Why More Customers are Requiring Qualified Welding procedures
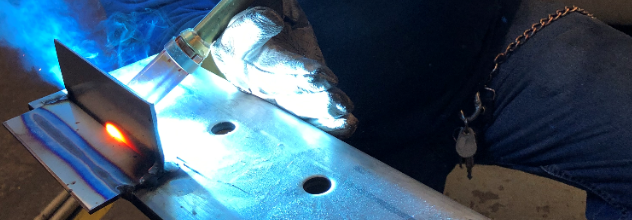
If you own or work at a job shop you may have noticed an increase in the number of customers that require the use of qualified welding procedures to build their products. Some fabricators are even getting this request from long time customers who never required them in the past. So why is this? The […]