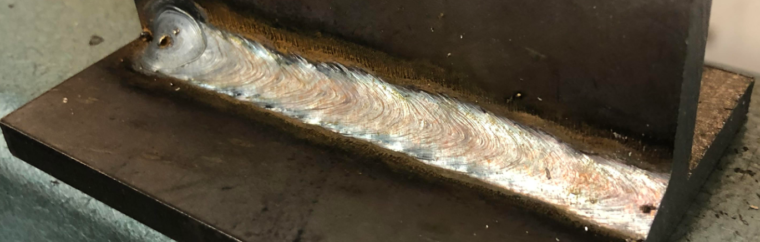
Today we received two different requests for help pertaining to shielding gas selection. The first caller requested a chart that tells them what materials can be welded with the different shielding gases that they had. They wanted a chart that can be provided to the welders to make sure they used the right gas on the right material. The second caller asked if they could use their shielding gas used for stainless (98% Argon/2% Carbon Dioxide) on carbon steel.
For the second caller we were able to weld some samples using the 98/2 shielding gas on steel and showed them the effects on penetration and bead profile. We will cover this on our post for next week – Danger of Using the Wrong Shielding Gas for GMAW.
Our response to the first caller was that shielding gas selection is made based on more than just base material alone. Developing welding procedures specifications is a process that considers base metal, base metal conditions, joint type, welding position, material thickness, and many more requirements. The selection of a shielding gas is therefore affected by these requirements.
However, we get into trouble because you can make welds look good regardless of what gas you use, for the most part. For example, you can weld mild steel with any of the following shielding gases:
- 100% Carbon Dioxide
- 75% Argon / 25% Carbon Dioxide (75/25)
- 90% Argon / 10% Carbon Dioxide (90/10)
- 95% Argon / 5% Oxygen (95/5)
- And many other mixtures
Although all of the above can be used on mild steel you must make your selection based on the application. If your base material is covered in rust and mill scale then the 95/5 mix is a terrible choice. But if we are welding on clean sheet metal than this 95/5 is adequate. 75/25 is an excellent choice for sheet metal as well since it is good with the short circuit mode of metal transfer, but should not be your preferred choice for welding heavy sections of steel (for the GMAW process). However, if you use flux-cored wire (FCAW process) then you can use 75/25 without concern for material thickness.
As you can see, there are certain considerations when selecting the right gas. We are in the process of creating a comprehensive chart that will cover not just the gases above but several more. For now, this is the quick reference guide we provided to our customer while the chart is created.
This chart should be used simply as a general guideline. All welding procedures should be qualified by testing or prequalified in conformance with the applicable structural welding code.
It is very important to know that just because a weld looks good on the outside it does not guarantee quality. Take a look at the image below:

This weld was made on 1/4″ A36 steel with 0.035″ ER70S-6 and 98%Ar/2%CO2 shielding gas in spray transfer. This shielding gas mixture is for GMAW of stainless steels.
Our next article will show what this weld looks like on the inside.
Argon gas is used in TIG welding and can we use same gas for mig welding? I’m much confused that what’s the main difference between them on mig and tig welding? Is it same on these two methods?
Argon is a inert gas. It can be mixed with Oxygen or Carbon Dioxide in the GMAW process, but for GTAW (TIG) the gas has to be 100% inert.
Dear sir,
Please share the advantages and disadvantages of 100% CO2 as a shielding gas.
100% CO2’s main advantage is that it is much less expensive than Argon and other gases. CO2 also does better when welding over mill scale, rust and other surface contaminants. However, you can get these benefits with as little as 10 to 15% CO2. Some disadvantages of 100% CO2 is that it does not facilitate spray transfer. It also generates significantly more spatter than an a higher argon mixture.
Recommendations for shielding gases used in TIG welding of different stainless steels are given in the table. For plasma-arc welding, the gas types with hydrogen additions in the table are mostly used as plasma gas, and pure argon as shielding gas.