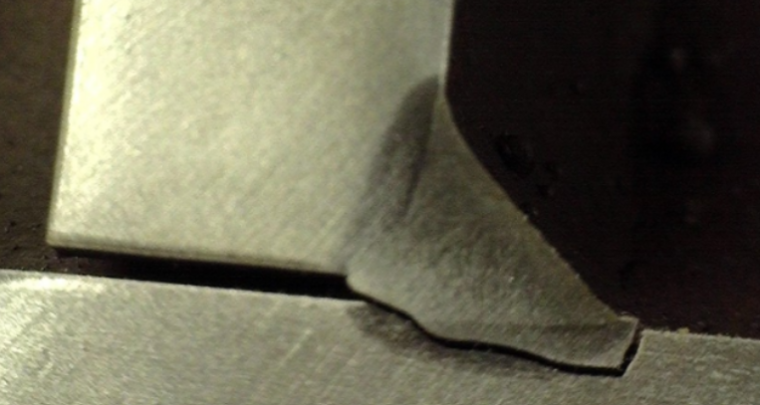
Weld failures happen all the time. Some are more serious than others in terms of cost and potential for property damage and bodily harm. If a weld failure is considered serious it typically gets a lot of attention. Forensics labs and industry experts get called to determine the root cause of the failure. It may cost thousands of dollars to figure out exactly what caused the failure.
Because of the high cost of failure analysis we typically don’t do a good job of diagnosing “minor” failures. If the weld that attaches the hinge of ramp to the frame of a utility trailer breaks we may have an unhappy customer. We go to the field, we repair our weld and go back to doing things the same way. It is of utmost importance that we evaluate every single weld failure.
Even if we are not experts, there is a lot we can find out by evaluating the failure in order to avoid future problems. Keep in mind that even experts that conduct failure analysis on a regular basis sometimes cannot come up with the root cause of the failure. Instead, they provide a list of recommendations which if followed, should prevent future failures.
One of the most important things to keep in mind when diagnosing a weld failure is that most failures are not caused by a single problem. Rather, they are a combination of many things. This is what makes failure analysis difficult at times. Many of our customers that call us in to help them determine the cause of a failure tell us that nothing in their manufacturing process changed.
The vast majority of weld failures have more than one root cause. This becomes a problem when we are trying to figure out what went wrong so that we can prevent it from happening again.
To illustrate this problem we’ll share a brief summary of a weld failure analysis we conducted for a customer a few years ago. The reported problem was a shaft failure that caused the barrel of a concrete mixer to be unable to spin. The end user lost the load of concrete and the fabricator of the truck lost a lot of money having to replace the truck. The initial evaluation from the fabricator was that the customer probably overloaded the barrel. Their solution was to make the weld with a higher tensile strength filler metal.
After our evaluation we found out that the size of the weld was not the issue. Rather, it was an engineering decision to change the welding procedure 18 months prior. The shaft was AISI 1045 material and the base plate ASTM A572 Gr 50. The AISI 1045 material requires preheating before welding. An engineer determined the welding process would generate enough preheat and costs savings would be achieved by eliminating external preheating. This of course was incorrect.
The customer said that this cannot be the issue since the change was made 18 months ago and only three trucks had failed. Our reply to that was “only three have failed so far.” They did not like this one bit. So we explained…
Preheat was required to avoid cold cracking (hydrogen induced cracking) since AISI 1045 has a high carbon content and is therefore susceptible to hydrogen induced cracking. In order to have hydrogen induced cracking we need not only a susceptible microstructure (the 1045) but also a source of hydrogen and sufficient stress. Remove one of these three and nothing will happen.

In order for hydrogen-induced cracking to occur all three factors need to be present. Eliminate one and it can’t happen.
Eliminating preheat provided a susceptible microstructure (rapid cooling of a steel with high carbon creates martensite, which is very hard and brittle and conducive to hydrogen cracking). However, a low hydrogen welding process (GMAW) was used to weld the part and the in-service stress was well below what would be needed to cause cracking. So most of the trucks had shafts that were hard and brittle but because they used a low hydrogen process and the shaft was not overloaded they had not failed.
