Tag Archives: welding costs
6 Challenges When Increasing Deposition Rates
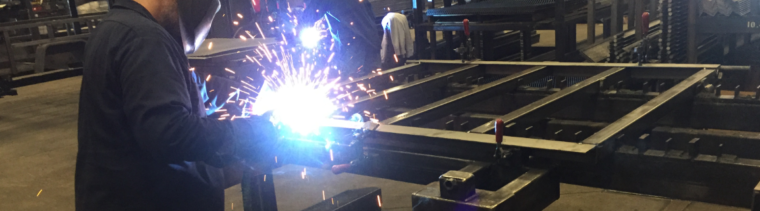
It is not a secret that increasing our deposition rates, measured in pounds per hour (kg per hour in metric units), can result in increased productivity. Deposition rate is the rate at which we are depositing weld metal. It is different from the melt-off rate. Melt-off rate is the rate at which we consume our […]
Who is responsible for determining weld size?
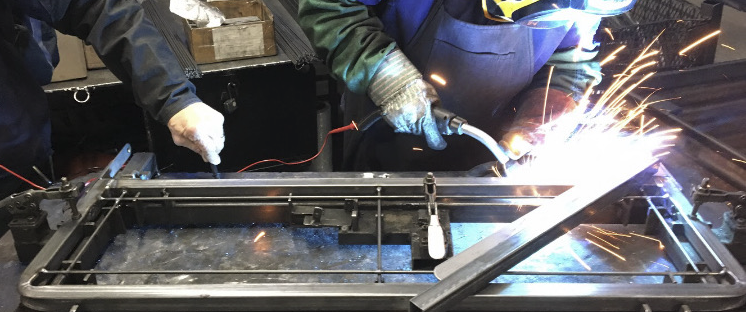
Who determines what size a weld should be? This is a question we ask many of our customers. And we never seem to get a straight answer. In a perfect world, the design engineer should specify all weld sizes and clearly communicate this through welding symbols on the print. But that is hardly ever the […]
3 Mistakes that lead to distortion in welding
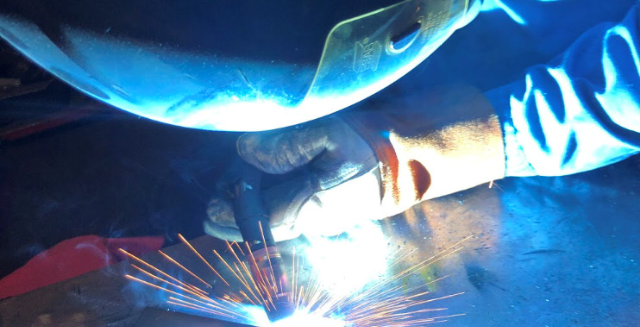
Distortion caused by the heating and cooling cycles of welding is extremely problematic. It can place structures out of dimensional tolerance creating costly rework. In some cases parts need to be scrapped. Understanding the causes of distortion and the properties of the metal being welded are an absolute necessity for those managing welding operations. There […]
3 Key Factors Affecting the Quality and Cost of Welds
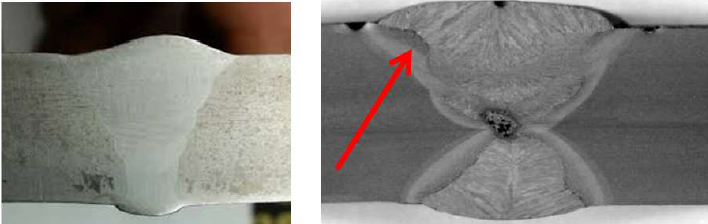
Quality and cost go hand in hand, or at least they should. Poor quality may be cheap during the fabricating process, but very costly when it comes to warranty repairs and potentially losing customers. Many of the companies we work with have seen substantial cost reductions when we help them address quality concerns. For the […]
5 Common Mistakes Made When Estimating Welding Costs
Read this before you bid on a welding contract
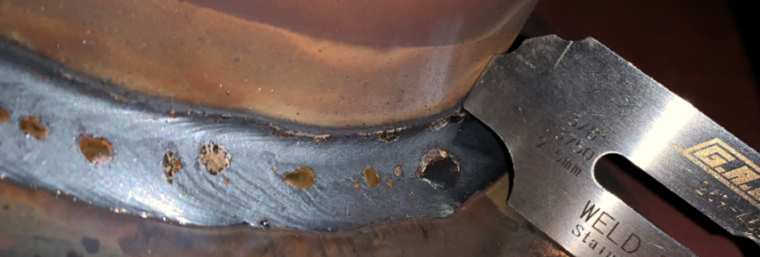
