Category Archives: Qualification
Pick Your Prequalified Welding Procedures Carefully
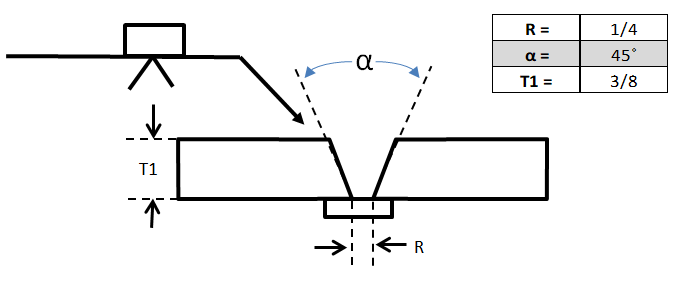
If you work with AWS D1.1 you are probably familiar with the use of prequalified welding procedures. The use of prequalified WPSs provides many benefits to the fabricator, one of which is costs savings due being exempt from having to perform costly testing to qualify the welding procedure. However, if you are looking to save […]
How To Qualify A Welding Procedure
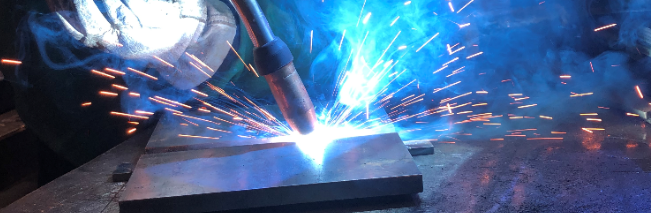
Whenever you hear that a welding procedure needs to be qualified it simply means that its suitability for use in a welded structure needs to be proven by testing. This means that the welding procedure must be capable of producing sound welds. But what are sound welds? Sound welds are welds that will perform in […]
How to get a Qualified Welding Procedure Quickly
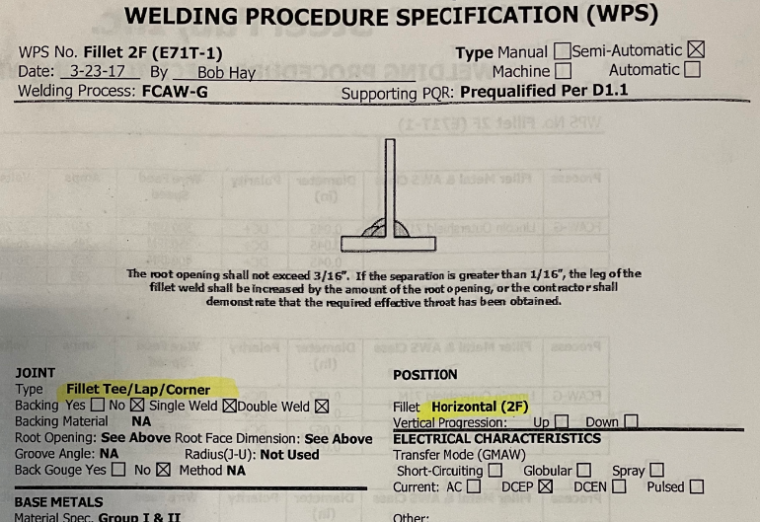
Have you ever been in a situation in which you need a qualified welding procedure immediately? Maybe you just failed an audit and have to halt production until a valid welding procedure is provided. Or maybe you’re just in a hurry to get started with a new job. Regardless of the reason you need the […]
5 Methods to Determine Preheat Temperature
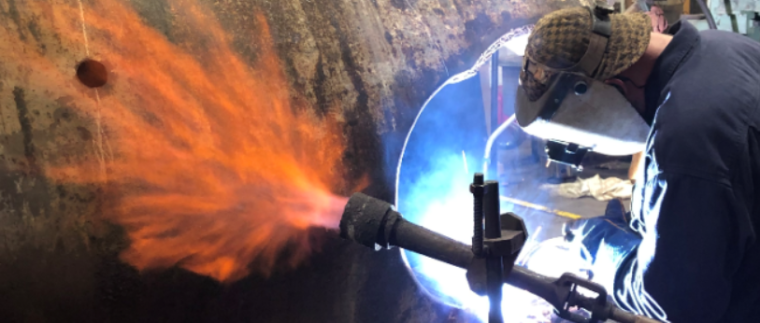
Preheat is used when a base material, due to its chemical composition, thickness or level or restraint, is susceptible to cold cracking (hydrogen induced cracking). Knowing what temperature to preheat your base metal is sometimes a complicated matter. You may hear people say “preheat to 300F to be safe.” The reality is that 300F may […]
AWS D1.1 Prequalified Welding Procedures
Prequalified WPSs for GMAW, MCAW, SMAW, FCAW & FCAW-S
Prequalified welding procedures must adhere to the strict requiremnts of the welding codes which permit their use. AWS D1.1 Structural Welding Code (Steel) is one that allows their use. Prequalified WPSs are exempt from testing becasue there is reasonable assurance that as long as all the requirements are met the deposited weld will be sound […]