The failed part we evaluated showed a welding discontinuity. It has overlap. In an attempt to make a big weld in the 2F (horizontal) position, the welder’s travel speed was too slow and gravity made the weld sag and create overlap.
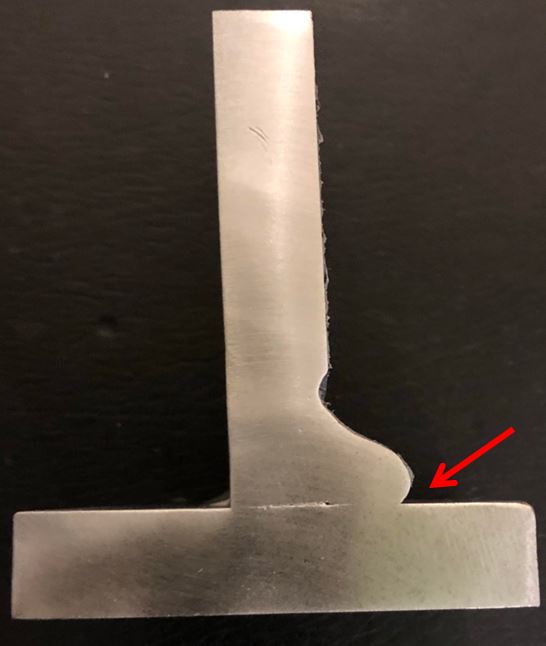
The red arrow indicates the overlap in this fillet weld cross section. Overlap is typically cause for rejecting a weld since it is a stress riser.
Overlap is discontinuity that can be nearly as detrimental as a crack. It creates a stress riser which magnifies any applied stress. This overlap created a situation where we had surpassed a threshold level of stress at which point hydrogen induced cracking was possible. We now have discovered 2 out of the 3 issues that must be present for hydrogen cracking.
The last item necessary was the presence of enough hydrogen. Upon inspection of new parts being built (welding of shaft to base plate) we noticed that the bin in which the shafts were stored had a floor which was covered in grease. So the parts at the bottom of the bin had a lot of grease (hydrocarbons) that was not always cleaned. And that was the source of hydrogen.
So out of the more than 300 trucks that were built it was very likely that more than one had these three issues. The overlap caused a stress riser. This did not lead to an immediate failure, rather it was a failure due to fatigue. Fatigue failures have three phases:
- Crack initiation – facilitated by a weld discontinuity such as crater cracks, undercut or overlap.
- Crack growth -due to cyclic loading which may take months or even years to reach a critical crack length, and
- Brittle fracture – after the crack reaches a critical size the remaining metal is not sufficient to sustain the load and brittle fracture occurs. In brittle fracture the crack that was growing as slow as less than 1 inch per year now grows at over 7,000 feet per second!

Image of the fractured surface of the shaft. The failure was in the HAZ adjacent to a spot in the weld with overlap. The surface also indicates that this failure occurred over time due to cyclic loading. Crack propagated slowly over time until it reached a critical length and then the part experienced brittle fracture.
This customer was faced with a dilemma. Do they recall all the trucks that were built in the last 18 months or wait for failures to occur and deal with expensive repairs and unhappy customers. Both alternatives represented high costs.
The moral of this long article is this: weld failures are rarely caused by a single factor. Always consider all aspects of the process and possible causes. Never assume that nothing has changed. Change can come from the manufacturing process, from changes to the base material and from other factors associated with the use of the product.
This was a great article. I have just recently found this website am finding all the articles to be interesting reads.
As a welder for over 25 years and now a repair shop manager, I have always found it ‘fun’ to try evaluate the reasons of weld failures, as you have shown spotting a cold lap or an undercut then seeing the slow, periodic progression of cracks in the color of oxidation and then the final failure. Or seeing high speed failures and trying the track the reason. Was it a bad weld design, was the wrong filler used? Pre heat / post heat? Material incompatibility?………………
Thank you for your insights!
Thanks for your comments Wayne. You are right, it can be fun to try to do the analysis. Maybe one day there will be a CSI: Welding show on TV, hahaha.