The Importance of the Heat Affected Zone (HAZ)
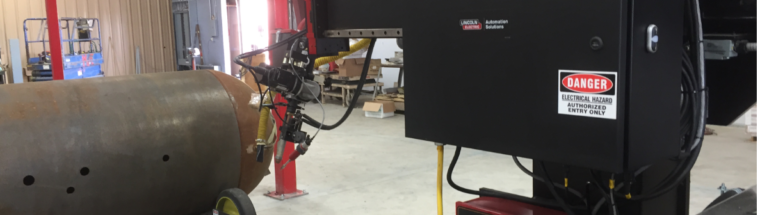
When we weld we generate enough heat in the welding arc to melt the filler metal and base material. Or just the base material is we are welding autogenously (as in GTAW without filler). The edges of the base material melt and combine with the filler metal to create what is called the composite zone. […]