When bidding jobs several fabricators end up calculating their costs associated with welding and then double that number to be safe. In some cases, that isn’t even enough. It is important to have a clear understating of how to translate the amount of welding to be done to actual manufacturing costs. One of the biggest challenges is that rework and overwelding is […]
Rule of Thumb for Fillet Weld Sizes
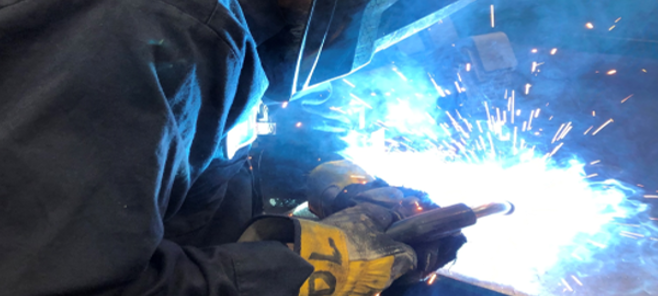
Many fabricators can lower their welding costs significantly if they paid close attention to weld sizes. If a print calls for a ¼” fillet weld and in production you make a 5/16” fillet weld, you are overwelding by 56%! If the print calls for a 3/16” fillet, the 5/16” fillet weld you deposit would be […]
The Outrageous Cost of Poor Fit Up in Welding Operations
You will cringe when you read this
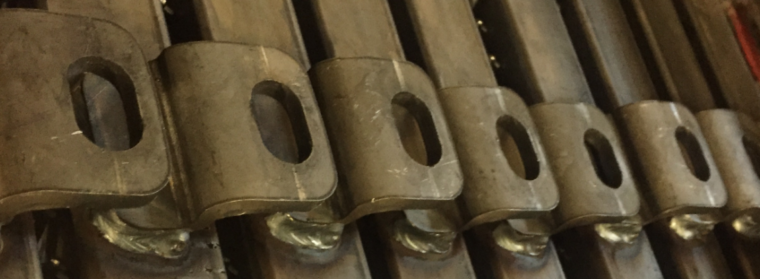
In a perfect world parts would fit together perfectly every time. However, as we all know, this isn’t the case. We mostly think of poor fit up as something that annoys welders but which they can compensate for. But the reality is it can have tremendous impact on your bottom line. Or, in many cases, […]
Why You Must Have Welding Procedure Specifications
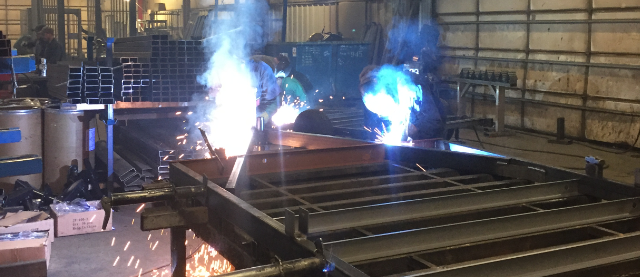
Our previous article discussed the importance of having a specification for weld quality. In this article we’re talking about the importance of one of its basic components: Welding Procedure Specifications (WPSs). Many fabricators don’t have WPSs. They rely in the experience of their welders to select the right parameters. As much as we want every […]
Importance of Macro Etch Testing of Welds
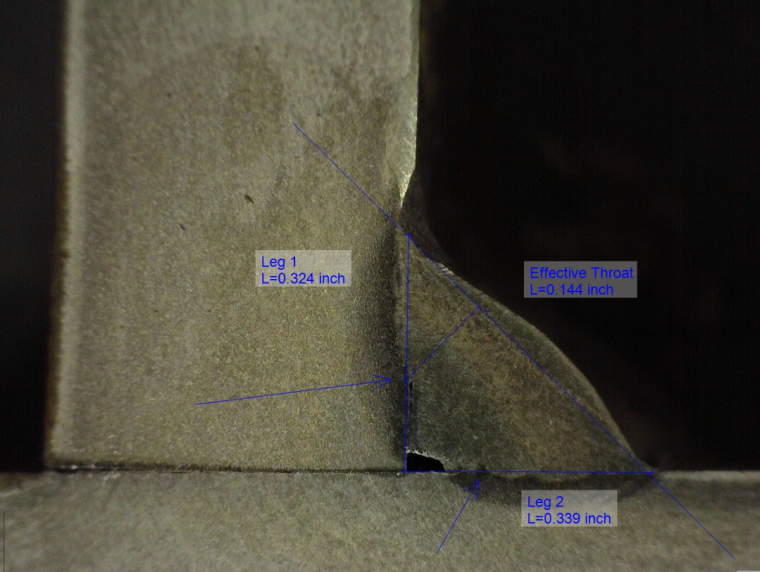
Macro etch tests are commonly done as part of qualification tests for welders and welding procedures. This test is relatively easy to do and does not require complex or expensive equipment. However, very few fabricators ever perform this test. A macro etch test can serve as verification that a change on how something is welded […]