3 Key Factors Affecting the Quality and Cost of Welds
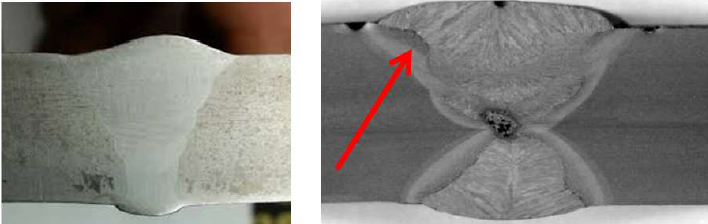
Quality and cost go hand in hand, or at least they should. Poor quality may be cheap during the fabricating process, but very costly when it comes to warranty repairs and potentially losing customers. Many of the companies we work with have seen substantial cost reductions when we help them address quality concerns. For the […]