Troubleshooting Welding Burn-through
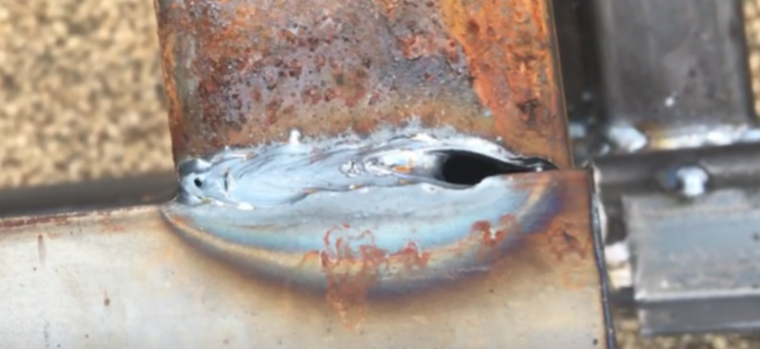
Burn-through is a common defect in welding of light gauge materials. It is typically results in costly scrapping of parts since it can be difficult to fix. Or, if left in place when there are not structural integrity concerns it looks awful and portrays extremely poor quality. The following is an excerpt from our guide: […]