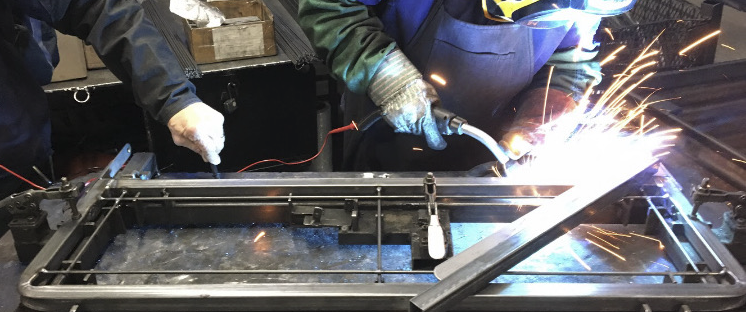
Who determines what size a weld should be? This is a question we ask many of our customers. And we never seem to get a straight answer. In a perfect world, the design engineer should specify all weld sizes and clearly communicate this through welding symbols on the print. But that is hardly ever the case. A lot of fab shops are building products to their customers specifications. Sometimes these specifications have drawings which include welding symbols and weld sizes. Other times they are nothing more than dimensional drawings.
So when your shop is fabricating without weld sizes having been specified by the end customer or by your engineering department, who determines weld size? More often than not it is the welder. Right, wrong or indifferent, welders are making decisions on weld sizes all the time.
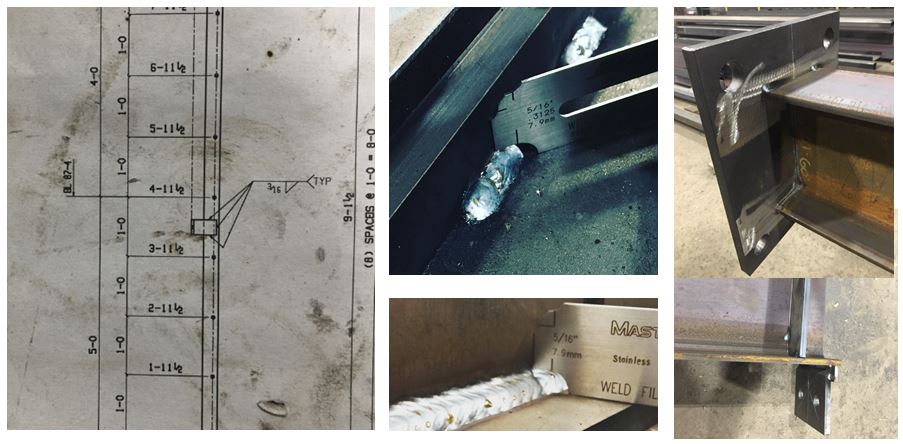
Sizing of weld should not be the responsibility of welders. However, the lack of understanding when it comes to weld design means most fab shops don’t have the knowledge necessary to make that call. So they figure “let’s just have the welders figure out the weld size, after all, that is their craft.”
Many of the shops we visit have a tremendous amount of overwelding and when we point this out to owners and their leadership team they blame the welders. Then they seemed surprised when we tell them that it is not the welders fault but their (management’s) fault. If instructions are not provided to welders in the form of welding procedures, part drawings, welding symbols and other work instructions, how can you blame them for overwelding? Or for welding to slow? Or welding too hot? Or having welding discontinuities and failures?
When we don’t provide proper instructions and force welders to make the engineering decision of determining weld size, they are not running calculations or FEA analysis or any of that stuff. They will base the weld size on many things, such as:
- Based on the thickness of the members being welded – the fillet weld leg size will match the thickness of the thickest part being welded (or the thinnest)
- Based on common shop practice (i.e. everything will be a 5/16” fillet unless otherwise specified)
- Based on experience (what they have done in the past and to their knowledge has not failed)
This situation leads to overwelding. Overwelding is extremely expensive, it reduces efficiency, and introduces quality problems such as distortion, overlap, slag inclusions and others.
When it comes to failures associated with weld sizes, it is way more common that a weld fails due to a quality problem caused by oversizing the weld than by an undersized weld. What? Yes, you read that right. Overwelding causes more failures than under sizing welds.
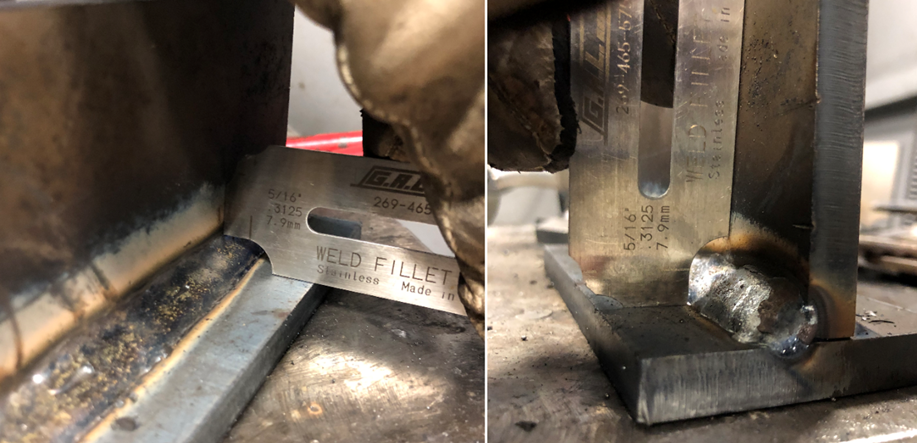
If you take a look at the structural welding code for steel (AWS D1.1) you’ll find Table 7.7 which specifies minimum fillet weld sizes. However, the minimum size has nothing to do with strength. Rather, it has to do with heat input. If a weld is too small it may have such a rapid cooling rate it can cause a hardened heat affected zone which can lead to problems.
This table exists because the design engineers that use software and other methods to calculate stresses typically find that fillet weld sizes can be as small as ⅛” or even 1/16” on material thickness of ½” or more. But a 1/16” fillet weld, other than being almost impossible to make other than with GTAW, would produce such a low heat input that rapid cooling is a concern. Thus, AWS D1.1 will say, for ½” steel the minimum fillet weld size shall be 3/16”.
But even a 3/16” fillet weld on ½” material seems too small, doesn’t it? It doesn’t look big enough. So as a welder, you don’t feel very comfortable making a 3/16” fillet weld. So you go bigger. ¼” sometimes 5/16” or even ⅜”. Making a ⅜” fillet weld on ½” material is very common. When you consider the weld could be 3/16”, you are making a weld that is 4 times bigger (in terms of volume). You just used 4 times the amount of wire, gas and labor time to make this weld. In welding, bigger welds are not always better. As a matter of fact, bigger welds are hardly ever better.
Is there overwelding going on in your facility? Have you been guilty of specifying weld sizes that are too big? What are the challenges facing you and/or your company and specifying weld sizes?
Reference: Welding Symbols Training Manual and Guide
Please note: I reserve the right to delete comments that are offensive or off-topic.