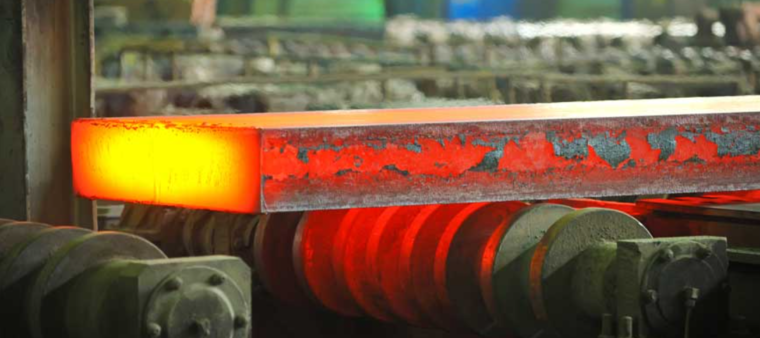
It is often incorrectly assumed that quenched and tempered (Q&T) steels are hard to weld or even completely unweldable. This assumption is inaccurate as most Q&T steels have great weldability. However, extreme care must be taken to prevent cracking or loss of certain mechanical properties. A very common quenched and tempered steel is ASTM A514. You may know this steel as “T-1 Steel.” This is an Arcelor Mittal trade name.
Three very important mechanical properties of steels are strength (tensile and yield), hardness and fracture toughness. Typically as hardness increases so does strength, but fracture toughness decreases. Quenched and tempered steels, as the name suggests are quenched to increase hardness and later tempered to regain some of the ductility and fracture toughness that was lost during quenching. The welding process can radically change the microstructure of this steel making it very susceptible to hydrogen cracking. Or it can have an annealing effect which softens the material and lowers the strength and hardness.
Welding of A514 and other Q&T steels requires an understanding of the desired mechanical properties of the welded connection after welding. If you recall from two weeks ago, weld strength and weld toughness (fracture toughness) are inversely related. So as strength (and hardness) goes up toughness goes down. So with high strength you typically have lower ductility and lower fracture toughness. With high fracture toughness you typically have to give up some strength. Q&T steels attempt to give you the best of both worlds. Manufacturers of Q&T steels do a phenomenal job of this and then we change it all with the welding process. The goal is to minimize the extent to which we change it.
So how does welding affect the properties of quenched and tempered steels?
Let’s look at two scenarios:
- We preheat to a temperature lower than that required by the manufacturer of the Q&T steel or we weld with extremely low heat input. Or worse, we do both. In this case the steel will experience rapid cooling. This will cause hardness levels to increase. This process takes a microstructure that is already susceptible to hydrogen induced cracking and elevates the risk significantly. If we are lucky enough to avoid cracking of the weld or heat affected zone, we will definitely lose a good amount of ductility. Fracture toughness is also decreased.
- We preheat to an excessive temperature or we exceed our interpass temperature or we weld with extremely high heat input. Or we do two of these, or worse, all of them. In this case the cooling rate will be extremely slow. This will have an annealing effect on the weld and heat affected zone. This creates a significant drop in strength (yield and tensile strength) as well as hardness. Conversely, ductility and fracture toughness would increase. Perhaps a better outcome than scenario one since there is little susceptibility for cracking, but if does not meet the in-service demands we may face equally undesirable results.
Because we are trying to avoid things that are essentially complete opposites, a sound welding procedure must be developed. This welding procedure should minimize the changes in hardness, strength, ductility and fracture toughness. This can become a balancing act, so we must prove the welding procedure by testing.
If you are working with AWS D1.1 Structural Welding Code (Steel) you will see that A514 is an approved base metal, but it is not approved for use with prequalified welding procedures. This means that any welding procedure for welding A514 used on a project governed by AWS D1.1 must be qualified by testing.
It is worth noting that some Q&T steels can be easily welded and are approved by AWS D1.1 for use with prequalified welding procedures. Examples of these steels are API 2Y grades 42, 50 and 60 as well as ASTM A709. The API 2Y steels have specified minimum tensile strength levels of 75ksi or less. A709 can get as high as 110ksi. There are also quenched and self-tempered steels such as ASTM A913 grades 50, 60, 65 and 70 which are also approved for use with prequalified welding procedures.
