In the January 2011 AWS publication of Inspection Trends, Albert J. Moore Jr. states that “other than the measuring tape, the fillet weld gage is the most used measuring device in the welding inspector’s kit.” We agree with this statement, but are also convinced that the fillet weld gage is THE most underused tool by […]
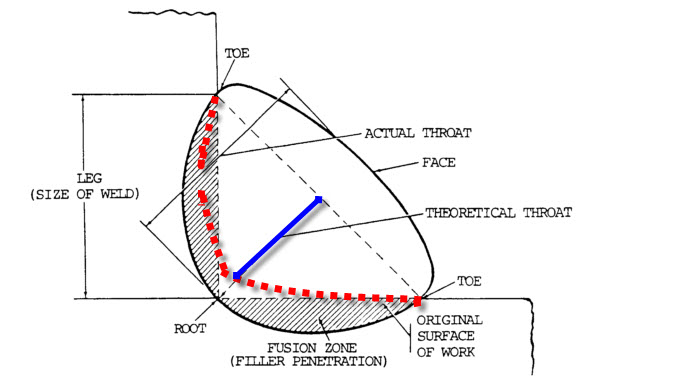
When weld sizes are determined by design engineers, the theoretical throat is used to calculate weld strength which in turn gives our leg size (for fillet welds). This means that the desired strength of a weld is achieved only if we attain fusion to the root and side walls. The terms fusion and penetration are used […]
Most manufacturing facilities use 1.5 to 3 times as much shielding gas as they should. The reasons for this can be found in a previous post: Control Your Shielding Gas Usage. Before doing all the checks to see if you have leaks or other problems there is a simple way to get an idea of whether or not […]
Welding joints vary widely but can be traced back to a few basic joint types. Typically we hear terms like fillet weld, butt weld, lap weld or corner weld. These are all all joints but within these there are variations. Below we outline the joints and provide a graphical representation. These joint types are categorized […]
A weld failure is never good. Whether a weld cracks on a truck’s axle or on the post holding your house’s fence, there are always consequences. Hopefully the consequences are limited to time and money. Unfortunately, weld failures can cause injury. Welds can fail due to design flaws, but the majority of weld failures occur […]
A customer recently questioned our advice of going to bulk packaging for his mig wire. He stated that paying an extra $0.10 per pound was the complete opposite of what he wanted to do. We explained how spending a little more per pound would translate into significant savings for his company. Typically the bigger the package the […]
What alloy is used to weld stainless steel to carbon steel?
This is one of the most frequent questions we receive. If you are welding mild steel to stainless the recommended alloy is 309L or 309Lsi. This is true even if the stainless base material is 304, 308 or even 316.
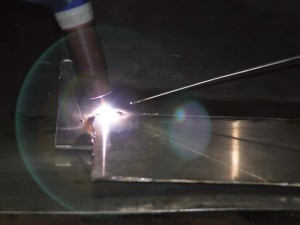
For joining stainless to mild steel use a 309L filler
A not so common question is whether carbon steel can be welded with 308L. There are a few reasons why you would want to weld carbon steel with a stainless filler, most of them have to do with not having to change out the wire in robotic applications for short runs of mild steel product. It makes sense that 308 would be sufficient, but this is not always the case. A 308 filler would yield a deposit that when mixed with carbon steel would be similar to a 410 stainless deposit. This would be a weld deposit that may be too brittle for the application. The recommended filler in this case would also be 309L since when mixed with carbon steel it yields a deposit similar to a 308L deposit.
For more information on welding stainless steels you can read 5 Common Mistakes Made Welding Stainless Steel.
Over the past several years we have seen a tremendous increase in the amount of automation in our everyday lives. This is no different in the welding industry. Gone are the days when you needed to make 50,000 identical parts to justify a robot. With prices going down and quality, reliability and flexibility going up, […]
A common question in the field is which wire type will provide the best deposition rate. In one of our earlier posts “Calculating Deposition Rate for Solid Wires” we discussed deposition rates strictly for solid wires. Here we will talk about deposition rates across wire types – mainly solid wire, metal-cored wire and flux-cored wire. […]
Even for those of us dealing with welding all day every day it is difficult to remember the welding position nomenclature. So here is a quick cheat sheet. Fillet Weld Positions Groove Weld Positions Pipe Weld Positions Which do you consider to be the most challenging welding position?