3 Mistakes that lead to distortion in welding
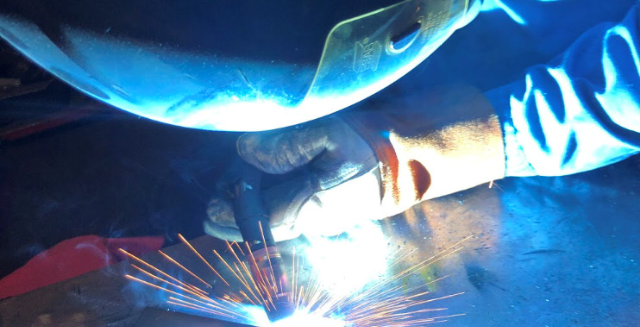
Distortion caused by the heating and cooling cycles of welding is extremely problematic. It can place structures out of dimensional tolerance creating costly rework. In some cases parts need to be scrapped. Understanding the causes of distortion and the properties of the metal being welded are an absolute necessity for those managing welding operations. There […]