Developing a welding procedure for Quenched and Tempered Steels
As we have noted, the welding procedure for Q&T steels should be carefully developed and tested. To put it simply, we need to have a welding procedure with just the right amount preheat, interpass temperature and heat input from the welding process. ASTM A709 is used in the fabrication of bridges and its use is addressed in AWS D1.5 Bridge Code. This code, in Table 12.7 provides the minimum and maximum preheat and interpass temperatures to use with this Q&T steels based on their thickness and the heat input from welding. This table also assumes (since it is required) that welding will be done with a low hydrogen process. This means that the deposited weld metal will have a maximum hydrogen content of 8mL per 100 gram of weld. Whether you are building bridges or using A709 for other structural applications, this table is absolutely essential. Let’s take a look at how to use this valuable table.
EXAMPLE: You are tasked with developing a welding procedure for making a complete joint penetration weld on ASTM A709. This base material has a thickness of 2 inches. You want to use the submerged arc welding (SAW) process as it provides high deposition rates which are great for productivity. You want to use a proven procedure that has been used on ASTM A572 in the past. This procedure, based on amperage, voltage and travel speed, has a heat input of 58.5 KJ/in.

The submerged arc welding process is capable of depositing 20+ lb/hr of weld metal. This means high amperages and large weld nuggets which carry a high heat input. Recommended preheat and interpass temperatures for welding Q&T steels may need to be adjusted downward due to this high heat input.
You now have to pick adequate preheat and interpass temperatures. Getting this wrong could mean ending up with a heat affected zone that will be susceptible to cracking or ending up with a situation where you don’t have adequate strength in your welded connection. So you turn to Table 12.7 of AWS D1.5 to get your answers. If you read it right, you’ll see that for ASTM A709 with thicknesses over 1 inch and up to 2 inches, and a heat input between 50 and 70 KJ/in from the welding process, the required preheat and interpass temperature is 250˚F – 400˚F. This means that your minimum is 250˚F and your maximum is 400˚F for both preheat and interpass.
If you follow these guidelines you are well on your way to developing a welding procedure that will yield acceptable results. Although you are following proven guidelines, the welding procedure may still require qualification by testing. Examine the contract documents for the requirements detailed by the engineer in charge. In some cases even though a code may allow for the use of prequalified welding procedures, the owner of the project may dictate that you qualify or procedures by testing.
What about post weld heat treatment (PWHT) of Q&T steels?
In general, PWHT is not recommended for Q&T steels. However, in some cases this is necessary to maintain dimensional stability during machining. If this is the case you must be aware of the implications. These are: potential loss of notch (fracture) toughness in the heat affected zone and potential intergranular cracking.
For additional information including filler metal selection you can read Recommendations for Welding T-1 Steel.
References: AWS D1.5/D1.5M:2015 – Bridge Code
AWS D1.1/D1.1M:2020 Structural Welding Code – Steel
Qualification of Welding Procedures, Welders and Welding Operators (2020)
The Procedure Handbook for Arc Welding – 14th Edition
Are you working with AWS D1.1 Structural Welding Code (Steel) and need welding procedures?
Our publication 322 Prequalified Welding Procedure Specifications for Steel Fabricators provides prequalified WPSs for SMAW, GMAW, MCAW, FCAW-G and FCAW-S in full comformance with AWS D1.1 Structural Welding Code – Steel.
If you only need prequalified welding procedures for a specific process (GMAW, SMAW, FCAW, MCAW) those are available as well. Simply visit our online store to choose what you need.
322 Prequalified Welding Procedure Specification for Steel Fabricators
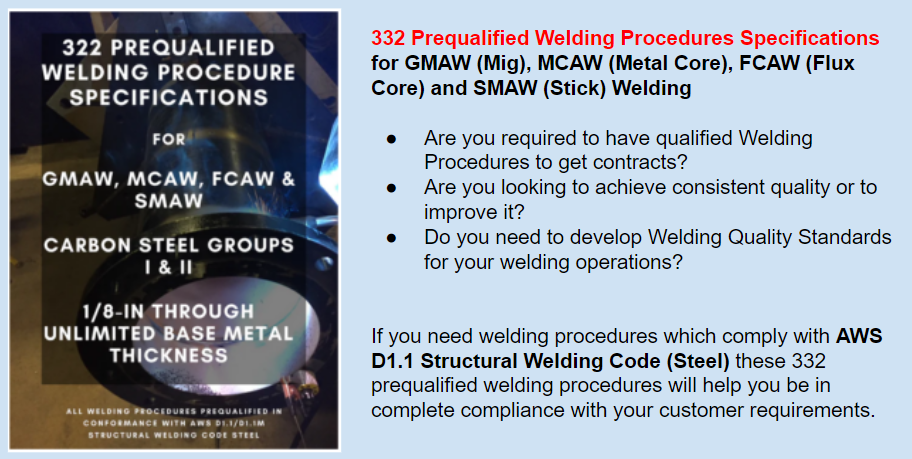