Key Components of Effective Welder Training Programs
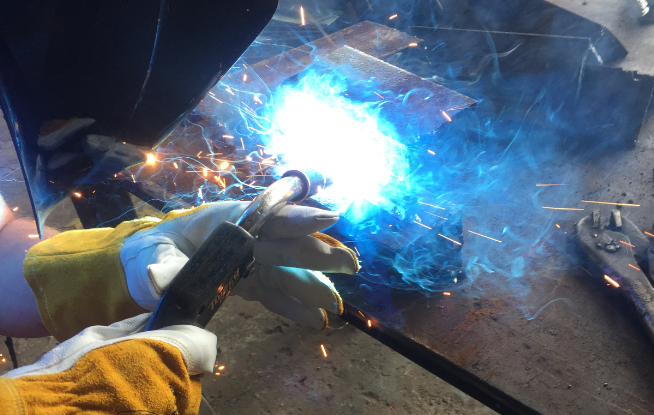
Continuous learning is something that is very important for both personal and professional development. This applies to all industries and to all positions. The welding industry, as many of its counterparts, is challenged with a workforce that is lacking the skills necessary to do the job. This is driven by the increased demand for welders, […]