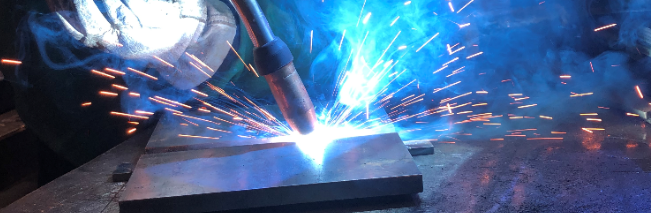
Spray is a mode of metal transfer in which a fine spray of metal droplets are projected axially from the tip of the electrode to the work. These droplets are smaller in diameter than the electrode. This mode of transfer is characterized by high wire feed speeds (high amperage), high voltage and consequently high heat input. It produces a very fluid weld puddle so it can only be used in the flat and horizontal positions.
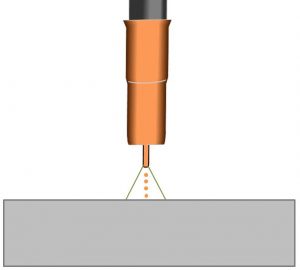
In spray transfer fine droplets are transferred through the arc. This produces deep penetrating and typically spatter free welds.
The welds produced with spray transfer are characterized by deep penetration and excellent bead appearance, provided proper welding technique is used.
In order to achieve spray transfer the welding procedure should be such that it provides amperage above the transition current and the corresponding voltage to achieve a stable arc. The amperage level at which we attain spray transfer is dependent primarily on two variables:
- Shielding gas composition
- Electrode diameter
As we learned when discussing short circuit and globular transfer, the mode of transfer is directly influenced by amperage, voltage, current (amperage) and shielding gas composition. In order to achieve spray transfer the shielding gas should contain at least 80% argon (inactive/inert gas) with the balance being most commonly carbon dioxide and in some cases oxygen (at levels of 5% or lower). Gases of these compositions provide a stable medium for the metal droplets to transfer smoothly through the arc.
Because different gas mixtures have different energy levels and other specific characteristics, spray transfer is achieved at different current levels for a specific electrode diameter depending on the shielding gas composition.
As explained above, you need at least 80% argon in your mix to achieve spray transfer. But there is a large number of shielding gas mixtures. For now we’ll stick with some of the most common ones. The chart below shows the current at which spray is achieved for a specific electrode diameter and shielding gas combination.
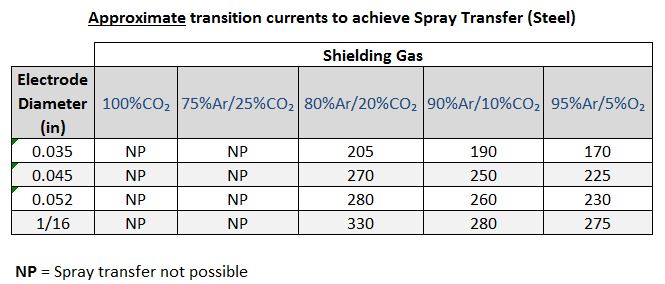
Electrode diameter, shielding gas composition and amperage are the most important variables in determining transfer mode.
The chart above provides the estimated current at which spray transfer can be achieved. There are other factors that will affect the arc such as voltage. If your voltage is too low your arc will be erratic and you won’t have a good transfer. You also need to pay attention to other factors that affect amperage, such as your contact-tip-to-work distance (CTTWD). This is the main reason why the chart shows amperage rather than wire feed speed. For a given wire feed speed the resulting amperage will decrease as your CTTWD increases and vice versa. So keep that in mind.
It is important to note that as the percent of argon increases in the shielding gas the transition current is lower for a given electrode diameter. Spray transferred can be achieve at a much lower current when using 95/5 (argon/oxygen) than with 90/10 (argon/carbon dioxide). But before you go changing your gas for this reason don’t forget all the other things that your shielding gas composition can affect.
Advantages of Spray Transfer
- High heat input which can provide deep penetrating welds
- Higher wire feed speeds (amperage) produce high deposition rates which increase productivity
- Very clean, spatter free welds possible
- Good choice for thicker sections (1/4-inch and thicker)
- Allows for use of prequalified welding procedures
Limitations of Spray Transfer
- Use is limited to the flat and horizontal positions due to puddle fluidity
- Potential for burn-through on thinner materials
- Potential for undercut due to high voltage levels
- More expensive gas than for short circuit or globular
- Higher levels of radiated heat – uncomfortable for the welder
References: Steel Design Guide 21: Welded Connection – A Primer for Engineers
Hello, many thanks on these set of articles on Mig transfer modes. How could I factor the chart above for .030 wire and Ar/CO2 92-8 % (Air liquide Arcal 21). I have a Kemppi minarc 180 – I beleive limited to 24 volts but also a Jasic 200 28 volts both Europe single phase 230 v input. I have built my workshop with non supportive welds (support is bolted) with 394 inch per min and 21 V with the Kemppi and I read outputs in the 158 to 180 amps – was that some hybrid of short circuit and spray ? But how can I reach spray settings on 0.030 and a 24 V limit. Many thanks ans best regards. Serge
With smaller diameter wires it gets more difficult to achieve spray. However, for an .030″ wire you should be in spray around 145 – 160 amps with 92/8 gas. This is an estimate but should be confirmed through testing/trial.
the chart you provided, is that based off of your experience or is that a chart you obtained from a separate source?
Hello Scott. This is based on experience. The number are approximate. I placed specific values for simplicity but I much rather prefer a range for about 5-7 amps.
I just asked about tank size ,was reading about pulse spray trans. again, up till now Ive been using short circ, for 1/4 in and thinner so spray wouldn’t work too well? You had a guide for spray , current to break into, My Power mig 300 is in synergenic ? weld mode 11 .035 wire in Wire feed speed not amprage ,so I’d have to switch to pwr mode to get current input ? I think I’m asking how does amp correlate to WFS, I’m asking Lincoln elec. but they act like they don’t understand the Question !
Jerome P.S. Very good guides
THe Power Mig 300 should display amperage as you are welding (in the same window that was showing Wire Feed Speed). It will display amperage as you weld and will hold that display for 5 seconds after you are done welding. So strike an arc, weld for a few seconds and then stop and check the display for your amperage. Its best to have someone look at it as you are welding since the weld termination is sometimes erratic and can give you a very low or high reading.
I would stick with Mode 11 as Mode 40 (Power Mode) can be a little tricky to use.
The wire feed speed that corresponds to a specific current is affected by the contact tip to work distance. If you go to the spec sheet of the filler metal you are using you’ll find recommended settings. For .035″ ER70S-6 wire you get about 195 amps when running 375 inches per minute and have a contact tip to work distance of 1/2 – 3/4in and running 90/10 gas. Voltage should be around 23-24 volts. Keep in mind that you can be way above the transition current but not really have spray transfer if your voltage is too low.
The relationship between wire feed speed and amperage is directly proportional. As your wire feed speed goes up so does the amperage. Good luck.