the “groove”( groove being made because it is sheet metal rolled to be pipe segment). I tried welding towards the ground clamp and increased the current by 5 amps, new flux as well and I got nice results with it, while my colleague did not when slowed and decreased amps. We did it as a test even if it was a workpiece which somehow approved my theory that I went hotter then my colleague. Please tell me if you agree with me and if there is some sort of advice you would share.
Porosity is sometimes caused by not allowing enough time for the gases to exit the weld. If that is the case what you want is more energy to keep the puddle molten longer. A 5 amp increase is mimial in submerged arc welding, but it does increase energy. Going slower will keep the puddle molten longer, but decreasing the amperage will speed up solidification. So what you did and what your colleague did are relatively similar. There are many causes for porosity. Sometimes it is not as easy to troubleshoot and you must use trial and error, as you did in this case. If you’re changes made the situation better then keep doing that. But it is important to determine the root cause of porosity to really understand what solved the problem.
Don’t forget to look into the following:
1. Any changes to the base material (surface condition, metal preparation, gap, type of metal)
2. Check MTRs. Is sulfur content in check?
3. Condition of the flux. How is it stored? Can it be picking up moisture?
4. Atmospheric conditions. Has humidity increased?
5. Is the arc steady? Welding towards the ground is typically not recommended as it can cause arc blow.
there are other things to check but start with the ones above.
good day ,.i have tough slag removal problems with sub Arc welding ,can you suggest anything.
rob.
If the groove isn’t too narrow and you are having a hard time detaching the slag your voltage may need to be adjusted. You should aim for a relatively flat weld face. If your weld is excessively convex (too ropey) you will trap slag. Also, if it is too concave it will also trap slag. If your weld it too ropey (convex) increase the voltage. If it is too concave decrease the voltage.
may i come to know the cause of porosity in GMAW
And what to do to prevent the same..?
affect of porosity on weld.
We have a post that should help you get started: https://weldinganswers.com/7-ways-to-eliminate-porosity-in-your-welds/