Rule of Thumb for Fillet Weld Sizes
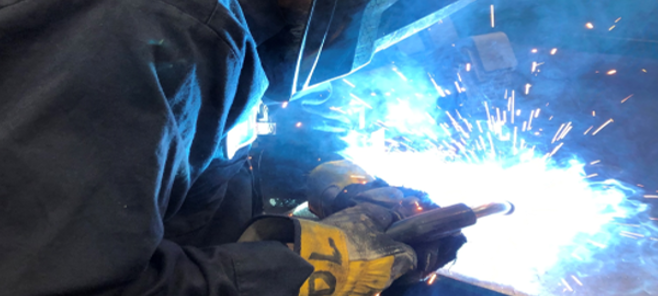
Many fabricators can lower their welding costs significantly if they paid close attention to weld sizes. If a print calls for a ¼” fillet weld and in production you make a 5/16” fillet weld, you are overwelding by 56%! If the print calls for a 3/16” fillet, the 5/16” fillet weld you deposit would be […]