5 Methods to Determine Preheat Temperature
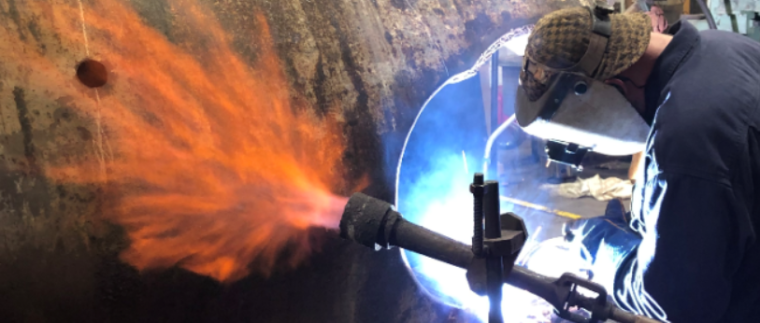
Preheat is used when a base material, due to its chemical composition, thickness or level or restraint, is susceptible to cold cracking (hydrogen induced cracking). Knowing what temperature to preheat your base metal is sometimes a complicated matter. You may hear people say “preheat to 300F to be safe.” The reality is that 300F may […]