What is Stress Relieving and Why We Need It
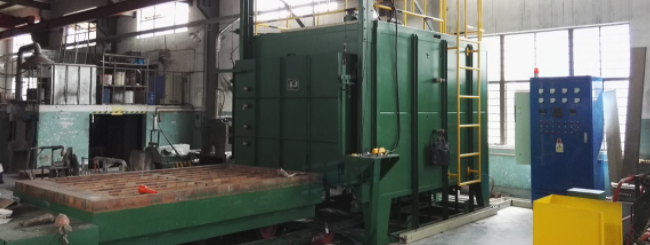
Stress relieving is a form of post weld heat treatment. In stress relieving we heat a material to a specific temperature; hold it at this temperature for a specified amount of time in order to reduce or eliminate residual stresses; and then cool it at a slow enough rate to prevent these stresses from redeveloping. […]