Tag Archives: welding procedure specification
Welding Procedure Development: Qualification
Welding Procedure Development: Selecting Welding Parameters
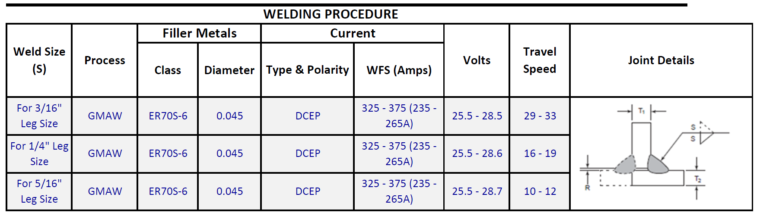
When writing a welding procedure one of the most critical steps is selecting our welding parameters. This means determining the appropriate amperage and voltage as well as other critical aspects that the welder must adhere to such as travel speed and travel and work (transverse) angles. What follows is an explanation as to the importance […]
Welding Procedure Development: Selecting the right welding process

Selecting the best welding process is a critical step in developing a welding procedure that attains the desired quality and optimizes productivity. Many times we look for the welding process that can give us the highest deposition rate to optimize productivity. However, every welding process has limitations. For example, submerged arc welding (SAW) has extremely […]
Understanding the Difference between Qualified and Prequalified Welding Procedures
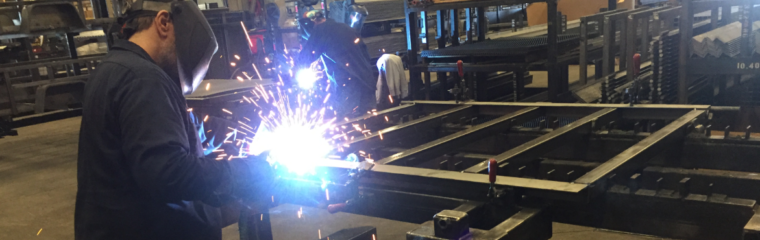
One of the most common questions we get around the topic of welding procedure qualification is regarding the differences between qualified and prequalified welding procedures. The main question is typically: is one better than the other? Before we answer this question, let’s first discuss the need for qualified, or prequalified, welding procedures. If you have […]
7 Things to Consider When Choosing the Best Welding Process for your Welding Procedure
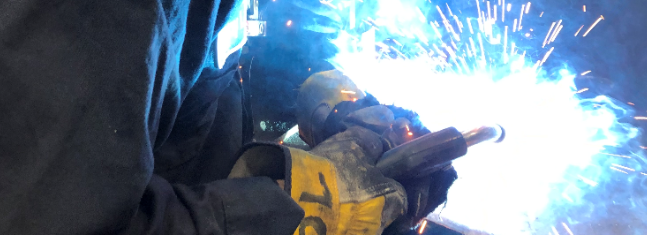
Selecting the best welding process is a critical step in developing a welding procedure that attains the desired quality and optimizes productivity. Many times we look for the welding process that can give us the highest deposition rate to optimize productivity. However, every welding process has limitations. For example, submerged arc welding (SAW) has extremely […]
How to get a Qualified Welding Procedure Quickly
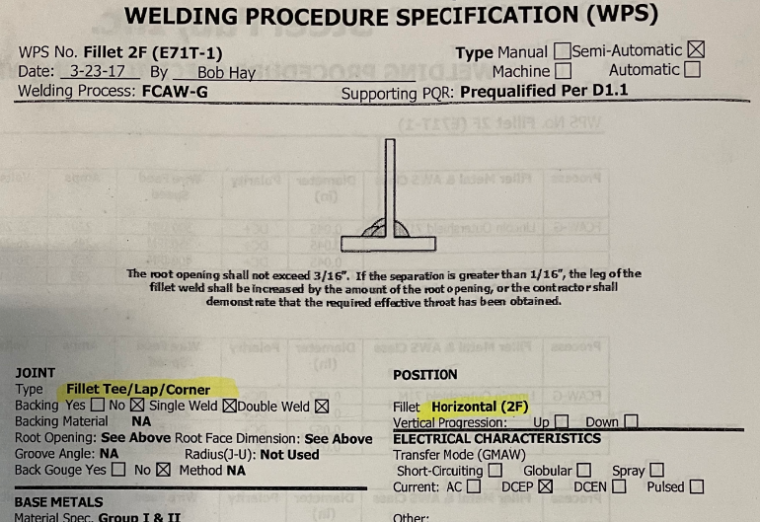
Have you ever been in a situation in which you need a qualified welding procedure immediately? Maybe you just failed an audit and have to halt production until a valid welding procedure is provided. Or maybe you’re just in a hurry to get started with a new job. Regardless of the reason you need the […]
Importance of Weld Failure Analysis
Basic guidelines to troubleshoot weld failures
21 Changes to PQR Essential Variables that Require WPS Requalification
Have you ever seen a welding procedure specification with established amperage ranging from 200 to 550 amps? Or voltage ranging from 21 to 29 volts? Or some other variable with a huge window? This is all too common, but extremely dangerous. Why? Because changes to essential variables beyond that which is reasonable will affect the […]
Why prequalified welding procedures are exempt from testing
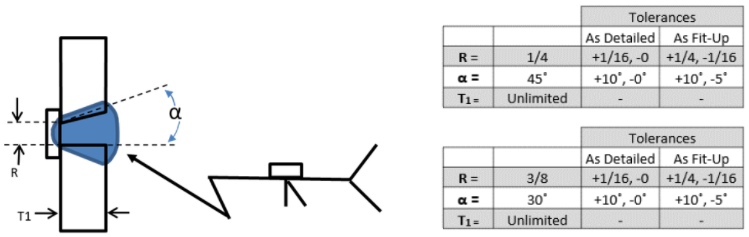
One of the advantages of using prequalified welding procedures is that you can save a lot of time and money because they are exempt from testing. This means you don’t need to perform any destructive or nondestructive testing. You simply follow the requirements of AWS D1.1 and you can write a prequalified welding procedure and […]