Category Archives: Cost Reduction
6 Challenges When Increasing Deposition Rates
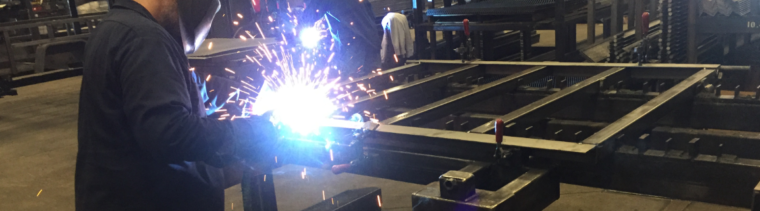
It is not a secret that increasing our deposition rates, measured in pounds per hour (kg per hour in metric units), can result in increased productivity. Deposition rate is the rate at which we are depositing weld metal. It is different from the melt-off rate. Melt-off rate is the rate at which we consume our […]
Who is responsible for determining weld size?
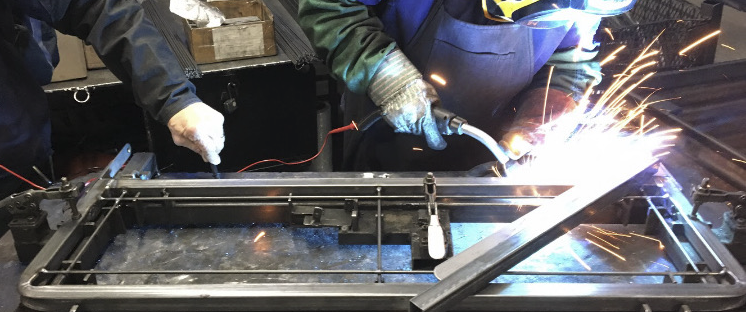
Who determines what size a weld should be? This is a question we ask many of our customers. And we never seem to get a straight answer. In a perfect world, the design engineer should specify all weld sizes and clearly communicate this through welding symbols on the print. But that is hardly ever the […]
3 Mistakes that lead to distortion in welding
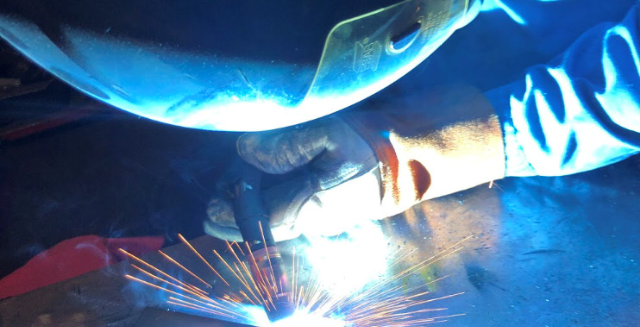
Distortion caused by the heating and cooling cycles of welding is extremely problematic. It can place structures out of dimensional tolerance creating costly rework. In some cases parts need to be scrapped. Understanding the causes of distortion and the properties of the metal being welded are an absolute necessity for those managing welding operations. There […]
Pick Your Prequalified Welding Procedures Carefully
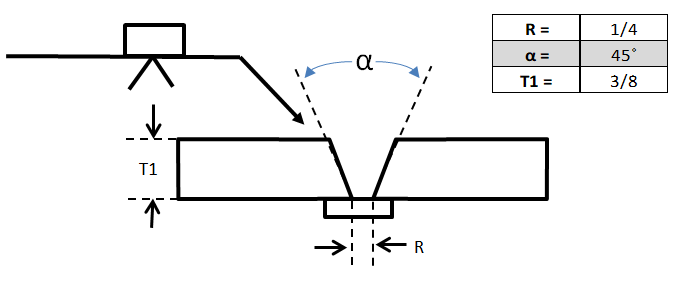
If you work with AWS D1.1 you are probably familiar with the use of prequalified welding procedures. The use of prequalified WPSs provides many benefits to the fabricator, one of which is costs savings due being exempt from having to perform costly testing to qualify the welding procedure. However, if you are looking to save […]
3 Key Factors Affecting the Quality and Cost of Welds
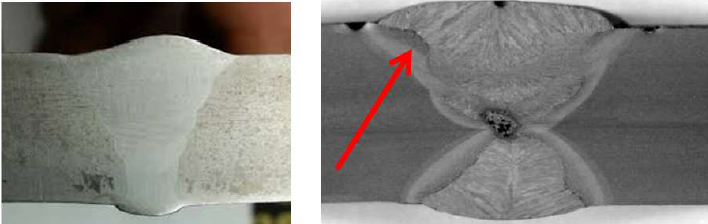
Quality and cost go hand in hand, or at least they should. Poor quality may be cheap during the fabricating process, but very costly when it comes to warranty repairs and potentially losing customers. Many of the companies we work with have seen substantial cost reductions when we help them address quality concerns. For the […]
