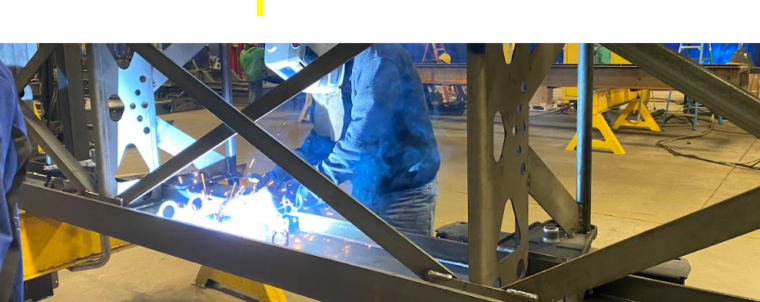
We frequently receive questions regarding the preheating, welding, and post-weld heat treatment of ASTM A514 and other quenched and tempered steels. If you’re working with these materials, the following guidelines will be extremely helpful for welding this steel and avoid cracking or other problems.
Metallurgy, Uses, and Welding Challenges of ASTM A514
ASTM A514, often referred to by the trade name “T-1” (a trademark of ArcelorMittal), is a high-strength, low-alloy (HSLA) steel. It’s quenched and tempered to achieve exceptional yield strengths exceeding 100,000 psi (690 MPa). This heat treatment process creates a martensitic microstructure, which provides the steel with its high strength and hardness.
- Metallurgy: The quenching and tempering process involves heating the steel to a high temperature, rapidly cooling it (quenching), and then reheating it to a lower temperature (tempering). This process refines the grain structure and forms martensite, a very hard and strong phase.
- Uses: Due to its high strength-to-weight ratio, ASTM A514 is widely used in heavy-duty structural applications, including:
- Heavy equipment construction (e.g., cranes, bulldozers)
- Bridges and structural supports
- Pressure vessels (ASTM A517, a related specification)
- Welding Challenges: The high hardness and hardenability of ASTM A514 make it prone to cracking after welding. The heat affected zone (HAZ), the area of base metal that is not melted during welding but has had its microstructure and properties altered by welding heat, can become excessively hard if proper welding procedures are not followed. This high hardness can lead to:
- Hydrogen-induced cracking (HIC)
- Reduced ductility and toughness
- Premature failure of the welded joint.

AWS D1.1 Structural Welding Codes (Steel) identifies A514 and A517 as approved base metals for structural applications, but requires qualification by testing. This means that prequalified welding procedures are not permitted with these base metals. Both are grouped together by other reference material such as the Procedure for Arc Welding (14th Edition) meaning that both should follow the same recommendations for welding.
While ASTM A514 and A517 exhibit good weldability, careful consideration of the welding process and procedure is crucial.
Key Elements for Successful Welding of ASTM A514 Steel:
- Selection of the Correct Electrode or Electrode/Flux Combination
- To match the high strength of the base metal, use electrodes with Mn-Ni-Cr-Mo alloying elements.
- The weld metal should have a minimum tensile strength of 100,000 psi and Charpy V-notch toughness of at least 20 ft-lbs at -40°F.
- For submerged arc welding (SAW), use filler metals with an AWS classification of F11A6-ECM2-M2-H8 (e.g., Lincoln Electric 880/LAC-M2).
- For gas metal arc welding (GMAW), use ER100S-G/ER110S-G dual-classified wire.
- Lower-strength filler metals (e.g., ER70S-6) can be used, but this requires engineering approval due to reduced strength. However, unless you are making complete penetration welds (CJPs), undermatching may be beneficial. Keep in mind that the amount of dilution will ultimately determine the strength of the weld metal.
- Use low-hydrogen electrodes for all welding processes (SMAW, FCAW, GTAW).
- Adequate Welding Procedure and Preheat/Post Weld Heat temperatures
- Follow the steel manufacturer’s recommended preheat temperatures, which vary with plate thickness:
- Up to 1/2″: 50-100°F
- Over 1/2″ to 1″: 50-150°F
- Over 1″ to 2″: 150-200°F
- Over 2″: 200-250°F
- Highly restrained joints may require higher preheat temperatures.
- Maximum preheat and interpass temperatures are crucial for quenched and tempered steels:
- 400°F for thicknesses up to 1-1/2″
- 450°F for thicknesses over 1-1/2″
- Measure preheat temperature 3 inches from the joint (or a distance equal to the plate thickness, if greater than 3 inches).
- Control welding parameters (amps, volts, travel speed) to ensure proper fusion and controlled heat input.
- When using undermatching filler metals, the depth of penetration will dictate the final strength of the weld. Not only penetration into the root which increases the effective throat of the weld, but also higher penetration increases dilution which in this case will increase the strenght of the deposited filler metal compared to the filler metal’s specified minimum tensile strength.
- ASTM A514 requires qualified welding procedures (WPS) as it is not a prequalified base metal per AWS D1.1.
- Follow the steel manufacturer’s recommended preheat temperatures, which vary with plate thickness:
- Use Recommended Fabrication Practices
- Minimize hydrogen-induced cracking by controlling hydrogen sources:
- Use dry electrodes, flux, and shielding gas.
- Avoid cellulosic-type electrodes.
- Clean the base metal to remove contaminants (grease, oil, moisture).
- Slow cooling allows hydrogen to diffuse out of the weld.
- GMAW solid wire produces the least amount of hydrogen.
- SAW flux must be stored and handled with great care due to the possibility of moisture absorption.
- Minimize hydrogen-induced cracking by controlling hydrogen sources:
- Exercise Caution with Post-Weld Heat Treatment (PWHT)
- PWHT (typically above 700°F) should only be performed if it benefits the microstructure.
- Slow cooling is necessary, but is not considered PWHT. Thermal blankets can be used.
- Proper preheat and a controlled welding environment can often eliminate the need for PWHT.
- AWS D1.1 provides guidelines for PWHT and WPS qualification.
- AWS D1.1 establishes that preheat and interpass temperatures must be established based on the steel’s composition and provides ways to determine these temperatures in Annex B (2020 edition).
Welding ASTM A514 (T-1) steel can be done successfully by adhering to proper procedures. By selecting the correct filler metals, implementing appropriate preheat and welding parameters, controlling hydrogen input, and carefully considering PWHT, you can achieve sound and reliable welds.
Please note: I reserve the right to delete comments that are offensive or off-topic.