Importance of Macro Etch Testing of Welds
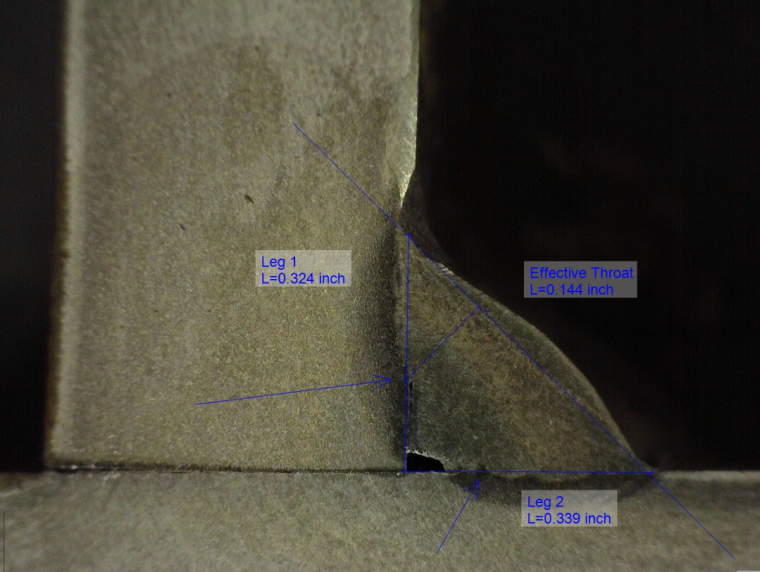
Macro etch tests are commonly done as part of qualification tests for welders and welding procedures. This test is relatively easy to do and does not require complex or expensive equipment. However, very few fabricators ever perform this test. A macro etch test can serve as verification that a change on how something is welded […]