What Causes Welding Spatter
17 reasons why you are getting spatter in your welding operations
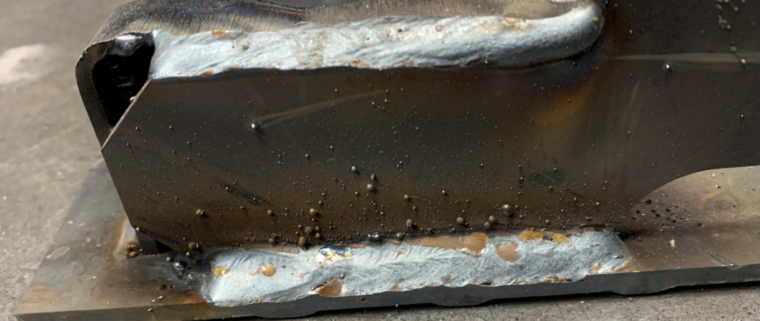
Spatter is present in welding. It’s all over welding. But it doesn’t have to be. Spatter costs fabricators millions of dollars every year. Its removal constitutes rework that significantly and negatively impacts productivity. Many fabricators work under the assumption that spatter is a necessary evil, a part of welding. However, this couldn’t be further from […]
7 Things to Consider When Choosing the Best Welding Process for your Welding Procedure
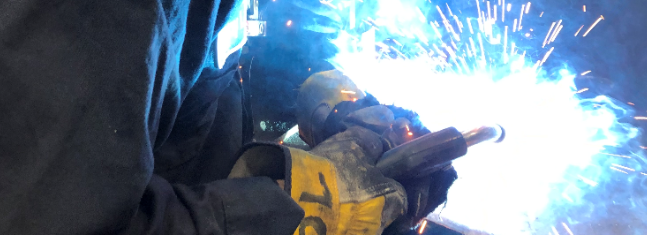
Selecting the best welding process is a critical step in developing a welding procedure that attains the desired quality and optimizes productivity. Many times we look for the welding process that can give us the highest deposition rate to optimize productivity. However, every welding process has limitations. For example, submerged arc welding (SAW) has extremely […]
Welding Hot Rolled vs Cold Rolled Steel
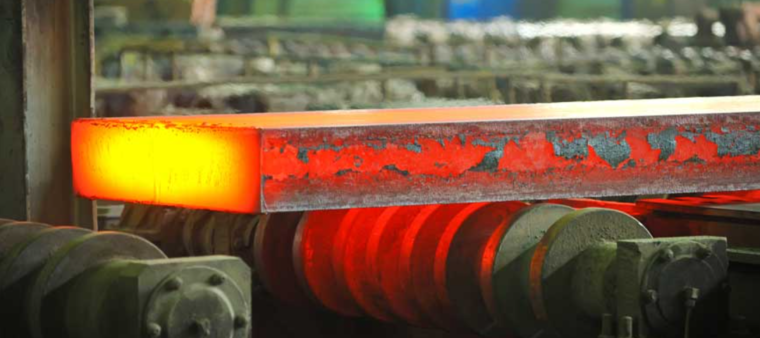
Both hot rolled and cold rolled steels can easily be welded. However, there are differences between the two that will impact which you choose to use. Making this choice depends on several factors such as strength, surface finish, dimensional accuracy and cost. To understand the difference between hot rolled and cold rolled steel and how […]
3 Keys to Troubleshooting Welding Problems
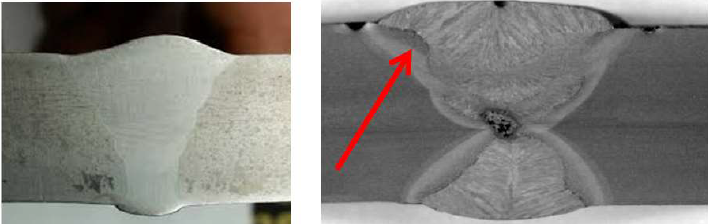
Troubleshooting of welds and other welding problems increases costs in welding, causes delays and affects weld quality. Even a moderate understanding of welding problems, their symptoms, causes and potential solutions can help tremendously. The more informed you are the better. To successfully troubleshoot and fix welding discontinuities, welding defects and other welding problems we need […]