Why You Must Have Welding Procedure Specifications
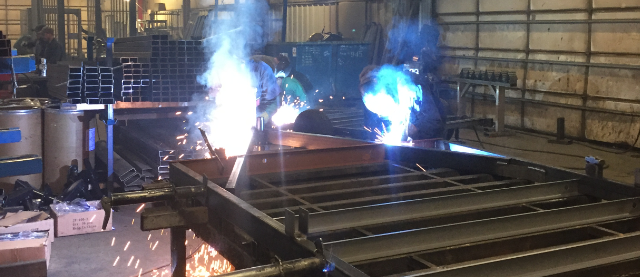
Our previous article discussed the importance of having a specification for weld quality. In this article we’re talking about the importance of one of its basic components: Welding Procedure Specifications (WPSs). Many fabricators don’t have WPSs. They rely in the experience of their welders to select the right parameters. As much as we want every […]