Category Archives: Processes
The Importance of Weld Repair Procedures
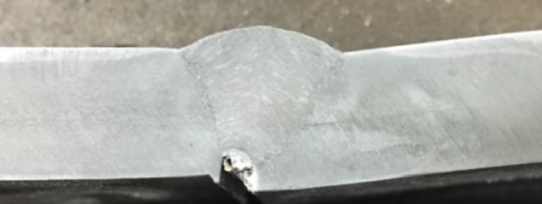
A repair procedure is necessary any time there is a defect in welding that must be corrected. The repair procedure is not just a welding procedure specification, but rather a set of instructions and rules on how to repair different types of defects. There is no standard format for a repair procedure, or a standard […]
AWS D1.1 Prequalified Welding Procedures
Prequalified WPSs for GMAW, MCAW, SMAW, FCAW & FCAW-S
Prequalified welding procedures must adhere to the strict requiremnts of the welding codes which permit their use. AWS D1.1 Structural Welding Code (Steel) is one that allows their use. Prequalified WPSs are exempt from testing becasue there is reasonable assurance that as long as all the requirements are met the deposited weld will be sound […]
7 Reasons to Consider Stick Welding Over Other Processes
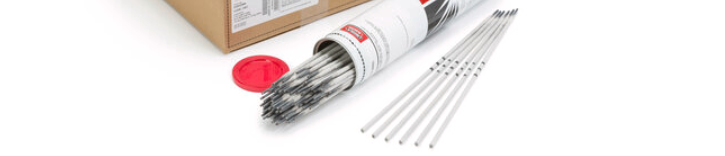
Shielded metal arc welding (SMAW), or what is commonly referred to as “stick welding,” is one of the oldest welding processes. Despite being one of the first welding processes developed, it remains one of the most used welding process worldwide. If you have been working in a fabrication shop for years using advanced GMAW (mig) […]
3 Ways to Improve Out of Position Welding

Welding out of position does not need to be overly complicated. It does present a challenge, especially for inexperienced welders, but there are things we can do to make this go well for everyone. When we talk about out of position welding we mean welding vertical up or overhead. Vertical down is also out of […]
Storing and Re-drying Low Hydrogen Electrodes
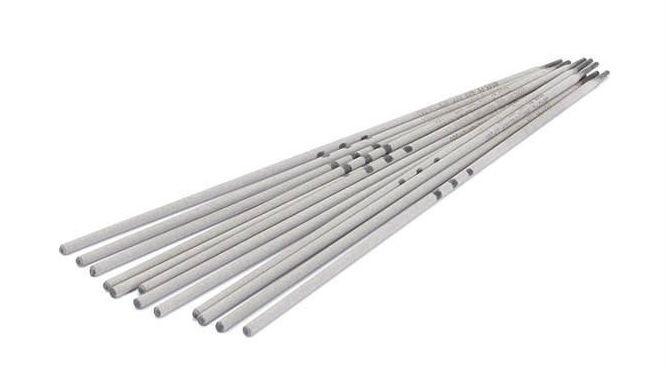
One of the dangers we should be aware of when welding high strength steels or even thick sections of low carbon steel is hydrogen induced cracking. Hydrogen induced cracking, also called hydrogen assisted cracking and cold cracking, is caused when three conditions are present. First, we need a susceptible microstructure (base material related). Second, we […]
Causes of Porosity in Submerged Arc Welds
Submerged arc welding is typically done automatically, meaning it is not done by hand, but rather set up as hard automation. The operator simply controls the welding machine and torch position to obtain the desired results. Typically,the system is run by an operator, not a welder. So when problems come up, the operator may not […]
Effects of Voltage on Weld Quality
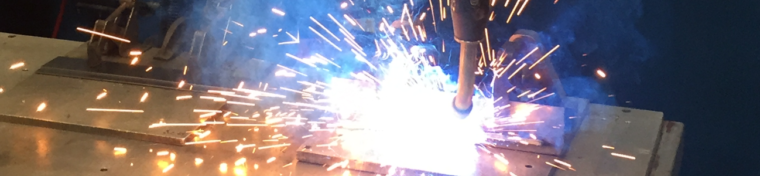
Voltage is one of the most important variables in a welding procedure. It is also one that is sometimes misunderstood. You may ask five welders what effect voltage has on a weld and you may get five different answers. This is because voltage can do a lot of things, some good and some bad. Understanding […]
FCAW prequalified welding procedures and their limitations
Dangers even if you follow all the requirements of AWS D1.1
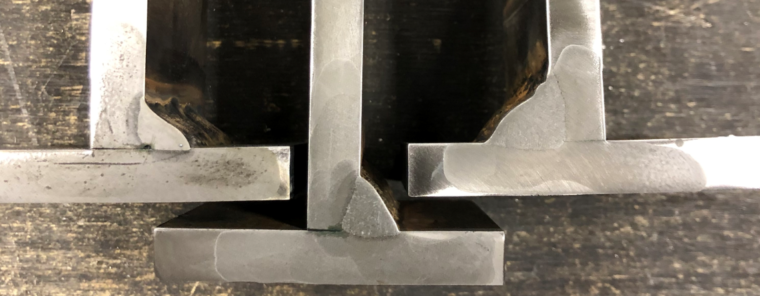
The use of prequalified welding procedures has many advantages as well as many disadvantages. One danger of using prequalified welding procedures is that AWS D1.1 allows for quite a bit of freedom in weld sizes. If you look at Table 5.1 –Prequalified WPS Requirements of AWS D1.1/D1.1M:2020 Structural Welding Code (Steel) you’ll see that in […]
Which is the best shielding gas for MIG welding?
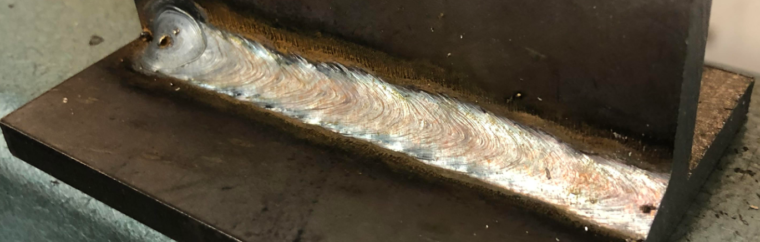
Today we received two different requests for help pertaining to shielding gas selection. The first caller requested a chart that tells them what materials can be welded with the different shielding gases that they had. They wanted a chart that can be provided to the welders to make sure they used the right gas on […]