5 Questions and Answers You Must Know for the CWI Exam
And fundamental principles for the fabrication of steel structures
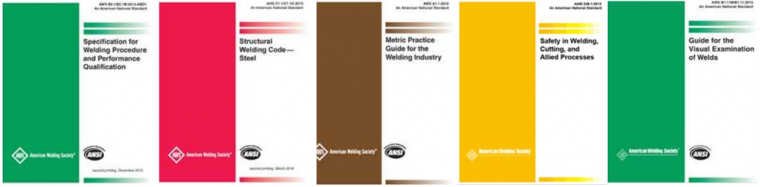
If you have taken or hope to take the CWI exam you probably have searched for some practice exam questions. In practicing for the code book portion of the test you may have come across a few questions for which you could find the answer, but didn’t really understand the importance of the question or […]
What To Do When Welding Codes Are Not Clear
Or when the code does not provide enough information to make an important decision
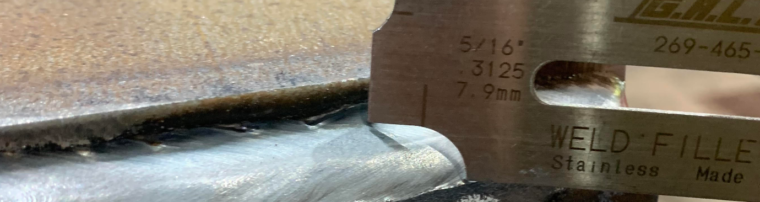
If you are a CWI, welding engineer or serve in a capacity that requires you to use and interpret welding codes, you probably have run into instances where the code is not very clear. Many of the questions we receive from our readers deal with interpreting codes and standards. Many times it is not about […]
21 Changes to PQR Essential Variables that Require WPS Requalification
Have you ever seen a welding procedure specification with established amperage ranging from 200 to 550 amps? Or voltage ranging from 21 to 29 volts? Or some other variable with a huge window? This is all too common, but extremely dangerous. Why? Because changes to essential variables beyond that which is reasonable will affect the […]
What is a Qualified Welding Procedure?
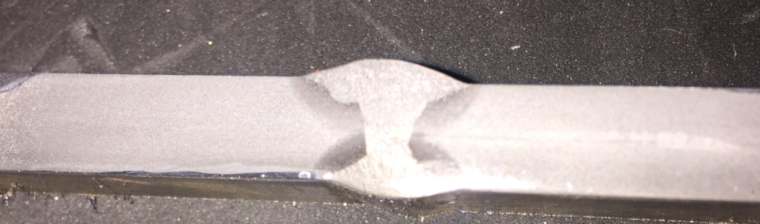
A qualified welding procedure is a welding procedure that has been proven to produce sound welds after undergoing extensive testing. When using structural welding codes, these tests include both destructive and nondestructive tests. Some of these tests are: Visual examination Macroetch Break test Bend test Ultrasonic inspection Radiographic inspection Hardness test Tensile test The reason […]