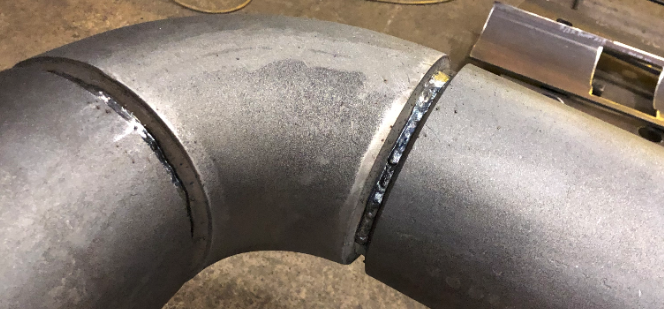
Interpass temperature is the temperature of the base metal in and adjacent to the weld joint prior to depositing and additional pass (weld). Maintaining and measuring interpass temperature should be done carefully. Different materials require different levels of preheat and interpass temperature. For this reason it is extremely important that both prehat and interpass temperature be specified in the welding procedure. To illustrate the importance of interpass temperature let’s go through a real life example.
A while ago a fabricator of pressure vessels was looking to reduce costs in their welding operations. As mandated by the ASME Boiler and Pressure Vessel Code this fabricator had welding procedure specifications (WPSs) and procedure qualification records (PQRs) in place. These were properly written, tested and documented.
The WPS called for a minimum preheat and interpass temperature of 225˚F on a 24-inch diameter pressure vessel having a wall thickness of 3.5 inches. The vessel was preheated with oxyfuel and Tempil sticks were used to verify that the right preheat temperature had been reached. The mistake made by the operator (welding was done with the submerge arc welding process) was assuming that the interpass temperature (temperature in between passes) was being kept at least at 225˚F. What we found was that the interpass temperature was lower than 150˚F immediately next to the weld and lower than 90˚F when taken 3.5 inches away from the weld. This is almost room temperature!

The minimum interpass temperature must be maintained during welding in order to prevent rapid cooling and potential issues with cold cracking.
So why do we have minimums for preheat and interpass temperature? And why is it dangerous to not adhere to these requirements?
The reason why we use preheat when welding carbon steels, especially thick sections, is to slow down the cooling rate. By slowing down the cooling rate we avoid the formation of martensite. A martensitic structure is very hard and brittle. Neither of these characteristics is particularly desirable in a pressure vessel.
This can be a very dangerous condition for the following two reasons:
- When our interpass temperature is below what is specified we risk having a cooling rate that is fast enough to form martensite. Once we have a martensitic microstructure in and around the heat affected zone (HAZ) we have a much higher susceptibility to hydrogen induced cracking. As you can imagine, a crack on a vessel which is under pressure is a very bad thing.
- When following welding codes there are safety factors that allow us some room for mistakes. Pressure vessel design can be done in different ways. By design we mean the selection of the steel and the thickness necessary for the desired application (pressure, temperature, etc.). One design approach is “leak before burst.” This means that the design is such that if a crack were to develop it would grow slow enough that it would create a leak which would relieve the pressure from the vessel rather than a rapid growth which could lead to catastrophic failure.
In this type of design the microstructure of the weld and HAZ is extremely critical and it must be exactly as specified. But if we have rapid cooling during production welding, we increase hardness and lose ductility. This may not be enough to lead to hydrogen induced cracking, but overtime if a crack develops it may not be suitable to slow its growth. The hard, brittle microstructure could and probably would lead to brittle failure.
This particular manufacturer had been building pressure vessels for years without a single failure due to not maintaining interpass temperature. How is this possible?
There are two likely reasons:
- The conservative approach (safety factors) provided by the welding code. The proper cooling rate may very well be achieved with a preheat of 100˚F, but maybe to be safe and to account for difficulties in manufacturing, especially out in the field, 225˚F is what is specified.
- The heat input from the submerged arc welding process is high enough that the right cooling rate is still achieved even with a low interpass temperature. Codes such as AWS D1.1 have allowances for this.
We should be careful how we take this. This is not a license to be careless. Following the established welding procedure carefully is absolutely necessary. It is important to keep in mind that catastrophic failures are almost always a combination of many different things rather than just one.
What if there is user error and the service pressure is double than what the vessel was designed for? What if there was lack of fusion that was not detected by the radiographic testing? What if corrosion has thinned the wall of the pressure vessel? What if the vessel was sent for service in Alaska rather than the Caribbean as was originally expected and now it is in much less forgiving ambient temperatures? If any of these things were to happen, having applied the proper preheat and having maintained adequate interpass temperature would lessen the chances of failure.
Reference: Welding Metallurgy and Weldability by John C. Lippold
hi
Good article, fight with Fitters and Welders daily with regards to Preheat and Interpass temps.
Good article, fight with Fitters and Welders daily with regards to Preheat and Interpass temps.
It can be a struggle. At times all we can do is convey the importance of adhering to procedures and hope that the level of professionalism of our welders is such that they will execute as per the WPS. Most times what I fight are incorrect notions such as the thinking of that the welding arc is hot enough to keep the part hot.