Hydrogen-induced cracking (HIC) is a far too common type of failure. It is also called hydrogen assisted cracking (HAC) and delayed cracking since it does not occur right after welding, but a few hours or days after the weld has completely cooled down to ambient temperature. Cracking occurs due to a significant loss in ductility in the weld metal and/or heat affected zone (HAZ).
In his book Welding Metallurgy and Weldability, John C. Lippold, a welding engineering professor at Ohio State explains that there are three factors that contribute to hydrogen-induced cracking. These factors are:
- Threshold level of hydrogen
- Susceptible microstructure
- Restraint level
There are several theories to explain the mechanism for HIC, but simply put, hydrogen introduced into the weld will diffuse to the HAZ of a susceptible microstructure (such as martensite and bainite), and form a crack when the material cools and enough restraint is present.
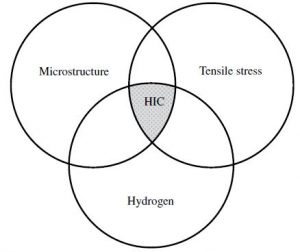
In order for hydrogen-induced cracking to occur all three factors need to be present. Eliminate one and it can’t happen.
The three factors explained:
Threshold level of hydrogen – Although most materials contain at least traces of hydrogen, the hydrogen associated with HIC is introduced during the welding process. Hydrogen introduced into the weld during welding comes from three sources:
- Moisture in the electrode, flux, shielding gas or environment
- Decomposition of cellulosic-type electrode coatings and combustion products of oxyfuel gas welding
- Contaminants containing hydrogen (i.e. grease, oil, cutting fluids, water, etc.) on the surface of the material to be welded
Low-hydrogen practice minimizes or eliminates these sources to prevent HIC.
Susceptible microstructure – In steels there can be a wide array of microstructures depending on the composition of steel and the welding process parameters. Hard and brittle microstructures are the most susceptible to HIC. These microstructures are usually the product of fast cooling rates which tend to form martensite or bainite on most steels. Keep in mind that simply looking at the composition of a base material and determining the carbon content or carbon equivalent is not enough to know the microstructure after welding. The heat input of the welding process and the preheat, or lack thereof, are significant factors in the final microstructure. In general, fast cooling rates should be avoided. Consult with the appropriate code for preheat, post weld heat treatment and interpass temperature requirements.

The microstructure of a weld and the heat affected zone is a product of the base material composition and the heat effects of the welding process and cooling rates.
Restraint level – The level of restraint is determined by the stress and strain state of a weld resulting from factors such as clamping and fixturing, geometry of weld joint, thickness and strength of the base metal, presence of weld discontinuities and residual stress. Out of the three factors this is typically the one that is hardest to control.
Remember that for HIC to occur you need all three factors. Seek to eliminate the ones you can most easily control. Avoiding hydrogen in the weld is typically the easiest to affect, followed by control of microstructure. To learn more about reducing susceptibility to cracking due to hydrogen read Preventing Hydrogen Induced Cracking.
Source: Welding Metallurgy and Weldability by John C. Lippold
Hi All,
Thank you for this useful information.
regards