What is a Qualified Welding Procedure?
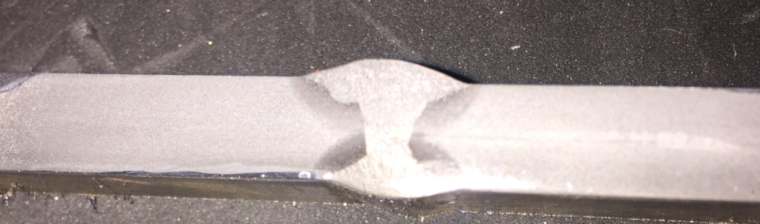
A qualified welding procedure is a welding procedure that has been proven to produce sound welds after undergoing extensive testing. When using structural welding codes, these tests include both destructive and nondestructive tests. Some of these tests are: Visual examination Macroetch Break test Bend test Ultrasonic inspection Radiographic inspection Hardness test Tensile test The reason […]