Are Concave Fillet Welds Bad?
You may be surprised to know that sometimes they are desired
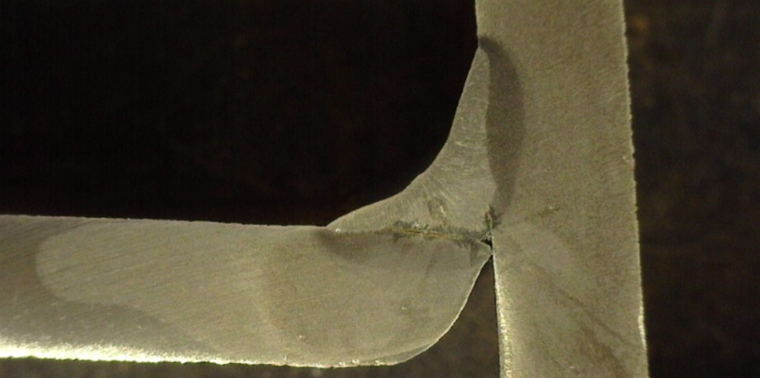
The following is an exerpt from: TROUBLESHOOTING FOR NON-WELDING ENGINEERS There is nothing wrong with concave welds so long as they attain the desired throat dimension. AWS D1.1/D1.1M:2020 Structural Welding Code (Steel) states that “there is no restriction on concavity as long as minimum weld size (considering both leg and throat) is achieved.” Concave welds […]