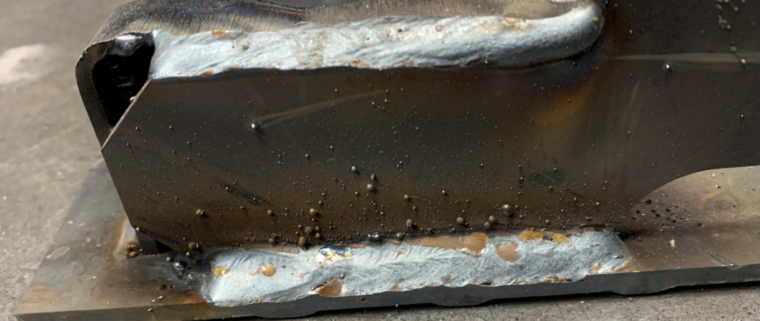
Spatter is present in welding. It’s all over welding. But it doesn’t have to be. Spatter costs fabricators millions of dollars every year. Its removal constitutes rework that significantly and negatively impacts productivity. Many fabricators work under the assumption that spatter is a necessary evil, a part of welding. However, this couldn’t be further from the truth. Welding spatter can be reduced or even eliminated. In order to get rid of spatter we first need to understand what causes it.
Spatter is not just the product of one or two things. Rather, it can be caused by a multitude of welding factors. Below are 17 causes of spatter. Once you identify which of the below items are causing spatter in your welding operations you can take corrective action and start saving thousands of dollars. If you don’t think that spatter is costly, you must read The Real Cost of Welding Spatter.
17 Reasons you are getting spatter:
1. Amperage (current) set too high – high currents for a given voltage in wire processes will generate spatter. There should be a balance between amperage and voltage for any wire diameter and any mode of metal transfer (short arc, globular, spray, pulsed spray). If your current is too high simply lower it by reducing the wire feed speed in CV process or reducing the amperage in CC processes. You can also increase your voltage if you don’t want to reduce your deposition rates.
2. Voltage set too low – this is essentially the same as having your amperage too high. You must have a good balance between voltage and current (amperage). Adjust your voltage accordingly to reduce spatter.
3. Bad fit up – inconsistent fit up leads to spatter. This happens because the welder will need to compensate for variations in gaps and other fit up problems. In order to prevent blowing through a gap, especially on thin material, a welder will pull a long arc. This increases the contact-tip-to-work (CTTWD) distance which reduces amperage and reduces the punch, or the ability to penetrate. This is good because it prevents blowing through the part, but it generates spatter. In this case, the cure is to fix your fit up problems and allow your welder to produce spatter-free welds. To learn more about the damaging effects of bad fit up read The Outrageous Cost of Poor Fit Up.
4. Incorrect torch angles – torch angles (or electrode angles) include transverse angle and travel angle. Transverse angle is the angle at which you position the electrode in relation to the weld joint. For example, in a fillet weld, you want to direct your electrode right at the joint, this requires a 45-degree transverse angle. If you are welding a butt joint you may be at a 90-degree transverse angle. Your travel angle is whether you push or pull (drag). All arc welding processes with the exception of submerged arc welding (subarc) will require a push angle of 10-15 degrees or a pull (drag) angle of 10-15 degrees. Exceeding 15 degrees, whether you push or pull, will generate spatter.
5. Choice of shielding gas – in general, the more carbon dioxide in your shielding gas the more spatter you will generate. As the amount of argon or other inert/inactive gas increases your arc becomes more stable and generates less spatter. With this being said, even with 100% carbon dioxide there is a lot that can be done to minimize spatter. To learn more about consideration when selecting a shielding gas read Should You Consider a Different Shielding Gas.
6. Contaminated filler metal – the filler metal, whether it is the welding wire, stick electrode or even the flux can cause spatter if it is contaminated. Contamination usually is due to moisture. In copper coated wires and some bare wires rust will form on the surface and this can lead to spatter.
7. Contaminated gas – As with electrode contamination, shielding gas contamination is usually due to excessive moisture levels. For most binary gas mixes the maximum moisture content is in the order of 80 ppm, yet some cylinders will exceed this amount by many times.
Spatter Reduction Guide
Subscribe to get our latest content by email and receive your FREE Spatter Reduction Checklist!
8. Mode of metal transfer – different modes of metal transfer have different arc characteristics. Short circuit transfer (short arc) will produce spatter regardless of how optimized the welding parameters are, but the spatter is usually very low energy so it does not fuse to the base metal. However, it will generate spatter and in some cases it will fuse to the base metal requiring clean up by grinding, chipping or other methods. Globular transfer is the worst when it comes to spatter. It is very violent and produces large “globs” of spatter that tenaciously adhere to the base metal. Spray transfer and pulsed spray transfer are very smooth and can be spatter-free, provided all other variables are optimal.
9. Surface contaminants – contaminants such as moisture, rust, mill scale, dirt and other hydrocarbons will produce spatter and/or porosity.
10. Surface coatings – similar to surface contaminants, coating such as zinc (galvanized), aluminum (aluminized), paint and others will generate spatter. The best thing to do is to remove the coating by grinding prior to welding. Many times this is not desired due to the cost of doing so. However, rework, including spatter clean up, proves to be more costly almost every time.

Galvanized and aluminized steel is highly susceptible to spatter generation. Optimized welding procedures can reduce the amount of spatter but it is extremely difficult to completely eliminate it.
11. Lack of welder skill – this one should go without saying. Welder skill is essential in any process to produce sound welds. Bad habits, such as excessive weaving, whipping and other erratic arc manipulations will lead to spatter.
12. Work lead connection problems – if you do not have a good work connection (commonly, but erroneously referred to as “ground”) you will get spatter. This is due to poor connections leading to voltage loss.
13. Erratic wire feeding (wire processes) – if wire feeding is not smooth you will get spatter along with other more serious problems such as lack of fusion, overlap and other weld discontinuities. Erratic feeding is an equipment problem and proper troubleshooting should be performed. To learn more about the causes and solutions for erratic wire feeding read Troubleshooting Erratic Wire Feeding.
14. Wet flux or electrode coating – as mentioned above, electrode contamination due to moisture can generate spatter. It is imperative that electrodes be stored in accordance with the manufacturers recommendations.
15. Slow travel speeds – slow welding travel speeds, specifically in the flat, horizontal and vertical down positions will lead to spatter. This is due to the molten puddle running ahead of the arc causing the wire to feed into the puddle rather than the base metal.
16. Excessive whipping or weaving – this is related to poor operator skill. Weaving and whipping are common practices, but they can lead to problems such as spatter, lack of fusion and overwelding. Every time the arc goes around and into the puddle spatter is generated (similar to when we have extremely slow travel speeds).
17. Blocked nozzle – a blocked nozzle in gas-shielded arc welding processes will reduce gas coverage which in turn affects the arc. Typically, this causes porosity, but it can reduce gas coverage enough to also generate spatter.

Nozzles usually get clogged due to excessive spatter. This, in turn, can generate even more spatter due to inadequate shielding gas coverage.
There you have it, 17 reasons why you are getting spatter. Believe it or not, there are plenty more reasons for spatter. Can you think of others? If so, please shoot us an email and we’ll add it to the list.
Reference: