What is a Prequalified Welding Procedure Specification
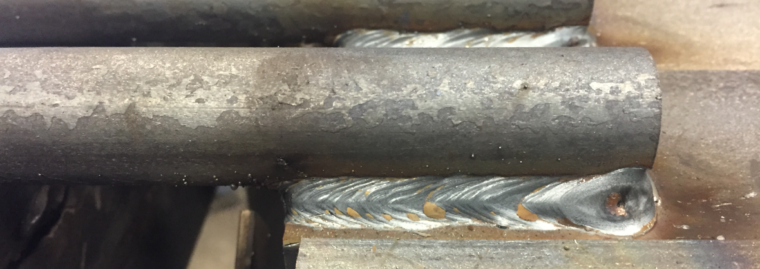
A prequalified welding procedures specification is a welding procedure that is exempt from the qualification tests required by a code or standard. Not all codes provide the user with the advantage of using prequalified welding procedures. Some that do are: AWS D1.1 Structural Welding Code – Steel AWS D1.3 Structural Welding Code – Sheet […]