Tag Archives: WPS
Understanding the Difference between Qualified and Prequalified Welding Procedures
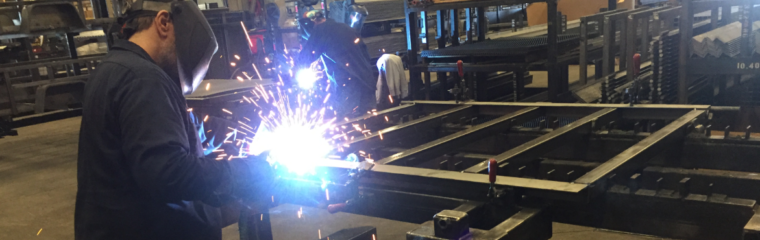
One of the most common questions we get around the topic of welding procedure qualification is regarding the differences between qualified and prequalified welding procedures. The main question is typically: is one better than the other? Before we answer this question, let’s first discuss the need for qualified, or prequalified, welding procedures. If you have […]
The Importance of Contact Tip to Work Distance in GMAW
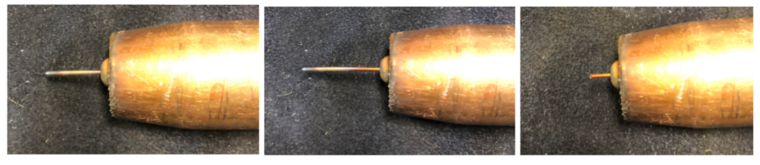
If you look at any of the structural welding codes you’ll notice that contact-tip-to-work-distance (CTTWD) is a variable which must be listed in welding procedure specifications (WPSs). However, it is not an essential variable, meaning that changes to CTTWD of any amount do not require requalification. This can seem puzzling to some, especially those […]
Pick Your Prequalified Welding Procedures Carefully
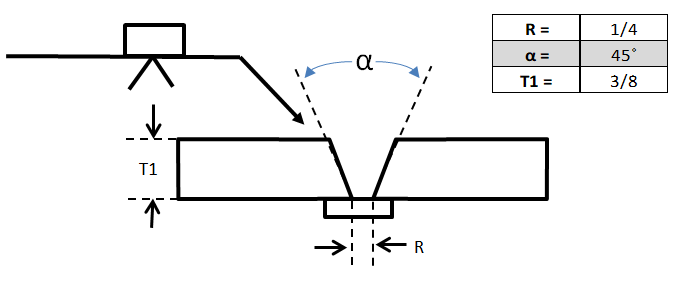
If you work with AWS D1.1 you are probably familiar with the use of prequalified welding procedures. The use of prequalified WPSs provides many benefits to the fabricator, one of which is costs savings due being exempt from having to perform costly testing to qualify the welding procedure. However, if you are looking to save […]
How To Qualify A Welding Procedure
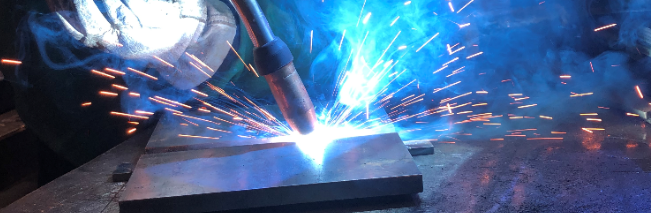
Whenever you hear that a welding procedure needs to be qualified it simply means that its suitability for use in a welded structure needs to be proven by testing. This means that the welding procedure must be capable of producing sound welds. But what are sound welds? Sound welds are welds that will perform in […]
How to get a Qualified Welding Procedure Quickly
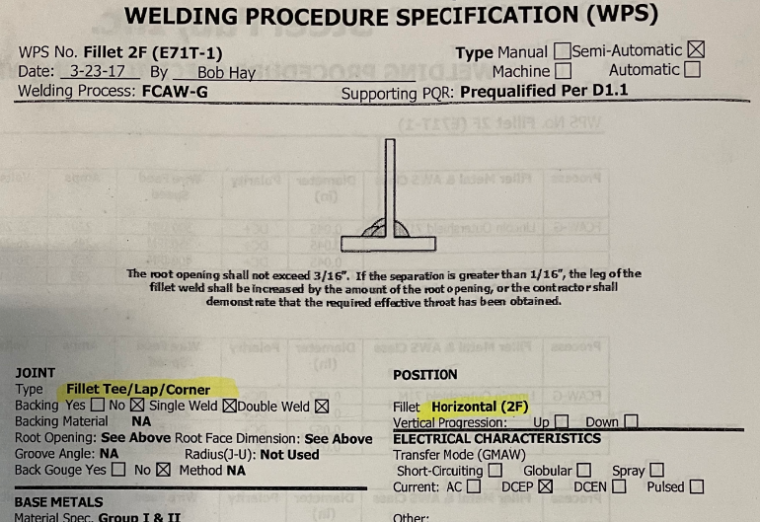
Have you ever been in a situation in which you need a qualified welding procedure immediately? Maybe you just failed an audit and have to halt production until a valid welding procedure is provided. Or maybe you’re just in a hurry to get started with a new job. Regardless of the reason you need the […]
AWS D1.1 Prequalified Welding Procedures
Prequalified WPSs for GMAW, MCAW, SMAW, FCAW & FCAW-S
Prequalified welding procedures must adhere to the strict requiremnts of the welding codes which permit their use. AWS D1.1 Structural Welding Code (Steel) is one that allows their use. Prequalified WPSs are exempt from testing becasue there is reasonable assurance that as long as all the requirements are met the deposited weld will be sound […]
5 Questions and Answers You Must Know for the CWI Exam
And fundamental principles for the fabrication of steel structures
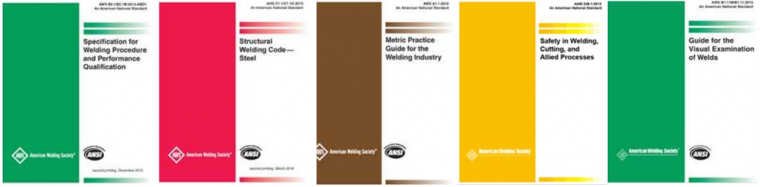
If you have taken or hope to take the CWI exam you probably have searched for some practice exam questions. In practicing for the code book portion of the test you may have come across a few questions for which you could find the answer, but didn’t really understand the importance of the question or […]
21 Changes to PQR Essential Variables that Require WPS Requalification
Have you ever seen a welding procedure specification with established amperage ranging from 200 to 550 amps? Or voltage ranging from 21 to 29 volts? Or some other variable with a huge window? This is all too common, but extremely dangerous. Why? Because changes to essential variables beyond that which is reasonable will affect the […]
Frequently Asked Questions about Prequalified Welding Procedures
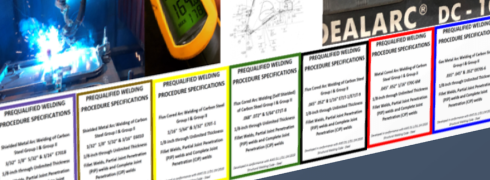
The following FAQ are related to 322 Prequalified Welding Procedure Specifications for Steel Fabricators. To learn more or to get your copy simply click here Is this a physical book? No. The procedures are provided as digital files (PDF) and are available for immediate download. The user has the option to print the files […]