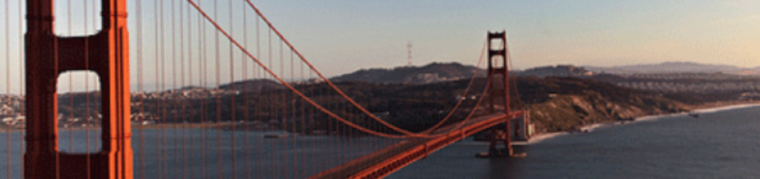
If you work with metals, whether you are a business owner, a design engineer, an inspector or a welder, you have heard the terms yield strength and tensile strength. In welding, we seem to focus more on tensile strength than on yield strength. When we match a filler metal to a base metal we do it based on tensile strength. When we determine the allowable shear stress on a weld we use the minimum specified tensile strength of the filler metal. All AWS electrode classifications reference tensile strength as in ER70S-6 for GMAW filler metals where the “70” means 70,000 psi minimum tensile strength.
Although it almost seems like tensile strength is all we should worry about, it is very important to understand yield strength. In this article we’ll cover both yield and tensile strength. We’ll start by defining the two, explaining the differences in behavior and explaining the importance. We’ll then provide an example of how this works in the real world.
Yield Strength
Definition: Yield strength is the amount of stress at which a material begins to deform plastically, or undergo permanent deformation, without any increase in the load.
Behavior: Before reaching the yield point, the material deforms elastically, meaning it returns to its original shape once the applied stress is removed. Beyond the yield point, plastic deformation occurs, and the material retains some amount of deformation even after the stress is removed.
Significance: Yield strength is crucial in designing structures or components that need to withstand loads without undergoing permanent deformation. It is a measure of the material’s ability to resist deformation under load.
Tensile Strength
Definition: Tensile strength is the maximum stress that a material can withstand while being stretched or pulled before necking, which is the point where the material begins to significantly contract.
Behavior: Tensile strength is the highest point on the stress-strain curve, representing the maximum stress a material can endure. Beyond this point, the material undergoes necking and eventual failure.
Significance: Tensile strength is important in applications where the material is subjected to stretching or pulling forces. It provides information about the material’s ability to withstand maximum loads without breaking.
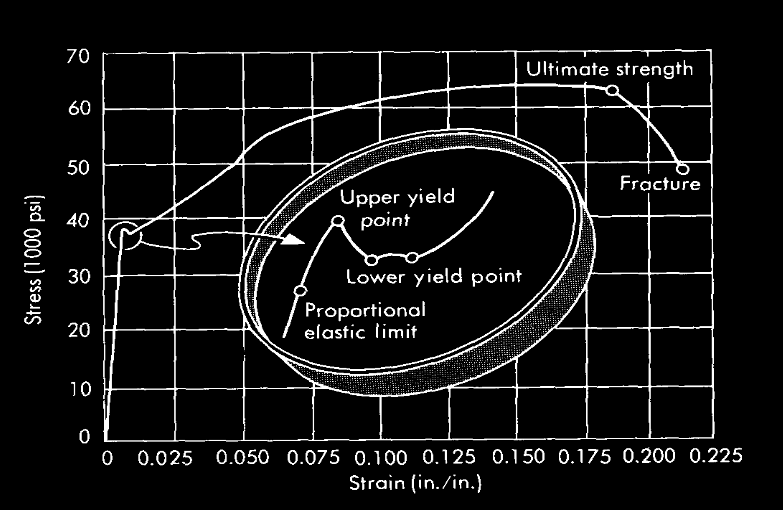
It is important to know the stress level at which a steel structure will start to experience plastic deformation (yield strength) and the ponit at which it wil fracture (tensile strength).
In summary, the key difference lies in their definitions and the points on the stress-strain curve at which they are measured. Yield strength is associated with the onset of plastic deformation, while tensile strength is associated with the maximum stress a material can endure before failure. In general, yield strength is used for designing structures, as it indicates the point at which permanent deformation may occur, while tensile strength is a measure of the material’s maximum strength under tension.
Now let’s go through a simple real-life example.
Consider a bridge made of steel that has been welded together. Bridges often experience a variety of loads, including the weight of vehicles, dynamic forces from traffic, and environmental factors like wind and temperature changes.
Now, let’s imagine a scenario where a heavy truck is crossing the bridge. As the truck moves across the bridge, the steel structure is subjected to a significant load. If this load exceeds the yield strength of the steel, plastic deformation will occur.
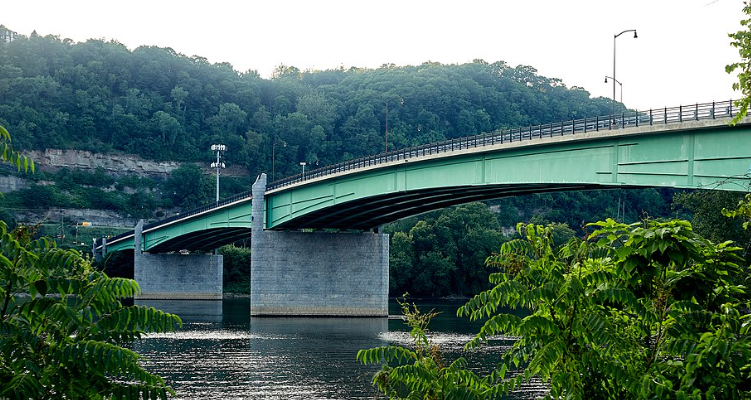
Bridges are subjected to variable loads which place several of its members under tension and compression. It is not only the vehicles that create fluctuating stresses on the bridge, fluctuating winds also affect the fatigue life of the bridge.
In this situation we have exceeded the yield strength. The stress from the weight of the truck and any additional dynamic forces may exceed the yield strength of certain welded sections of the bridge. This means that the steel in those sections will undergo plastic deformation. The affected parts may experience some permanent deformation, like bending or warping.
In this scenario, we exceeded the yield strength but did not exceed the tensile strength. The overall stress on the structure might still be below the tensile strength of the steel. This is crucial because it means that, although plastic deformation is occurring, the structure is not on the brink of failure or rupture. The steel is stretched and deformed beyond its elastic limit but has not reached the point of ultimate failure.
This scenario illustrates the importance of understanding both yield strength and tensile strength in structural design. Engineers must ensure that structures can withstand the expected loads without undergoing catastrophic failure. In this case, the bridge might experience deformation, but it remains intact because the tensile strength has not been surpassed, preventing a complete structural failure. Regular inspections and maintenance would likely be necessary to monitor and address any plastic deformation that occurs over time.
References:
__________________________________________________________________
Are you looking to qualify welding procedures and/or welders? Are you using AWS D1.1 Structural Welding Code -Steel as your quality standard?
“Qualifying Welding Procedures, Welders and Welding Operators” is a guide developed to help you peform your own qualifications in full compliance to AWS D1.1 Structural Welding Code. It provides step-by-step instructions on how to qualify welders and welding procedures. It also provide step-by-step instruction on the proper use of prequealified welding procedures.