Demystifying Fatigue Fractures in Welding: The 3 Stages of Fatigue Fracture
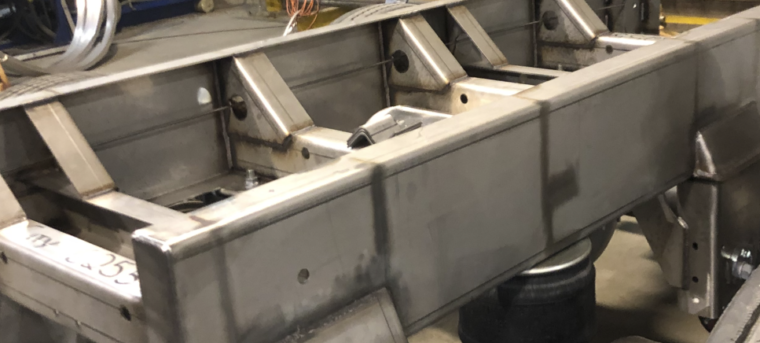
In today’s article we’ll be discussing a critical aspect of welding which is crucial in ensuring the safety and long useful life of structures. When engineers conduct a fitness for service analysis of structures they are looking for flaws. These flaws may be cracks, loose bolts, deformations, rust damage (thinning of structural members) and other […]